A linear control valve & rotary control valve can be defined as a mechanical device that starts, stop and regulate the passage of liquids or gases. It can be done by linear or rotary movable part that opens, closes, or partially obstructs one or more valves.
Depending on their design and materials, valves can open and close, connect and disconnect, regulate, modulate or isolate a wide variety of liquids and gases. This ranges from the simplest fluids to the most corrosive or toxic.
Linear Control Valves & Rotary Control Valves
Based on the stem movement, control valves can be classified into two types.
- Linear Motion
- Rotary Motion
Linear Control Valves
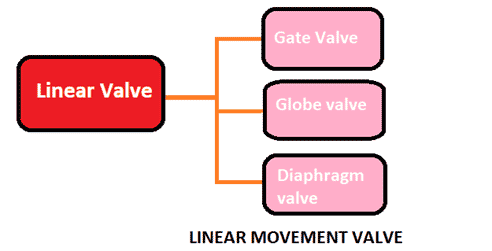
These types of valves have a closing device that moves in a straight line to start, stop or throttle the flow. These valves have a higher level of precision and stability in their closing system, although they may be slower in their operation. We can see them as a gate, globe, and needle valves.
Linear motion valves are used to start and stop the flow. The valve is fully open when the disc is removed from the flow stream.
The closure device could consist of a disc or flexible material such as a diaphragm. Linear motion valves tend to be slower to operate, but have a higher level of accuracy and stability in the position of the closure member.
The closure device can be used to:
- Plug into or against a fluid passage.
- Cylindrical or spherical through a fluid passage
- Move a flexible material in the flow path
The most common examples of linear motion valves include gate valves, globe valves, fixed cone valves, needle valves, and pinch valves.
Gate Valves
Gate valves are used to completely stop or start a fluid. Discs that gradually close with linear movement or vertically until it conforms to the seat open and closes the flow paths. Since they are bidirectional and full bore, they offer a minimum pressure drop.
Gate valves are economical and easily accessible. The disks can be a solid or flexible wedge. Periodically lubrication is required for gate smooth operation. Correction of packing leaks immediately, and operate slowly when opening to avoid hydraulic shock.
Gate valves are classified according to the type of disc they use:
- Flexible wedge
- Solid wedge, and
- Split wedge
Its advantages are high tightness, offers no resistance to flow when open, high capacity, and economical.
Its disadvantages are high torque, slow-closing, and produces cavitation with pressure drop.
Globe Valves
The opening and closing parts of the globe valve are disc-shaped, the sealing surface is flat or conical, and the disc moves linearly along the center line of the fluid. The type of stem operation includes the lifting type (the valve stem is rotated up and down with the hand wheel in place) and the rotating and lifting stem type (the hand wheel and valve rod are rotated). Valve rotates and moves up/down together.
The globe valve is only suitable for fully open and fully closed operation and is not suitable for regulating and throttling. The globe valve is a force-sealed valve, when the valve is closed, pressure must be applied to the disc/plug to establish a tight seal.
The advantages of a globe valve are shorter stroke (compared to a gate valve). Good sealing capacity, less friction between sealing surfaces, and longer service life. Moderate to good throttling ability. There are three patterns available offering unique capabilities: T-type, Y-type, and angle patterns.
Diaphragm Valves
A diaphragm valve s a type of valve that has a flexible diaphragm that opens, closes, or partially obstructs one or more holes or passages.
The flexible diaphragm attached to a compressor works as a shutter, when the valve stem lowers the compressor, the diaphragm produces a seal and cuts off fluid flow.
It is used for total opening or total closing and throttling at low operating pressures. It is used in corrosive fluids, sticky or viscous materials, semi-liquid fibrous pastes, sludge, food, and pharmaceutical products.
Its cost is low. They do not have gaskets. There is no possibility of stem leakage. Immune to clogging, corrosion, or gum formation problems in circulating products.
One disadvantage of diaphragm valves is that diaphragm susceptible to wear. High torque when closing with the pipe full.
Rotary Control Valves
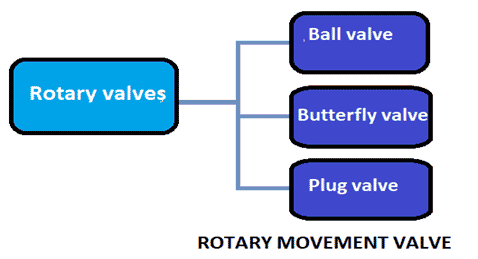
Any valve that takes a circular motion to control flow is a type of rotary valve.
This contrasts with the linear valve, which moves a gate up and down to control flow. The basic function of the rotary valve is the same as a linear valve but generally takes up less space.
These valves rotate a disk or ellipse around an axis. Also known as quarter-turn valves, where the plug and stem are rotated 0° to 90° from fully open to the closed position. When the stem of the Quarter-turn valve is turned 90°, it will move from a fully open or fully closed (0°) state.
They are further classified as ball, butterfly, or spherical valves.
Ball valves
The ball valves are quarter-turn valves. The operating mechanism is made using a drilled ball that rotates between the elastic seats, to start, stop or regulate the circulation of a fluid.
When the valve actuator is in the open position, the ball rotates to a point where the hole through the ball is aligned with the valve inlet and outlet. Ball valves have good tightness and fast opening.
Ball valves are a common type of rotary valve. This is also called a shut-off valve. The ball valve has a hole in the center, which is turned by a handle. Inserted into a pipe, it can be closed, partially open, or fully open, allowing some flow control. Opening and closing, and easy automation.
Butterfly valves
The butterfly valve also falls into the category of rotary valves. It is more compact than the ball valve because the closing mechanism is a flat dial.
They are of a quarter turn, they allow the circulation of the fluid using a circular disc that is rotating 90° to obtain the opening and closing position. Butterfly valves offer low shaft wear, low friction, and therefore low torque. It means that they are suitable for operation with either a manual or automatic actuator. It should be noted that they can be of the Wafer connection type, to be placed between flanges or Lug, these valves can be welded directly to a flange to avoid vibrations.
Plug Valves
A plug valve is a kind of quick on/off conduit valve. The friction caused by the movement between the sealing surfaces under the condition of being fully open can completely avoid contact with the flowing medium. Therefore generally can be used for the medium with suspended particles.
The advantages of the plug valve are it is of one-piece body, top entry, simple structure, easy in-line maintenance, leak-free, and can withstand higher strength of the piping system.
Chemical industry mediums have strong corrosion, so valve bodies used in the chemical process must have strong permeability and be resistant to intergranular corrosion.