The soft starter is an advanced electronic starter for induction motors. It is thyristor-based electronic equipment that is used to start and stop the induction motor. In this article, we will discuss the working principle of a soft starter, its advantages, disadvantages, and applications,
It is a piece of electronic equipment based on solid-state semiconductors that allow the start-up of single-phase three-phase squirrel-cage rotor asynchronous motors in a controlled way. Nowadays the soft starter has brought about a significant change when it comes to protecting motors. The block diagram of the soft starter is given below.
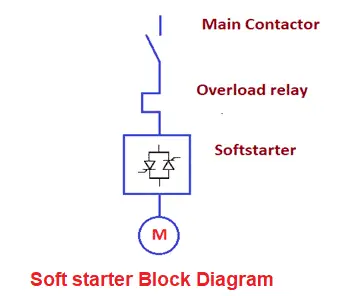
Working Principle of Soft Starter
Induction motors have a fairly high starting current, which can be between 3 and 15 times the nominal current (in normal operation). Although it can be assumed, in the long term it can damage both the motor and the power supply network.
Soft starters control the motor RMS input voltage from zero (or a configurable value) to the nominal operating voltage for starting and vice versa. The starting current drawn by the motor and the torque generated can be controlled by adjusting the supply voltage.
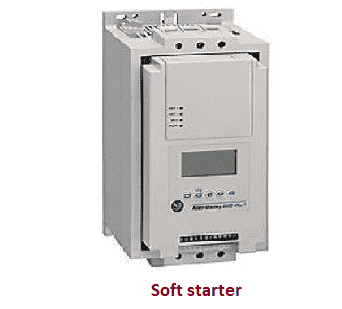
Purpose of Soft starter
Different applications such as pumps, conveyors, and centrifugal machines must be started in a smooth way, and sometimes they must also be shut down in a controlled manner with the idea of preventing mechanical shocks, fatigue, and torsion of shafts or couplings.
The risk of damage that equipment and processes can suffer is very great. Frequent startup of these high inertia applications also generates stress on the motor and power supply.
Construction of Soft Starter
The main parts that make up a soft starter are:
- Control unit.
- Power Circuit.
- Protection devices.
Control unit
It is made up of microprocessors that control the supply current to the motor, using the angular phase control system, with which is achieved by varying the firing angle of the thyristors. The microprocessor supplies the logic sequence for the signals from the starter to the power card and then to the drive cards that are used to drive the thyristors.
If a fault is detected, the starter control logic provides an indication in the LCD (Crystal Liquid Display) and gives the event, and the fault conditions, thus assuring that the starter will have stopped operating to protect the engine.
Power circuit
It is composed of two thyristors connected in anti-parallel per phase, governed by the control module providing total wave control in all three phases. Through this, the current is supplied to the motor.
Protection devices
They act against any fault present both in the motor, the load it activates, and on the starter itself.
This advanced boot system performs the following basic functions:
- Start check.
- Stop check.
- Electronic motor protection.
- Visualization and communication interface.
Working of Soft Starter
Induction motors demand a fairly high starting current, which ranges from 3 to 7 times the nominal current, which in the long term can damage the motor and the power supply network.
In order to control the starting current consumed by the motor and the torque it generates, soft starters control the voltage and deliver it gradually up to the motor’s operating ratings. As a result, the starting current does not generate a peak.
A soft starter wiring diagram is given below.
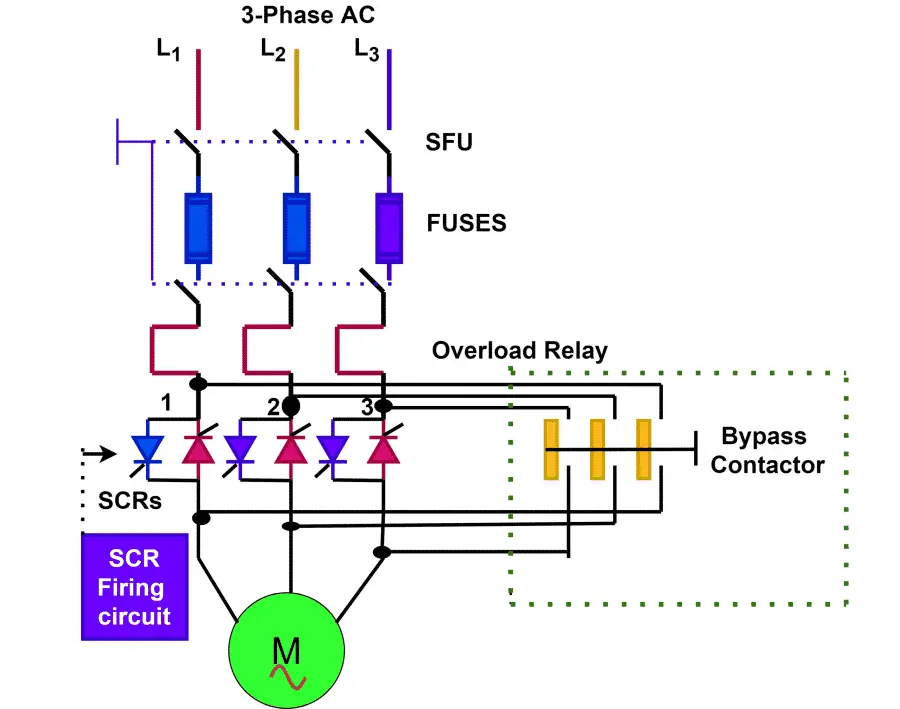
Soft Starter Circuit Description
The soft starter has two SCRs in each phase that are connected in anti-parallel connections. Thus it has 6 SCRs in all three phases. One SCR of each phase conducts in a positive half-cycle and the other SCR of each phase conducts in a negative half-cycle. Thus, these SCRs control the AC voltage in the entire cycle of the AC.
The way to control the voltage supply is through an algorithm where 3 pairs of SCRs are controlled in an anti-parallel configuration that helps us to start or stop the motor.
The output voltage of the soft starter increase with a decrease in firing angle. When the motor starts, the firing angle of the SCRs is zero, and gradually the firing angle decrease with motor acceleration.
The graph between the firing angle and the output voltage is given below.
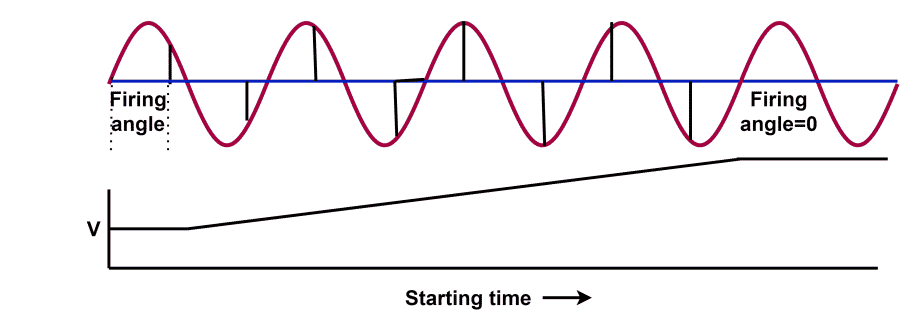
From the above graph, it is clear that with a decrease in firing angle, the ac output of the soft starter increase. When the firing angle becomes zero, the soft starter outputs AC voltage that is equal to the input AC voltage. Thus, the motor gets its rated stator voltage.
When the firing angle is zero, the bypass contactor is made on. For a short period of time, the bypass contactor and the SCRs remain in the circuit, and after some time the firing to SCRs is stopped. In this condition, the motor runs through a bypass contactor.
This arrangement allows us to control the AC voltage by changing the firing angle every half cycle. Thus the voltage is gradually increased until it reaches its full voltage or provides the voltage according to the current limitation.
Advantages of Soft Starter
The following are the advantages of soft starters.
- A simple and flexible way to control the starting current and torque. It starts and stops the motor without any jerks.
- It is suitable for all types of induction motors.
- The uniform control of current and voltage leads free of jumps or transitions in the motor and supply network.
- It is suitable for frequent startups because at every start and stop the motor draws a controlled current and thus, experiences less stress.
- It is suitable for easy change of starting conditions.
- Soft stop control that extends the motor deceleration time. Therefore, the motor comes to stop without jerks. It enhances the useful life of the motor and its driven equipment.
- Braking control that reduces motor deceleration time.
- Unlike DOL and star delta starter, the soft starter driven motor draws a low starting current and thus, it minimizes the stress on the load, motor and line.
- It is much smaller and more compact.
- It reduces the temperature rise of the motor winding during starting. Thus, it enhances the useful life of the insulation.
- The energy-saving is possible if the load demands lower torque than the motor’s rated torque. The energy-saving is achieved by running the motor at the reduced stator voltage.
- The soft starter does not cause voltage dips during starting of current. In the case of DOL or star-delta starting, a large motor current may cause a voltage dip in the power system.
- It is cheaper than the VFD. It is most suitable where there is no need for speed control of the motor during normal operation.
- The soft starter has an advanced micro-controller that controls the firing of SCRs on a real-time basis, therefore the starting and stopping operation of the motor is perfect. Also, it protects the motor from overload, ground fault, and instantaneous overcurrent. In a nutshell, it provides better protection to the motor.
Disadvantages of the soft starter
- Soft starters are not suitable in applications involving speed control. It is only suitable for starting and stopping the motor.
- Soft starters are more expensive in comparison to conventional DOL and star-delta starters.
- Soft starter generates harmonics and pollutes the electrical supply.
- Only a qualified person can troubleshoot the faulty soft starter or an OEM engineer need to call for repairs.
Applications of Soft Starter
The soft starter is most suitable for the following applications.
- Centrifugal pumps
- Compressors.
- Fans / Blowers / Extractors.
- Mixers.
- Crushers / Grinders.
- Presses.
- Cranes
- Conveyor belts, and agitators.