In this article, we will discuss the pros and cons of a Wire-Wound Vs Thin-Film resistance temperature detector. A Resistance Temperature Detector (RTD) is also known as a resistance thermometer. A temperature transmitter is an electronic device that is used to determine the temperature by measuring the resistance of the RTD or thermocouple.
The resistance of the RTD changes with the change in temperature. RTD has a Positive Temperature Coefficient (PTC), which means the resistance of RTD increases with the increase in temperature.
The measuring range of the RTD is from -250°C to 1000°C. RTD has very high accuracy.
The materials used in making RTD can be platinum, nickel, copper, nickel-iron, etc. The most commonly used materials are PT100 (PT stands for Platinum) and PT1000.
Construction of Resistance Temperature Detector or RTD:
There are two types of construction of RTD:
- Wirewound resistance temperature detector
- Thin-Film resistance temperature detector
Both the RTD types have different properties. Both the RTD types have their own pros and cons. They both are efficient and operation-safe. The selection is based on various aspects, especially the process environment.
Wire Wound Resistance Temperature Detectors:
In the wire-wound type of RTD, the sensing element consists of a small coil of ultra-thin wire (typically platinum). This wire coil can be packaged inside a ceramic or a glass tube the wire can be wound around the outside of a ceramic or glass housing material. This is the most common type of construction. Wire wound RTD sensing elements can easily be made into PT100 RTD by mounting them inside the metal tubes or the sheaths. It protects them from their surroundings and increases their durability. Wire wound RTD can also be fitted into the custom housings.
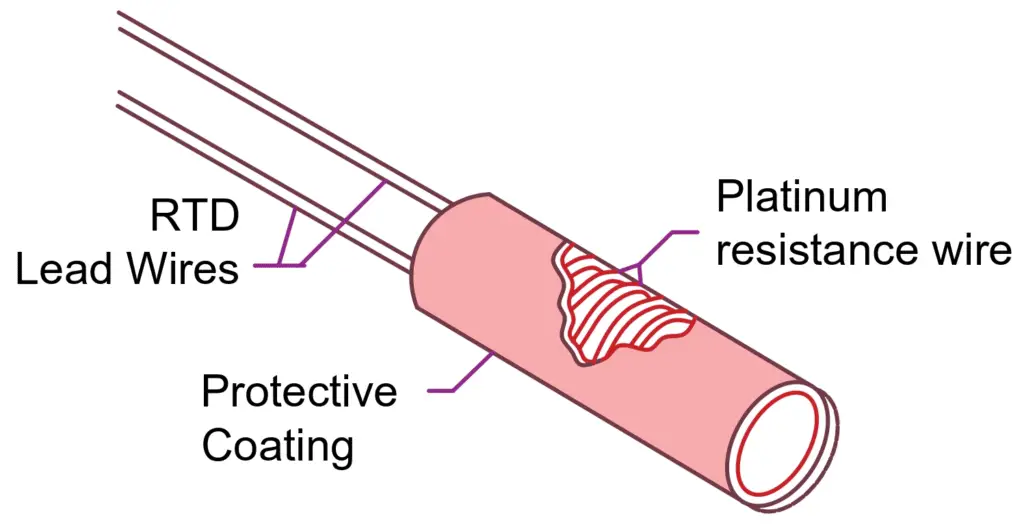
Advantages of wire-wound RTDs:
- Wire wound type of RTDs (specifically, the inner-coil type) is the most accurate type of RTD.
- The wire-wound RTD with the glass cores can readily be immersed in many liquids.
- The wire-wound RTDs with ceramic cores can be used to accurately measure extremely high temperatures.
Disadvantages of wire-wound RTDs
- Wire wound RTDs are more expensive to manufacture than thin-film types, requiring skilled labor and advanced assembly facilities.
- Wire wound RTD also tends to be more vibration-sensitive.
- Wire wound RTD is costlier as compared to thin-film RTD.
Thin-Film Resistance Temperature Detectors:
The thin-film RTD elements are made by depositing a very thin layer of metal (usually platinum) onto a ceramic substrate material. The metal film is cut by the laser or etched into an electrical circuit pattern which provides it the specified amount of resistance. The lead wires are then sealed together and a thin protective glass coating is applied to the entire element
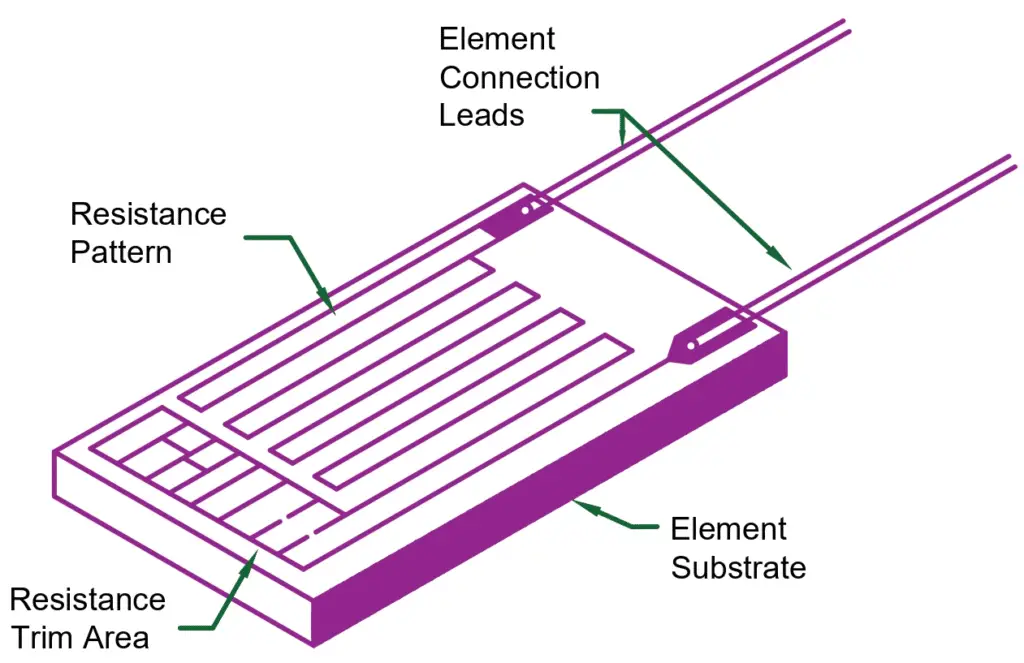
Advantages of Thin wire RTDs
- The thin wire type of RTD is popular because of its ruggedness.
- The thin wire type of RTD has good reliability.
- This type of RTD has a low cost.
- Thin-film elements are more resistant to getting damage from shock or vibration than other types of RTDs.
- The thin wire type of RTD has a flat profile which helps in design flexibility, enabling their use in many different industrial control and instrumentation applications.
- Multiple resistance, tolerance, size, and shape options are also available in thin-film RTDs.
Disadvantages of Thin wire type of RTDs
- The disadvantage of using a thin wire type of RTD is that the platinum film, ceramic base, and glass layer all will behave differently at different temperatures.
- There is a loss of accuracy at low and high temperatures
Signal Conditioning of Resistance Temperature Detectors
- We need to have a signal conditioning circuitry to use an RTD practically. With the help of this circuitry, the lead wire errors and other calibration errors can be minimized.
- In an RTD, the change in resistance of the temperature sensor (wire) is very small with respect to the temperature. Hence, we need a bridge circuit. We supply a constant electric current to the bridge circuit and measure the resulting voltage drop across the resistor, and then calculate RTD resistance accordingly.
- With the help of RTD’s resistance, the temperature can also be determined. It is done by using a calibration expression.
- The bridge circuit can be of three different configurations. They are:
2-Wire RTD
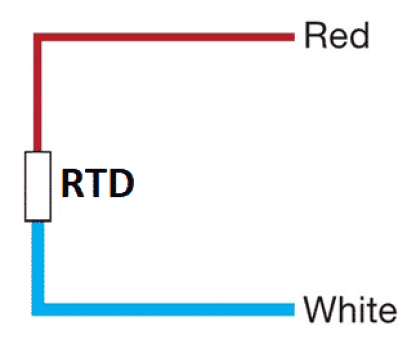
3-Wire RTD
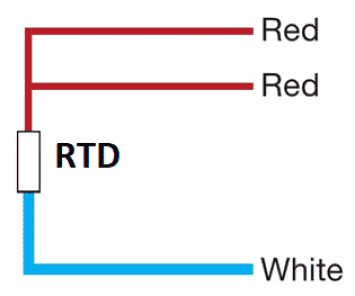
4-Wire RTD
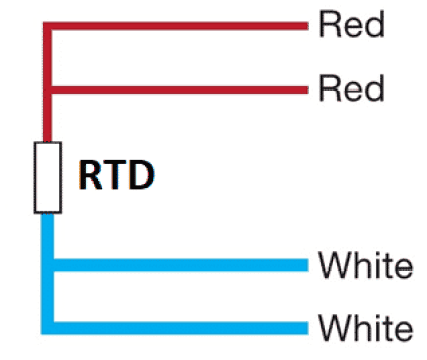
- In the 2-wire RTD, the compensating leg is absent. Output is taken from the two extension leads only. But the resistance of extension leads needs to be considered for an accurate measurement or else the resistance of the extension wires will affect the temperature reading.
- So, the 3-wire RTD is used. In this, the resistance of the extension leads is compensated.
- The more accurate version of the 3-wire RTD is the 4-wire RTD. In 4-wire RTD the compensation of the extension wire resistance is better. Hence there is no effect of the extension wire resistance on the temperature measurement.