Viscometer measures the viscosity of a fluid. Viscosity measurement can be important for all liquid to semi-solid materials that we know from daily life. A viscometer is used primarily to measure fluid viscosity and other flow-related characteristics.
The viscosity of a fluid is measured by the friction force that occurs between the “layers” that make it up. Viscosity is simply the internal resistance of fluids to flow. A centipoise (cP) is a unit of dynamic viscosity.
Let us understand the few lines regarding the basics of viscosity before discussing Viscometers.
Definition of Viscosity
Viscosity is a type of mass property defined as the resistance of a liquid to flow. When intermolecular attractive forces are strong within a liquid, there is a higher viscosity. Mathematically, viscosity can be defined as the ratio between the shear stress and the velocity gradient of the fluid.
Purpose of Viscosity Measurement
Monitoring the physical characteristics of fluids is critical in industrial sectors that manufacture liquid products or use them in their production processes. Precise measurements of the viscosity of a liquid can guarantee the control of processes in the industry. Viscosity measurement is an indicator of the quality of the final product.
Monitoring of this property is essential, as it affects the performance of the fluid, for example, during its pumping from one place to another.
Importance of Viscosity Measurement in Lubricants
For example, let us take LUBRICANTS. They have extensive applications – the quality control of these is rigorous. Hence, viscosity requirements are strictly followed.
If the viscosity of a lubricant is too high, a fluidity problem will occur in the product. This causes increased friction, thereby heat gets generated, accelerating the oxidation process, and lessening the useful life of the lubricant. Thereby increase in energy consumption. Finally, high viscosity lubricant increases wear of the equipment, with the consequent increase in repairs and shortening of the useful life of the components.
On the other hand, if the viscosity of a lubricant is too low, the fluid will not adequately cover and protect the parts, with consequent component wear. Thereby increase in repairs or component replacements. Increased friction, and heat, help faster oxidation, and high formation of sludge, which finally leads to greater energy consumption.
Types of Viscometers
In the industrial sector, viscosity is very crucial. It is measured and controlled using viscometers. This parameter can be measured using several different models, each of which is appropriate for the specific conditions of the manufacturing process.
To find the model of laboratory equipment that best suits a given application, some factors must be considered first. First, the viscosity range of a sample must be reviewed (low, medium, or high).
The following are the most widely used.
- Rotational Viscometer
- Capillary tube Viscometer
- Falling ball Viscometer
Rotational Viscometers
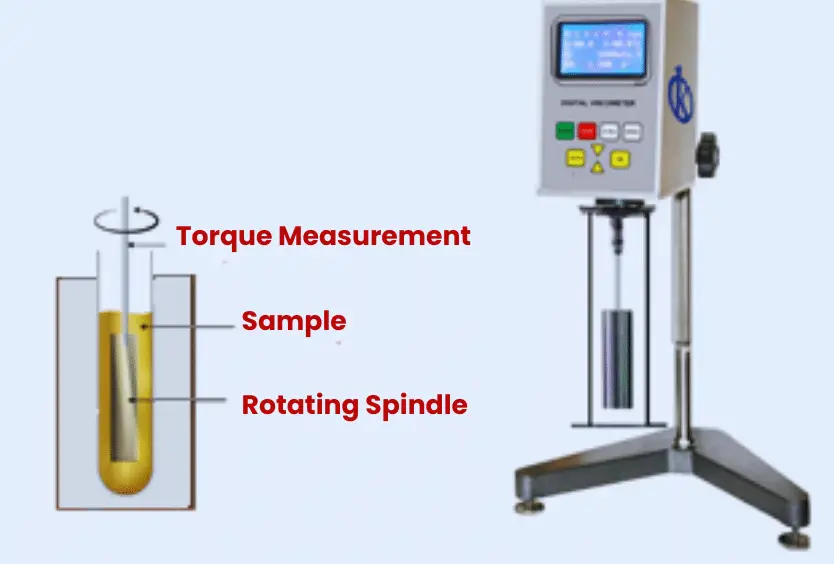
This type of viscometer is the most suitable for evaluating Non-Newtonian fluids.
The rotational viscometer comprises a spindle, rotated by a motor while immersed in the sample fluid, whose viscosity is to be determined. The spindle is rotated at a constant speed. It measures viscosity by analyzing the torque requirement to rotate a spindle. The torque demand is proportional to the viscous drag on the spindle, therefore, the sample viscosity.
Many liquids are exposed to thermal loads and therefore change their viscosity, for example, motor oils. This is exactly where the rotational viscometer comes into play. It is equipped with a probe to measure the temperature of the sample to be able to control it at all times. The immersion temperature sensor determines the temperature of the sample in a range between 0 to 100 °C during the measurement.
Viscometer accuracy depends not only on the design of the equipment but also on the accuracy of the temperature control. An accurate result is often obtained by averaging several repeated viscosity measurements.
To obtain the measurement history, the viscometer can be connected to a PC through the RS-232 interface.
Capillary Viscometer
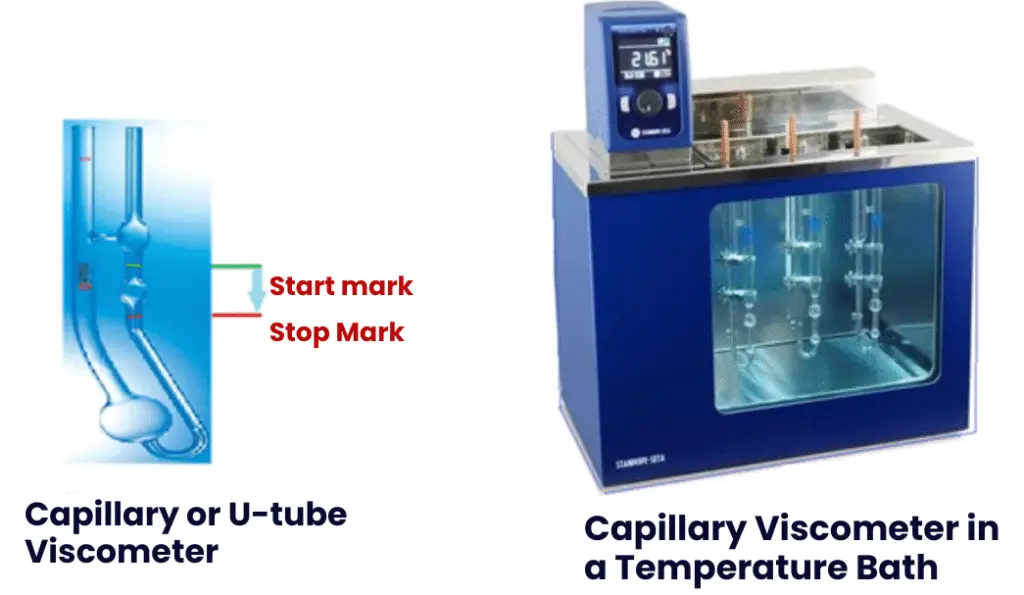
The primary apparatus used in a capillary viscometer test is a glass tube, used to measure non-Newtonian liquids. It is typically “U” shaped, giving it its commonly associated name, the U-tube. A temperature-controlled bath usually 40 or 100° C is required for this procedure.
Its simple design consists of a U-shaped glass tube with two bulbs (one on top, one at the bottom). The fluid passes from the upper bulb to the lower bulb through a capillary. Now, the viscosity is measured by measuring the time taken by the fluid to pass through the tube either by suction or by gravity force.
This measured time is then multiplied by a constant value associated with the particular tube to calculate the absolute (suction) or kinematic (force of gravity) viscosity.
U-tube viscometer comes in several variations. The most well-known three types are Ostwald, Cannon-Fenske, and Ubbelhode.
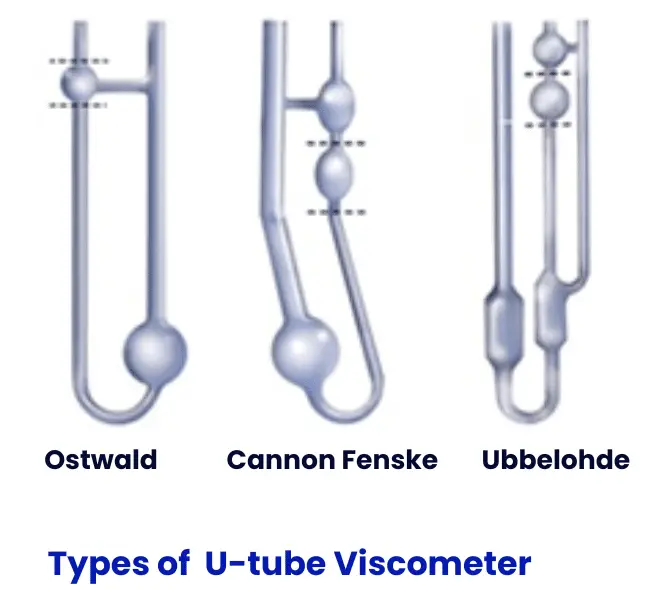
Falling ball Viscometer
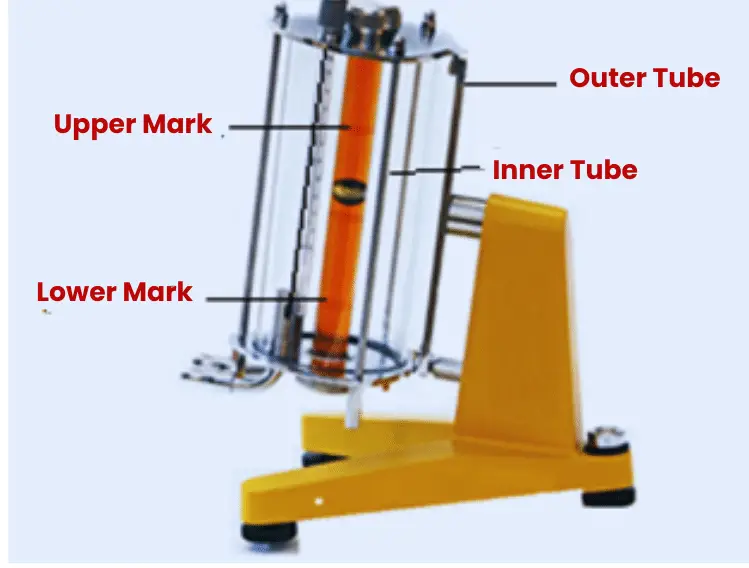
A falling ball viscometer uses Hoppler’s principle to measure the viscosity of fluids. By measuring the time required for the fall of the ball by gravity through the fill tube with the sample.
A falling ball viscometer is designed to measure the viscosity of Newtonian liquids and gases. That is, mainly low-viscosity substances.
The device consists of two glass tubes, one is a thick-wall glass tube inserted into another glass tube. Water is circulated in this space, a temperature probe is inserted in it. The whole arrangement is slightly tilted at an angle (50°, 60°, 70°, or 80°) on a stand. The tube is rotated at 180° around an axis perpendicular to both tubes.
The inner tube is filled with a liquid whose viscosity is to be determined. The spherical ball made of glass or solid supplied by the manufacturer is dropped through it. The speed of fall depends on the greater or lesser coefficient of viscosity of the sample to be measured.
The average time of three tests can be used to measure viscosity.
Advantages of Viscometer
- Viscometers are very helpful for quality control of the final product.
- In the production process, Viscometer is a part and parcel of quality control.
- The viscosity of solutions, suspensions, emulsions, and melts can be determined during formulation, transport, storage, and handling.
- By using viscometers in process control, industrial operations can be carried out efficiently. One can expect product quality, and with the least amount of variation possible.
- A viscometer in process control is to identify and correct variations in liquid specifications.
Applications of Viscometer
- In the industrial sector, the viscometer has a broad range of applications and is an important instrument for the verification of quality products.
- In glass manufacturing, viscosity control is carried out throughout the manufacturing process, since this parameter has a significant effect on other physical properties, such as melting, softening, and crystallization.
- The calculation of viscosity oil refining is important because it is a key element in determining the amount of liquid that can be transported in a pipeline during a specific period. Fluid properties can be dramatically affected by small changes in viscosity.
- Printing inks – water-based lacquers, inks, printing inks.
- Paper industry – Pigment dispersion, Paper additives, emulsions.
- Food industry – honey, milk, jelly sugar solution, beer, fruit juice.
- Chemical industry – Solvents, resin solutions, adhesives solutions, polymer solutions.
- The use of the viscometer to verify the quality of the final product of cosmetics, biotechnological products, paints, and adhesives.
- Detergents – washing liquids, liquid washing agents, and surfactant solutions.