The current in a healthy electrical network remains within a fixed limit. However, if it exceeds this limit, a fault occurs. This fault can be a phase-to-ground or phase-to-phase short circuit. As a result, excess current generates heat, which can permanently damage connected equipment. To prevent this, an electrical fuse is used. A fuse is a protective device containing a conductor. Specifically, when the current exceeds the set limit, the conductor melts and breaks the circuit. Therefore, this makes the fuse the weakest point in the circuit. This article explains the HRC fuse, its working principle, construction, and applications.
What is HRC Fuse?
Definition: An HRC fuse (High Rupturing Capacity fuse) is a type of fuse designed to carry a short-circuit current for a specific time. If a fault occurs in the circuit, the fuse blows off to break the connection. It is made of glass or other chemical compounds.
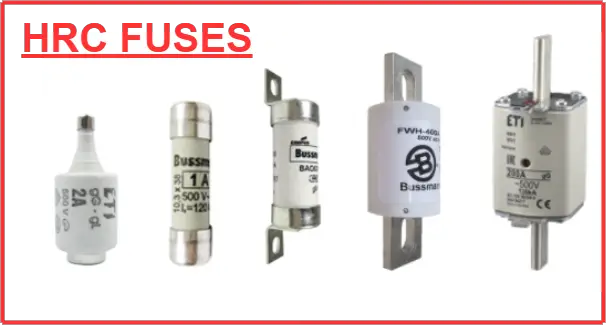
The fuse enclosure is tightly sealed to prevent air from entering. On both sides of the fuse, a ceramic enclosure is attached. Additionally, a metal cap is welded to the fusible silver wire. A small gap around the wire or fuse element is kept inside the enclosure. This space allows the fuse to function effectively by controlling heat dissipation and arc formation.
An HRC fuse is reliable and it has a special feature. If the fault current is high, the fuse breaks quickly. On the other hand, if the fault current is low, the fuse takes a long time to break.
Working Principle of HRC Fuse
Under normal conditions, the current flowing through the fuse is not strong enough to blow its element. However, if a large current flows, it melts the fuse element before the fault current reaches its peak value.
When the fuse is in an overload condition, its element does not blow off immediately. However, if the overload continues for a long time, materials like eutectic will melt and break the fuse element.- A eutectic is a uniform mixture of two or more substances. It melts at a lower temperature than any of its components. In a short-circuit condition, the thin parts of the fuse element melt quickly and break before the eutectic material.
This is why limitations are set within the element of an HRC fuse. This is why specific design limits are set within the HRC fuse element. These limits ensure that the fuse responds correctly to overload and short-circuit conditions, protecting the circuit effectively.
Construction of HRC fuse
The HRC fuse is made of a strong, heat-resistant material like ceramic. This ceramic body has metal end caps. These caps are welded to an element that carries a silver current. Inside the fuse body, there is a filling powder. The materials used for this powder include quartz, plaster of Paris, dust, marble, and chalk. Because of this filling, the current flow does not cause overheating. The following diagram illustrates the construction of an HRC fuse.
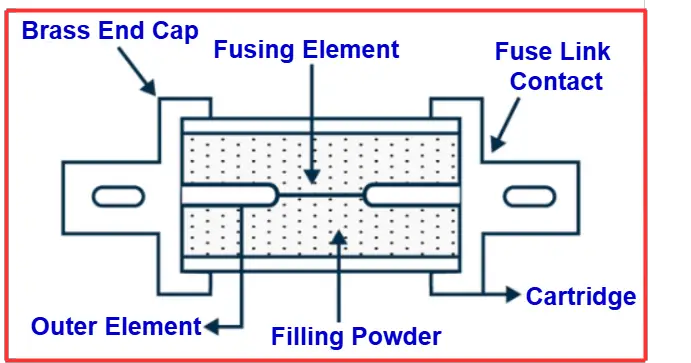
When the fuse element melts due to high current, the heat turns it into vapor. Then, a chemical reaction happens between the filling powder and the silver vapor. This reaction creates a high-resistance material that helps reduce the arc inside the fuse.
Copper or silver is commonly used as the fuse element. This is because both metals have low specific resistance. The fuse element usually has two or more sections. These sections are connected by tin joints. Tin has a melting point of 240°C, which is lower than silver’s melting point of 980°C. Because of this, the tin joints melt first during a short circuit or overload condition. This prevents the fuse from reaching extremely high temperatures.
Types of HRC Fuse
There are three types of HRC fuse.
- NH Type Fuse
- Din Type Fuse
- Blade Type
NH Type Fuse
These fuses provide protection against short circuits and overloads for low and medium-voltage applications. It is used to protect motor starters and other devices from electrical faults. These fuses are lightweight and have a compact, sturdy design.
Din Type Fuse
These fuses are available in a wide range of rated currents. They are used in various fields for different purposes. This is because they perform well at different temperature conditions. They can handle different voltage levels and are mainly used to protect transformers. One of their key features is their excellent clearing capacity. This makes them highly effective in handling short circuits. These fuses are commonly used in air and mining applications. They are also found in feeder sectionalizing, gas-insulated switchgear, and transformers.
Blade Type Fuse
This type of fuse is also known as a plug-in or spade fuse. It has a plastic body with two metal caps, which fit into a socket. These fuses are mainly used in cars to protect against short circuits and wiring issues. They are also used in motors for backup protection. They are lightweight and have a low cutoff current. Blade-type fuses come in different sizes and shapes. They are also available with various current ratings to suit different applications.
Characteristics of HRC Fuse
A fuse works when its element melts due to the heat generated by I²RF. Here, RF represents the resistance of the fuse. If the current flowing through the fuse increases, the heat generated also increases. As a result, the fuse element melts faster when there is a high fault current. However, for a lower fault current, it takes more time to melt. This relationship between time and current is called fuse characteristics. Understanding these characteristics is important for selecting the right fuse for a specific circuit.
Characteristics of HRC Fuse
HRC (High Rupturing Capacity) fuses have the following important features that make them reliable for electrical protection.
- High Voltage Ratings – They can operate at voltages ranging from 220V to over 40kV, depending on the application. International ratings cover both utilization voltage and maximum system voltage.
- Wide Current Ratings – They are available in different current ratings, from less than 1 amp to several hundred amps, based on the equipment’s full load current (FLA) or overcurrent protection device (OCPD) size.
- High Breaking Capacity – These fuses are designed to handle fault currents of 1500A or higher, ensuring safe circuit disconnection and proper coordination with downstream protective devices.
- Fast Interrupting Time – HRC fuses can operate in less than a second for semiconductor protection, while for applications like motor starters, they may take a few seconds to allow short-duration overloads without unnecessary tripping.
- Current Limiting Feature – They reduce the magnitude of fault current, preventing excessive damage to connected components.
- Reliable Arc Quenching – The fuse contains arc-extinguishing materials that break the circuit safely without causing a dangerous arc or fire.
- Long Service Life – They are built with durable materials that provide consistent performance over time with minimal degradation.
Why are HRC Fuses Used for Power Electronics Device Protection?
Power electronic devices like SCRs, IGBTs, MOSFETs, and diodes are sensitive to high currents. An HRC (High Rupturing Capacity) fuse protects them from damage caused by short circuits and overcurrent conditions. These fuses respond quickly and disconnect the faulty circuit before the current reaches high levels.
HRC fuses have a high breaking capacity, so they can safely interrupt large fault currents without explosion or fire hazards. They also have a current-limiting action, reducing the impact of fault currents and protecting delicate semiconductor components. Since power electronics devices cannot withstand high energy surges, HRC fuses are designed with a low I²t value, allowing only a small amount of energy to pass before disconnecting the circuit.
These fuses also protect against transients and voltage spikes, which are common in power electronics applications. If one component fails, it can cause a chain reaction that damages other components. An HRC fuse isolates the faulty circuit and prevents system-wide failure.
Advantages of HRC Fuses
The benefits of these fuses include the following:
- They are cheaper than other types of fuses.
- Their design is simple and easy to understand.
- They require no maintenance.
- They have a high breaking capacity, making them reliable for fault protection.
- Their performance is consistent over time.
- They are easy to operate.
- Their inverse time characteristic makes them ideal for overload protection.
Disadvantages of HRC Fuses
The drawbacks of these fuses include the following:
- They cannot be reused once they blow out.
- They may cause overheating in nearby electrical contacts.
- There is a higher risk of interlocking issues.
- They need to be replaced after every operation.
- The heat produced by the arc can affect the connected switches.
Applications of HRC Fuse
HRC fuses are used in various electrical and industrial applications, including:
- Short-Circuit Protection – They protect circuits in high-voltage (HV) switchgear from short circuits.
- Backup Safety – They serve as backup protection in electrical systems.
- Device Protection – They safeguard electrical devices such as motors, transformers, and automobiles.
- Motor Stators – These fuses are used in the stators of motors to prevent damage from electrical faults.
- Power Electronics Device Protection – They protect sensitive power electronic components like SCRs, IGBTs, and MOSFETs from overcurrent and short circuits.
Conclusion
In summary, this article provides an overview of HRC fuses and their features. From the above information, we can conclude that the current carrying capacity of a fuse wire depends on several factors. These include the material, dimensions, length, diameter, shape, and size of the fuse element.