Integral Flow Orifice Assembly facilitates the mounting of differential transmitter on the orifice plate assembly. As a result, this makes the system very simple and eliminates the installation cost of piping up to orifice assembly.
Integral Flow Orifice Assembly
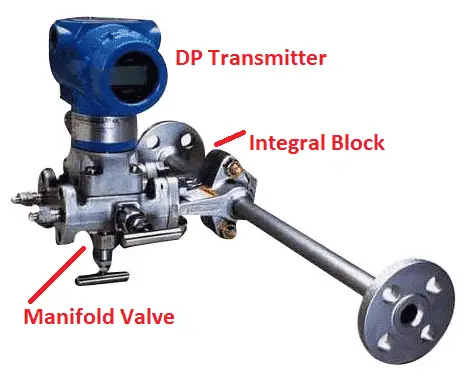
As shown in the above pic, the differential transmitter has its direct mounting on the orifice assembly through a 3/5 Valve H-type manifold.
The assembly is suitable for working up to 120 degrees Centigrade. The higher temperature above 120 degrees Centigrade may cause malfunction of the electronic circuitry of the differential transmitter.
The integral flow assembly has an orifice plate between two integral blocks that have corner taps. Both ends of the pipe are welded to the blocks with end flanges.
Advantages of Integral Flow Orifice Assembly
The use of an integral orifice assembly or meter run assembly has the following advantages.
- It eliminates the measurement inaccuracies on account of small orifice installation.
- The honed body of integral assembly reduces ID uncertainty.
- The precision bored upstream and downstream sections of the pipe of the integral assembly reduce the velocity profile distortion.
- Integral Orifice Plate design eliminates the possibility of plate misalignment.
- The integral orifice flow meter does not require impulse lines, thus it reduces the leakage.
- It facilitates the flexibility of numerous process connection options.
- The direct mount design does not require a long impulse line. Therefore, It minimizes line plugging problems.
- The direct mounting of the differential transmitter on the manifold head is possible.
- It is suitable for liquid, gas, and steam.
- It has good measurement accuracy. Accuracy up to ±0. 5% of volumetric flow rate
- This fully integrated flow meter assembly does not require fittings, tubing, valves, adapters, and mounting brackets. As a result, it reduces the welding and installation time.
Parts of Integral Flow Orifice Assembly:
The followings are the parts of integral flow orifice assembly.
- Flange union
A pair of flanges are screwed to the ends of pipes of the integral assembly. It is welded at both ends of the pipe. The flange unions connect the assembly to the process pipe. - Manifold
The manifold assemblies offer a centralized location for connecting multiple valves within a system. - Run Pipe
Generally, a meter run pipe is recommended for integral orifice assembly. The pipe length towards the upstream is 750mm and the downstream length of 250mm. - Differential transmitter
A differential pressure transmitter creates a consistent and accurate pressure drop in a pipe. Then, the transmitter shows the flow rate of liquid according to the pressure drop. - End flanges
The assembly has flanges that connect the assembly pipe with a process pipe. Typically flanges are welded or threaded. The two flanges are connected together by bolting them with a gasket to provide a seal that provides easy access to the piping system.