Wire Insulation is one of the most important aspects of electrical wires, machines, and systems. Insulation is made from non-conducting or insulating material, which ensures the necessary separation between two conductors. This way, the insulation protects against potential short-circuit faults and safely handles the electrical systems without getting electric shocks.
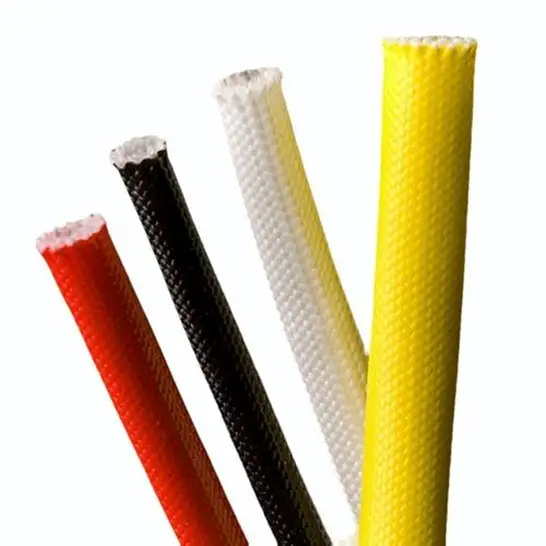
Insulating materials have tightly bound electrons, which generally can’t participate in electrical conduction. They need a very high potential difference applied across them (in thousands of volts) to start some conduction. This voltage is known as the breakdown voltage. That’s why these materials are used as insulators to protect wires and other electrical systems that operate at a voltage much below the breakdown voltage. Let’s understand the insulation of a wire, its application, and its types in detail.
Table of contents
Selection of Wire insulation
Although the work of all types of insulation is more or less the same, the type of insulation to be used varies from one application to the other. There are various factors based on which proper insulation is selected because the insulation has to not only protect the conductor within it but also have to be resilient against its environment.
System Voltage:
We discussed earlier that the safe voltage limit for an insulating material to work appropriately is its breakdown voltage. Therefore, a high-voltage wire needs a higher-order insulation as compared to that for a low-voltage wire. This ensures the safety of the system. At the same time, if a higher-order insulation is used for a relatively low-voltage system, it will be useless and uneconomical. Therefore, proper analysis of the power requirement is necessary for proper insulation.
Ambient Temperature:
Temperature affects the quality and working of the insulators. The insulating capacity decreases with the increase in temperature. The resistivity of the insulation goes down with rising temperature as insulators have a negative temperature coefficient. The insulation used in wires for the compressor in a refrigerant has to withstand the cool temperature to work correctly. This will undoubtedly be different from the insulation used for wires in a hot application like gasoline pumps, where wires have to face not only high temperatures but also gasoline vapors, liquids, chemicals, etc.
Moisture Resistant:
Insulating material must be able to resist moisture. A wire used inside an enclosed space like a room or a box isn’t exposed to ambient moisture. But for a conductor in an open environment, moisture is an essential factor to look for. Therefore, the type of insulation for wires used for both will differ.
Fire Resistant:
Good insulation exhibits low thermal conductivity. It means the insulating material should be able to absorb the heat generated and show little to no temperature difference. However, there are specific applications where the system temperature may rise dramatically. The wire insulation in such a system should withstand this varying temperature and be fire-resistant. Improper selection of insulation may result in the creation of hotspots and may lead to fire incidents.
Durability:
There are various heavy-duty dynamic applications where wiring is done. These are prone to continuous movement and shock. The wiring insulation should be durable enough to withstand such movements and shocks. On the other hand, durability is necessary for the material’s longevity, which may be prone to wear and tear otherwise.
Cost:
One of the most important things to consider while selecting proper insulation is the cost. The wire insulation should be optimum to withstand all the mentioned factors but should also be available at a reasonable cost.
These are some of the fundamental factors among many to be considered before selecting proper insulation.
Wire Insulation Types: Materials used for insulation
Plastic:
Plastic is a useful and commonly available type of insulating material. It is known for its high-voltage insulation, ductility, low thermal conductivity, etc.
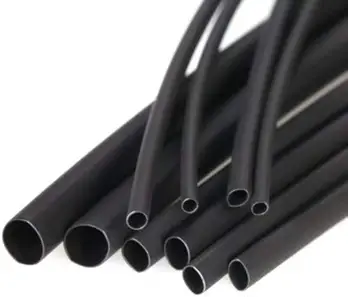
Some of the commonly used plastics in insulating materials of a wire are:
Plastic material | Description |
One of the most commonly used and cost-effective insulating materials. It is highly durable and can withstand temperatures ranging from -55 deg. C to 105 deg. C. | Denser and more rigid than PVC. It is durable and resistant to fire and chemicals. It can withstand temperatures from -65 degrees C to 80 degrees C. |
Polyethylene (PE) | Highly cost-effective and resistant to oil, heat, and temperature. |
Polypropylene (PP) | It has higher thermal resistance than PE. It can withstand temperatures from 30 deg. C to 80 deg. C. |
Polyurethane (PUR) | Denser and more rigid than PVC. It is durable and resistant to fire and chemicals. The wire insulation of this material can withstand temperatures from -65 degrees C to 80 degrees C. C. |
Chlorinated Polyethylene (CPE) | They are typically used as a secondary insulator over softer insulation materials. Nylon provides a flexible protective layer with poor water resistance. |
Nylon | Has a high thermal and moisture resistance. They are used to insulate high-voltage cables, underground cables, and submersible cables. |
Cross-Linked Polyethylene (XLPE) | Has a high thermal and moisture resistance. They are used to insulate high-voltage cables, underground cables, and submersible cables. |
Rubber:
Rubber is another material used for insulating materials. It is more flexible and resilient than plastic. Some of the commonly used rubbers for insulating material of a wire are:
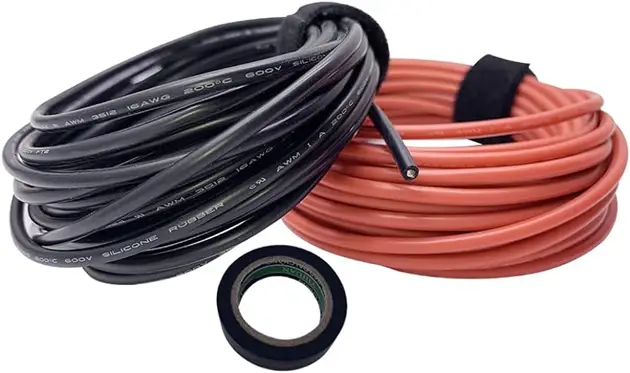
Rubber materials | Description |
Thermoplastic Rubber (TPR) | It is one of the most commonly used rubber-insulating materials. It is resistant to a broad range of temperatures, UV radiation, and wear and tear. |
Styrene Butadiene Rubber (SBR) | They are known for their high-temperature resistance. It is typically used for MIL cables. It can operate at temperatures between -55 degrees C and 85 degrees C. |
Silicone | They are used for low-voltage applications. It has good chemical and heat-resistant properties. |
Ethylene Propylene Rubber (EPR) | It is highly resistant to heat, moisture, oxidation, acids, and alkalis. They are used in medium voltage applications, mining applications, and welding applications due to high abrasion resistance. |
Fiberglass | Used for very high-temperature applications as it can withstand temperatures up to 500 deg C. It is highly resistant to heat and moisture. Wires with fiberglass insulation are used in heaters and motors. |
Chlorosulfonated Polyethylene (CSPE) | They are used for low-voltage applications. It has good chemical and heat-resistant properties. |
Ethylene Propylene Diene Monomer (EPDM) | It is known for its flexibility and thermal resistance. It can withstand temperatures between -45 deg C and 177 deg C. |
Neoprene (polychloroprene) | It is known for its incredible abrasion and cut resistance. Also resistant to oils and chemicals. |
Fluoropolymer:
Fluoropolymers are known for resisting acids, bases, and solvents. Some of the commonly used fluoropolymers in electrical insulations are:
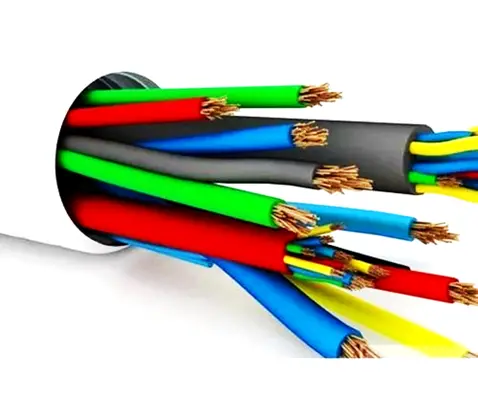
Fluoropolymer materials | Description |
Perfluoroalkoxy (PFA) | Provides excellent resistance to heat, moisture, oils, and chemicals. It is also known for its flexibility and can operate at a temperature between -70 deg C to 200 deg C. |
Polytetrafluoroethylene (PTFE) | Known for its excellent resistance to corrosion and high melting temperature. It also provides resistance to chemicals, electrical currents, and radiation. |
Ethylene tetrafluoroethylene (ETFE) | Known for its excellent resistance to corrosion and high melting temperature. It also provides resistance to chemicals, electrical currents, and radiation. |
Polyvinylidene Fluoride (PVDF) | It is an economical insulation material. It has flexibility, lighter weight, and flame resistance to UL 910 standards for plenum cables. |
Fluorinated Ethylene Propylene (FEP) | It has highly effective insulation properties and resistance to UV and chemicals. It is extremely tough and flexible. |
Specifications of a wire insulation
Specifications are the answers to the set of questions that we have before we purchase materials. In the case of the wire insulations, we must focus on the following key specifications:
- Approving body: These bodies approve insulating materials based on specific standard codes. Some of these bodies are UL, CSA, CE, SAE, ISO, etc.
- Voltage: System voltage must be noted before going for its insulation. Check the range for which the insulation would work without failing and ensure that the system voltage falls within that range.
- Temperature: The insulation should withstand the system and the surrounding temperature.
- Proper material required: Insulations are available of various materials, as we discussed. Whether plastic insulation or rubber insulation will be sufficient, one should judge based on the application and check for the same in the specifications.
- Durability: Insulation should be based on the type of application and the environment around it, which can ensure its durability and longevity. Therefore, proper and required materials having high cost-efficiency should be selected.
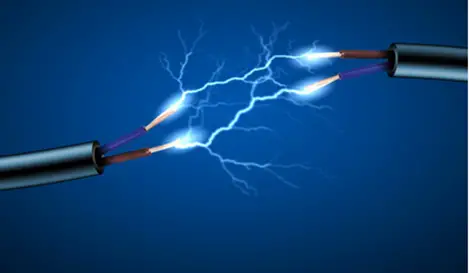
This is all about wire insulation, its application, and its types.