Electric poles are the different poles and towers used as support structures for overhead transmission lines. They are designed to ensure safe and efficient electrical power over long distances. The following are the key characteristics of electric poles.
- High Mechanical Strength: They are designed to support the weight of conductors and sustain additional stresses such as wind and environmental forces.
- Lightweight and Durable: While maintaining strength, electric poles are designed to withstand significant mechanical stress over time.
- Cost-Effective: They offer a balance between initial investment and ongoing maintenance expenses.
- Long Lifespan: Electric poles are built for longevity to ensure extended service life.
- Easy Access: They allow for easy inspection and repair of conductors.
Electric pole types used based on specific needs for overhead line support are wooden, concrete, steel, and rail poles.
The choice of pole material depends on several factors such as the load’s importance, the terrain and location, construction costs (including maintenance), and the overall project profitability. A single pole may support all phases, including the earth, and the neutral for low-voltage transmission lines. Different types of poles are used for the electrical system to support the various overhead line components.
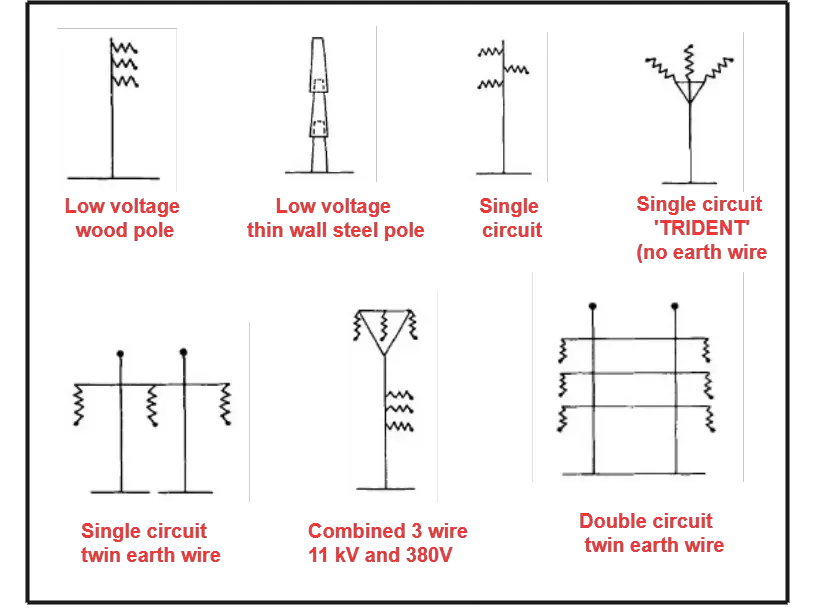
Types of Electric Pole
There are four main types of electric poles.
1). Wooden Electric Pole
2). Concrete Electric Pole
3). Steel Tubular Electric Pole
4). Rail Electric Pole
Wooden Electric Pole
Wooden poles are generally used to support low-tension lines (400 volts and 230 volts) and high-tension lines (11 kilovolts). In some cases, they are also used for 33 KV lines in certain situations. Wooden poles are much cheaper than other types of electric poles, and their foundation costs are also relatively low. A wooden pole has a longer life with proper maintenance and treatment.
Wooden poles are classified into three categories based on their strength in supporting electric cables:
Low-Strength Wood: These poles can withstand a force between 450 and 630 kg/cm². Examples include Chir, Debdaru, and Arjun wood.
High-Strength Wood: These poles can withstand a force of more than 850 kg/cm². Examples include Shaal and Masua wood.
Medium-Strength Wood: These poles can withstand a force between 630 and 850 kg/cm². Examples include Teak (Tik), Seishun, and Garjan wood.
The wood used for electric poles should be of high quality. Straight wood is preferred for this purpose. In special cases, two shorter poles can be joined to achieve the required length.
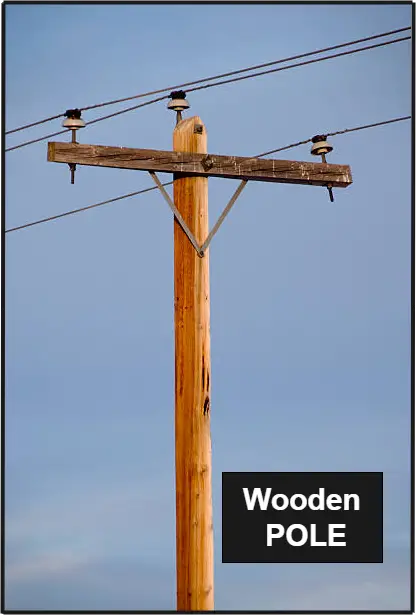
Wooden Pole Treatment
The first step in protecting wood is curing, which means drying it completely. Dry wood is important because it prevents damage from fungi and termites, with termites being the most harmful.
Heat and moisture can also damage wood, especially near and below ground areas. The wood is treated with chemicals to protect it. A common method uses a mix of tar with Creojet Oil or Copper Chromate Arsenic.
This process is called the Askew treatment. Wooden poles are placed inside a sealed tank and soaked in a Copper Chromate Arsenic solution. High pressure, up to 100 kilograms per square meter, is applied for at least one hour. This forces the chemical deep into the wood, protecting it from moisture and termites for a long time.
If the wood is not properly treated, the entire pole should be sprayed with two coats of Creojet oil before installation. Bituminous Creojet Oil must be applied to the part of the pole that goes into the ground and up to 50 cm (20 inches) above it. If this is not possible, tar should be used on the surface of the pole. If neither treatment is an option, the bottom two meters of the pole should be burned on the outside. This helps protect it from termites and moisture.
The top of the pole should be shaped into a pointed cone to prevent water buildup. Slots should be cut in the top section to fit the cross arms securely. The drilled holes should have a diameter between 17 mm and 20 mm. D-shaped iron clamp grooves are not required; a simple drilled hole at the required distance is enough. The top hole should be at least 200 mm (8 inches) from the pole tip. All holes and grooves should be made before the treatment process. After treatment, no new holes or grooves should be made. If required, they must be filled properly with creosote oil or bitumen for protection.
Concrete Electric Pole
Types of Concrete Electric Pole
There are two types of concrete poles:
1). P.C.C. Poles
1). P.C.C. Poles
Plain Cement Concrete (PCC) poles are commonly used in 11 kV and 400/230 volt systems. They are also used in 33 kV high-tension (H.T.) lines. PCC poles cost more than wooden poles but are cheaper than steel poles. They last longer and need little maintenance. These poles are stronger than wooden poles but not as strong as steel poles. However, PCC poles have two main disadvantages—they are very heavy and can break easily.

A cement concrete electric pole is made from cement concrete and reinforced with iron bars or rods to make it stronger. For earthing, a 25 mm × 3 mm copper strip is placed inside the pole during concreting, or a hollow space is left to insert the earthing wire. Also, 20 mm diameter holes are made in the pole during concreting to attach different fittings as needed.
The pole’s cross-section is always wider at the bottom than at the top. For PCC poles, the cross-section is rectangular instead of square.
The height of electric poles depends on their type and use. It plays an important role in their load-bearing capacity.
Concrete poles are classified into 11 types based on their height and load-bearing capacity
Pole classification | Height (Mtr) | Footing Deftness Excavation (Mtr) | Maximum Lateral Load (Kg2) |
1 | 16.5 m to 17 m | 2.40 | 3000 Kg2 |
2 | 16.5 m to 17 m | 2.40 | 2300 Kg2 |
3 | 16.5 m to 17 m | 2.40 | 1800 Kg2 |
4 | 16.5 m to 17 m | 2.40 | 1400 Kg2 |
5 | 14.5 m to 16 m | 2.30 | 1100 Kg2 |
6 | 11.5 m to 12 m | 2.00 | 1000 Kg2 |
7 | 11.5 m to 12 m | 2.00 | 800 Kg2 |
8 | 11.5 m to 12 m | 2.00 | 700 Kg2 |
9 | 9.5 m to 11 m | 1.80 | 450 Kg2 |
10 | 8 m to 9 m | 1.50 | 300 Kg2 |
11 | 6 m to 7.5 m | 1.20 | 200 Kg2 |
The depth of footings depends on the soil type and varies from place to place.
2). R.C.C. Poles
In recent years, reinforced concrete poles (R.C.C. poles) have gained popularity for line support. They are mechanically stronger than steel poles and last longer. They can also support larger spans. R.C.C. poles look better, need little maintenance, and effectively insulate the surrounding area.
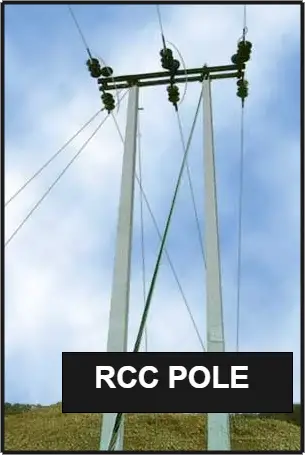
The perforations in the poles make climbing easier and reduce the load on line supports. However, these poles are heavy, making transportation expensive. To solve this problem, they are often built on-site to reduce shipping costs.
Steel Tubular Electric Pole
Steel tubular poles are much stronger and have a higher load-bearing capacity than wooden and concrete poles. With proper maintenance, they last a long time. However, they are expensive, so their use is gradually decreasing. They are mainly used in low and medium-voltage systems (400/230 volts) and 11 kV H.T. lines. In some cases, they are also used for 33 kV systems.
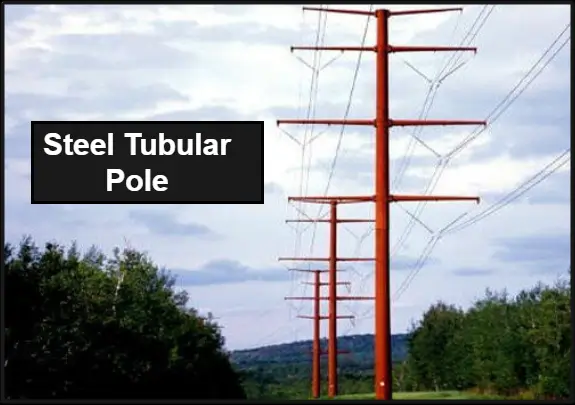
Types of Steel Tubular Electric Pole
Tubular poles are classified into two types:
1). Swaged Pole
2). Stepped Pole
1). Swaged Pole
Swaged tubular poles are made from high-quality materials like MS steel and sheets. The swaging process makes them stronger and more stable than simple linking poles. Because steel is versatile, these poles can be used in many applications, including commercial, residential, and municipal projects. Architects, engineers, and designers use them for various purposes.
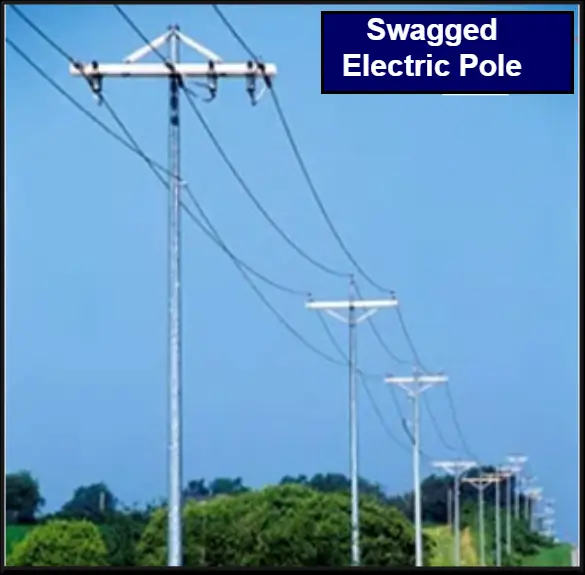
Installation takes less time because the poles are strong, durable, and lightweight. Their maintenance-free design reduces shipping costs.
Swaged poles are made from high-quality tubes, either welded or seamless, cut to the needed length before being swaged and joined. These poles include different types of lighting fixtures, such as single- and double-hanging light poles, traffic light poles, and street light poles.
ERW welded tubes are cut to the required length, then swaged and joined to make swaged poles.
The pole has a safety factor of 2.5, and steel weighs 7.85 grams per square centimeter.
2). Stepped Pole
Stepped poles are made using a special hot-swaged joint technique. In this process, larger-diameter pipes are heated and fused with smaller-diameter pipes, creating strong and durable joints.
The joints are fully sealed, ensuring the pole stays strong along its entire length. Since no welding is needed, the joints remain secure and reliable for the pole’s entire lifespan.
The pole has a safety factor of 2.5. The weight of steel is 7.85 grams per square centimeter.
Rail Electric Pole
Rail poles have high mechanical strength but are also the most expensive. Their heavy weight makes transportation, loading, and unloading more costly.
This pole is not suitable for 400/230-volt lines. Rail poles are used for 11 KV and 33 KV systems. The rail poles are available in four different sizes for overhead lines.
- 30 kg/m
- 37 kg/m
- 45kg/m
- 52 kg/m
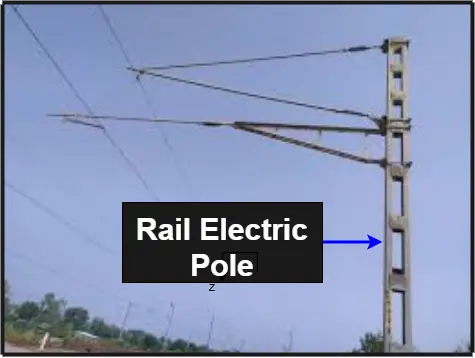
For 11 KV lines, we usually use rail poles that weigh 45 kg per meter. For 33 KV lines, we use both 45 kg per meter and 52 kg per meter rail poles. The length of rail poles ranges from 9 meters to 13 meters. Before installation, we apply at least one coat of red oxide. To make the pole last longer, we coat the bottom part with tar up to a certain height above the ground. Rail poles can hold more weight vertically than they can horizontally.
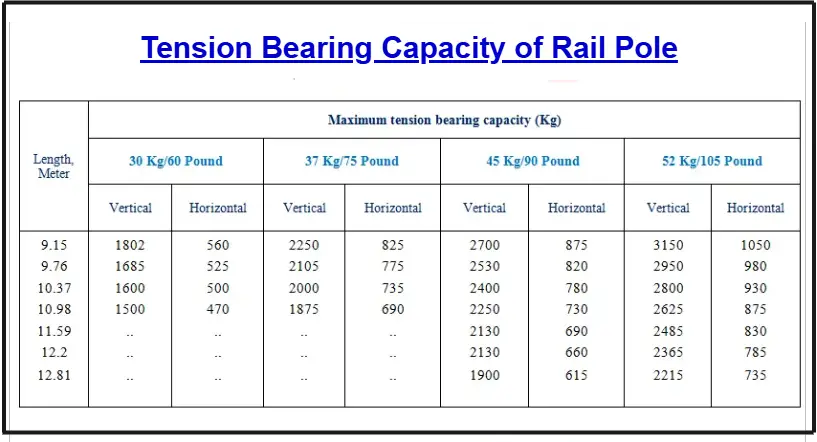