The working of VFD is based on the control of frequency and voltage simultaneously through a PWM inverter. A variable frequency drive (VFD) is most suitable for speed control of an induction motor.
Variable frequency drives are essential tools in many industrial operations. They provide a series of advantages that reduce the time and resources required to carry out operations.
It increases the safety of equipment and technicians, reduces electrical energy cost, and extends the motors’ useful life.
There are other names for it, such as
- Variable Speed Drive
- Adjustable Speed Drive
- Adjustable Frequency Drive
- AC drive
- Microdrive
- Inverter
In this article, we will discuss the working of variable frequency drives, their applications, and their importance in industrial production systems.
What is a Variable Frequency Drive?
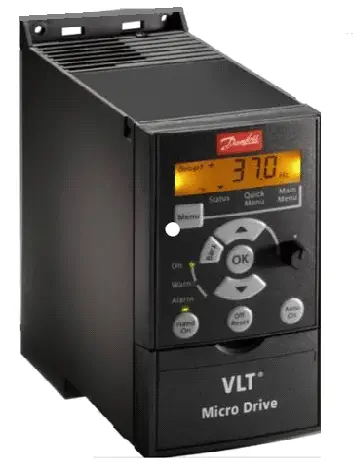
A variable frequency drive (VFD) is a precision electronic device. It is specifically designed and used to control the speed of single-phase and three-phase alternative current (AC) induction motors without affecting the electrical consumption, motor torque, impedance, magnetic flux, etc., of the motor.
Variable frequency drives are motor controllers that vary the frequency and voltage supplied to an electric motor. The drive has integration with an operator interface to receive the required speed control commands.
The VFD also has the ability to control motor acceleration and deceleration during starting or stopping, respectively.
The synchronous speed of the motor is proportional to the frequency.
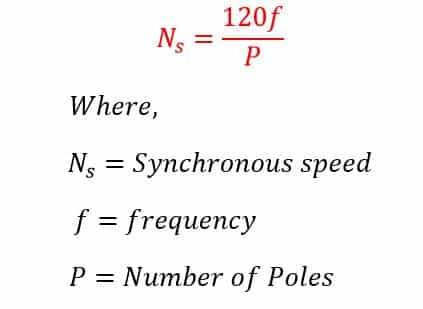
The frequency (or Hertz) of VFD is directly related to motor speed (RPM). In other words, the speed of the motor increases with an increase in frequency. If an application does not require an electric motor to run at full speed, the drive can be used to reduce the frequency and voltage to meet the load requirements of the electric motor.
Working of VFD
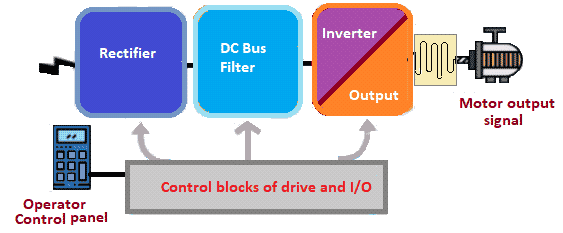
The working of VFD can be well understood by understanding the various sections of VFD. The electronic circuit of a VFD has the following sections.
Input Converter
In this stage, diodes are arranged in a regular bridge rectifier configuration. The AC mains is rectified and converted to DC.
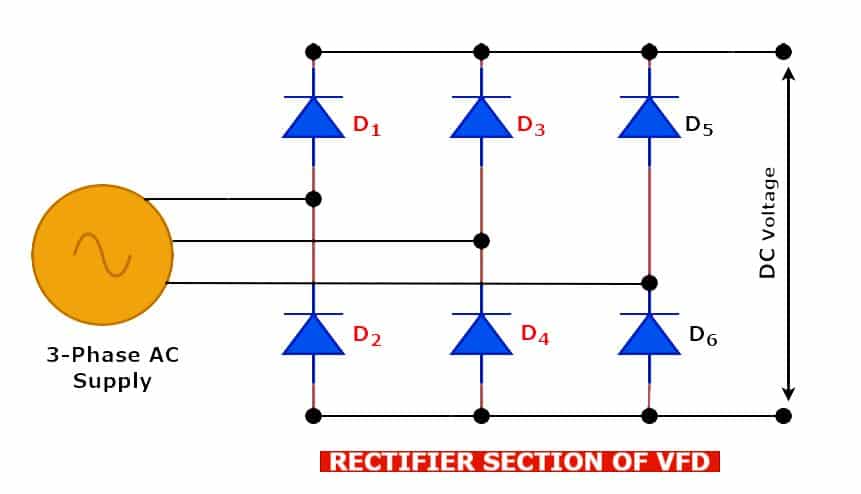
The IGBTs in the rectifier circuit are preferred where regeneration of energy feeds back to the main power supply.
DC Bus filter
The converted AC to DC signal is not exempt from AC components and residual harmonics require filtering. Rectification of AC components is carried out in this stage to reduce the ripples.
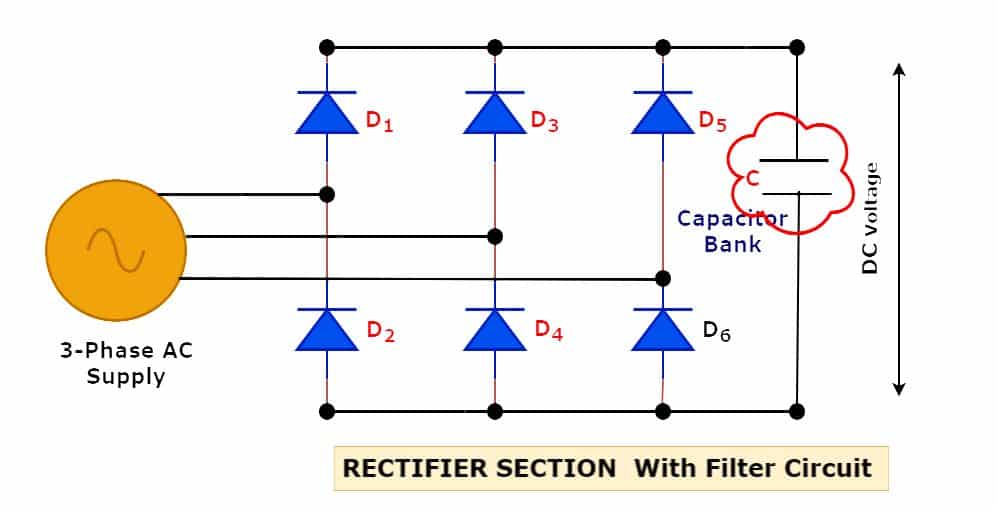
The VFD has a capacitor bank that filters out the ripples in the rectified DC voltage. Thus, we get the smooth DC voltage across the capacitor bank.
Inverter
In this step, the DC from DC bus back to AC but in a special way that forms the heart, or rather brain of the circuit. It consists of sophisticated microcontroller ICs specially designed and programmed to change the output frequency along with the voltage proportionally and also create a 3-phase output from a single-phase input.
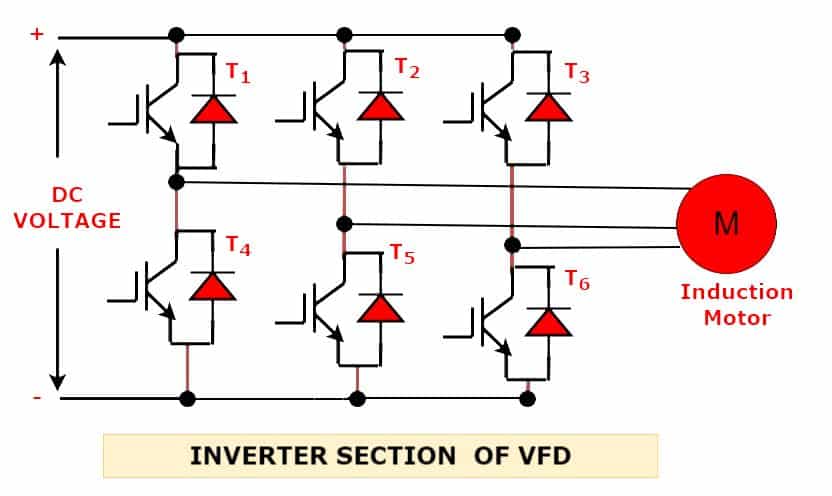
The technique used to vary both voltage and frequency simultaneously is called PWM inverter technology. Thus, the working of VFD is based on the PWM(Pulse width modulation) of the carrier wave with a sinusoidal wave. Thus, in the PWM inverter, the v/f ratio is maintained constant to keep the constant flux in the motor. This stage makes variable frequency drives especially unique and ideal for controlling AC motor speeds
Control section
The command from the previous stage (microcontroller ICs) is sent to the output IGBTs (Insulated Gate Bipolar Transistors) which switch the voltage received from the DC bus in narrow and chopped steps. To do this, the integrated circuits use PWM technology and convert direct current into sine waves.
The output voltage of the PWM inverter depends on the computation time. Greater the commutation time of these waves, the greater the voltage at the output to the motor and vice versa. This PWM procedure is responsible for two important functions of working of VFD.
- Changing the output voltage and frequency without losing the electricity
- Changing its frequency simultaneously with a change in voltage at a given speed to keep the magnetic flux and motor torque constant.
Main characteristics of a frequency drives
Briefly, a variable frequency drive has the following important characters.
- Protection against overcurrent is especially useful in the control of high inertial motors.
- Constant torque ensures a wider speed control range, allowing efficient power control throughout the range.
- It acts as a barrier between all input voltage disturbances like harmonics, ripples, dips, surges, etc., and obstructs them from entering the motor.
Applications of VFDs
VFDs are mostly used for speed control of the fans, pumps and compressors, lifts, and conveyors. These applications, represent 75% of all drives operating globally. Within these most common uses, variable frequency drives (VFDs) serve to:
Reducing energy consumption and costs
In an application that does not need to run the motor at full speed, one can reduce energy constants by controlling the motor with a variable frequency drive. In turn, they allow adjusting the speed of the motorized equipment to the load requirement. There is no other method of controlling AC electric motors that can achieve this.
Electric motor systems are responsible for more than65% of energy consumption in the industry today. Up to 70% of industrial energy consumption can be reduced by installing or upgrading motor control systems.
Additionally, its use enhances the quality of the product and lowers the cost of production. combining energy efficiency tax incentives and utility rebates, the return on investment for drive installations can be as little as 6 months.
Increase production through tighter process control
Shocks during start-up are eliminated on conveyors and belts, allowing for greater efficiency. By running the motors at the most efficient speed for any application, production levels will increase, bringing production costs down.
VFDs for reducing maintenance and extending maintenance
Equipment will last longer and have less downtime due to maintenance when controlled by variable frequency drives, ensuring optimum speed of motor application.
Due to the optimal control of the frequency and voltage of the motor, it will offer better protection in motors from problems such as electrical overloads, phase protection, low voltage, ground faults, single phasing, etc.,
When starting a load with a drive, it will not subject the motor or driven load to the “instantaneous shock”. The VFD starts the motor smoothly, thus eliminating wear on belts, gears, and bearings.
Also, it is an excellent way to reduce and or eliminate the water hammering effect. It is the main cause of breakdowns in pipes and hydraulic installations since we can have smooth acceleration and deceleration cycles.
Advantages of VFD
The frequency inverters are a necessary component in motor control in industrial production systems. It offers the following advantages.
- Saving energy and improving the efficiency of the system. The power-saving potential in the fan and pump application is substantial.
- Adapt drive speed to process requirements. The VFD controls the speed of the motor, and thus it controls the process accurately.
- Adapt the torque or power of a drive to the requirements of the process.
- It is possible to control the motor speed and capture drive running parameters from remote via RS485 or profibus.
- Improve the work environment.
- Low noise levels, for example – from fans and pumps.
- It is possible to create control loops for close loop control of the process variables and the speed of the motor. The VFD has many inbuilt PID control functions.
- Reducing mechanical stress on machines can extend their life.
- Decrease the maximum consumption of the electricity grid to avoid peak demand prices.
- Reduce the size of the motor needed.
- The VFD can operate the induction motor in all four quadrants. Thus VFD can run the motor in braking mode as well. The DC injection braking and dynamic braking are possible in the induction motor through VFD. Thus, the motor can work and the motoring and braking zone. This feature makes the VFD suitable for crane and hoist applications.
- Drives integrate diagnostic and network capabilities to improve performance and productivity.
- The capacitor banks of VFD Improve the power factor of the electrical network.
So, energy savings, intelligent motor control, and peak current reduction are three big reasons to choose a VFD as a controller in every motor-driven system.
Disadvantages of VFD
There are some disadvantages associated with the use of VFDs. These are;
- VFDs have very advanced technology and only a technical expert person can install, program, and maintain the drives.
- The VFDs can cause radio frequency interferences that may link to other nearby installed sophisticated electronic equipment.
- The initial investment is high, however over a period of time the energy-saving through VFD trade-offs the initial cost.
- VFDs can not be repaired at the site, therefore it needs a standby VFD for the immediate starting of the plant. The defective VFD needs to send to the original equipment manufacturer(OEM) for repair or the service engineer need to call the site.
- The VFD generates a higher voltage at the first winding turns of the induction motor and it may one of the reasons for insulation failure. Therefore, an inverter-grade motor needs to be installed with VFD. It incurs extra cost.
- The bearing circulation current phenomenon happens in VFD-driven motors. Therefore, insulated bearing at the NDE side for a motor is a must.
- VFDs pollute the electrical supply system because of harmonics and necessary harmonic filters required with VFD installation.
- The working of VFD gets affected by the voltage dips and surges in the incoming AC power supply.