Different types of electric motors, including DC motors, AC motors, servo motors, stepper motors, and linear induction motors are used in industries for various applications.
When selecting a motor for a particular application, various factors such as voltage, duty cycle, and other parameters must be considered to ensure the motor is suitable for the intended purpose. If the motor selection is improper, reliable operation cannot be ensured.
The motor has two main components: the stator and the rotor. The stator is stationary, and the rotor is rotating. The AC motor has a stator and rotor. The DC motor has an armature and field. The field remains stationary while the armature rotates in the DC motor. The magnetic field is produced by the stator for AC motors or by the field for DC motors.
The magnetic field generated by the field winding interacts with the armature current and produces torque, and the motor rotates. Similarly, the stator of the AC motor produces a rotating magnetic field, which induces a voltage in the rotor winding and causes rotor current to flow. The interaction of the magnetic field and the rotor current produces a torque that rotates the motor shaft.
Types of Electric Motors
The three main types of electric motors are AC, DC, and special-purpose motors.
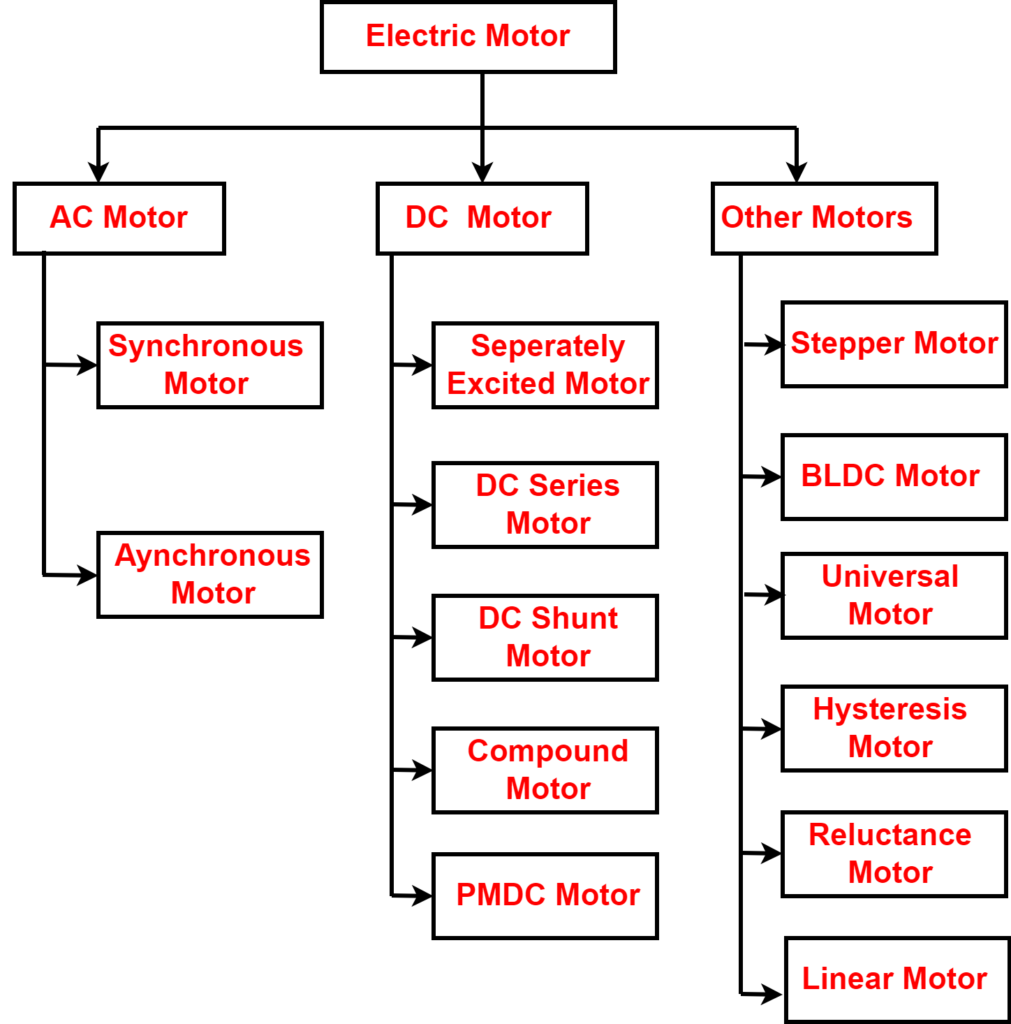
Types of AC Electric Motors
As its name suggests, AC motors work on alternating voltage.
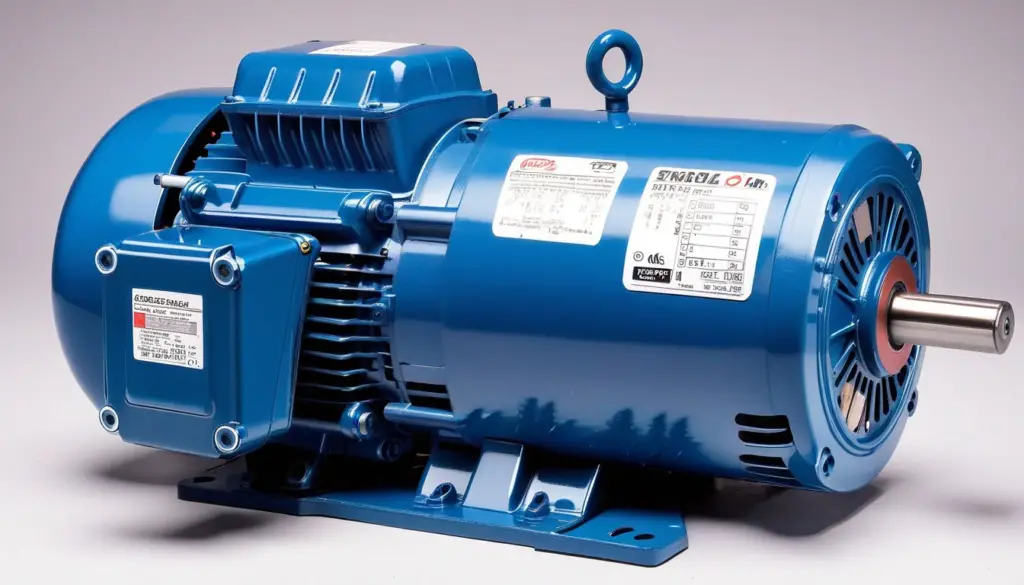
There are two types of AC motors: they are-
- Synchronous Motor
- Asynchronous Motor or Induction Motor
1. Synchronous Motor
A synchronous motor is an electric motor that operates at synchronous speed. When the AC supply voltage is applied to the stator windings, a rotating magnetic field is produced, which rotates at the synchronous speed. The synchronous speed depends on the supply frequency and poles. The following mathematical expression expresses the synchronous speed.
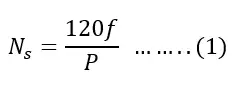
The rotating magnetic field travels through the air gap and induces an AC voltage in the rotor windings, causing rotor current to flow. The rotor current interacts with the rotating magnetic field, causing the rotor to rotate at the same speed as the magnetic field. A synchronous motor with four poles and a frequency of 50 Hz has a synchronous speed of 1500 RPM, which means that the rotor shaft will rotate at 1500 RPM.
The synchronous motors require a starting mechanism as they do not self-start. The damper winding provides the necessary starting torque.
The synchronous motor can function for both leading and lagging power factors. It maintains a constant speed regardless of the load, meaning that changes in load do not affect motor speed.
These motors are used where speed accuracy is desired. These are used in industrial drive, power generation, robotics, and electric propulsion systems.
Refer to this link to learn more about Synchronous Motor
2. Asynchronous Motor or Induction Motor
Asynchronous motors do not run at synchronous speed, so they are called asynchronous motors. They are also called induction motors. The slip between the synchronous speed and the rotor speed creates slip, which produces EMF in the rotor. The rotor is short-circuited, so current starts flowing in it. The rotating magnetic field and rotor current interact and produce torque, which rotates the rotor.
The synchronous speed of the induction motor is the same as that of a synchronous motor; however, its rotor speed is less than the synchronous speed. The rotational speed of an asynchronous motor can be calculated using the following mathematical formula.
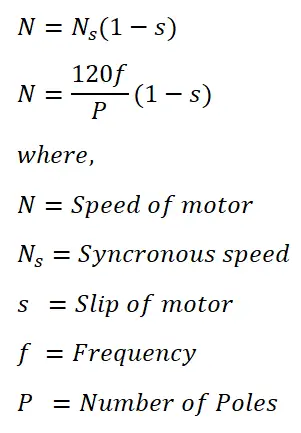
The speed of an asynchronous motor is determined by its frequency, number of poles, and slip. For a 4-pole, 50 Hz motor, the synchronous speed is 1500 RPM, and its actual speed is lower than the synchronous speed.
Induction motors are classified into single-phase and three-phase based on supply phases.
Based on their rotor construction, asynchronous motors are of two types: squirrel cage and wound rotor induction motors. In a squirrel cage motor, a ring short-circuits the rotor winding. The connections of the wound rotor winding are taken out through slip rings and carbon brushes to connect them to external resistances to improve the starting torque.
Squirrel cage induction motors are widely used with variable-frequency drives called inverter-duty induction motors.
Types of DC Electric Motors
The main types of DC motors are series, shunt, compound wound, and PMDC motors.
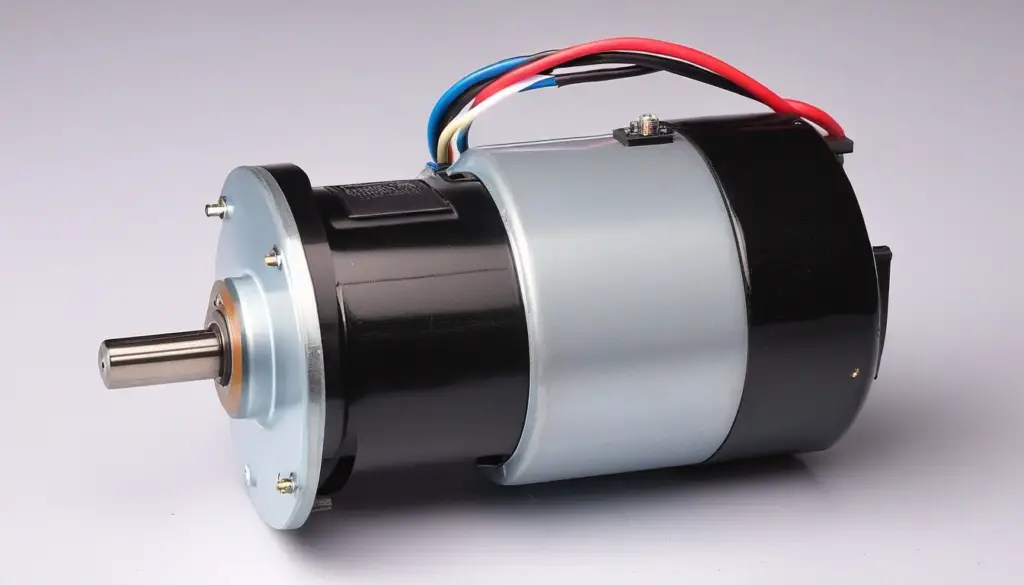
1. Separately Excited DC Motor
Separate DC voltage sources power the field and armature coils in separately excited DC motors.
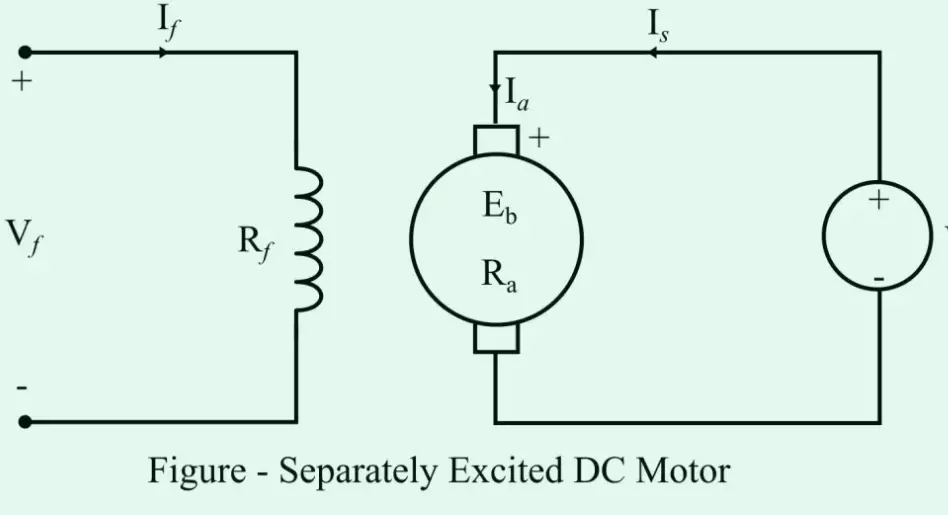
A constant DC voltage powers the field coil, while a variable DC voltage source powers the armature. The field coils produce a constant flux, and the speed of the motor varies by changing the armature voltage.
The motor’s torque is proportional to the product of magnetic flux and armature current. Since the flux is constant, the torque is proportional to the armature current.
2. DC Series Motor
The series DC motor is a self-excited type of motor, and its field winding is connected in the series with the armature winding. The field and armature winding are excited with a single DC source.
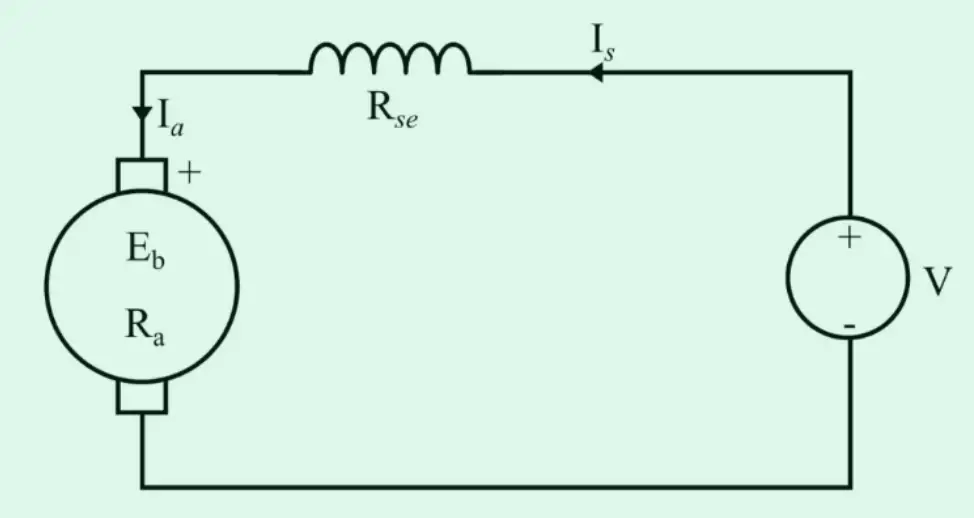
The series field winding of the motor is designed to have low resistance and carry the entire armature current. Practically, it is made of thick wire with fewer turns.
The torque is produced due to field flux and armature current interaction. The armature current flows through the field winding; therefore, the field and armature current are the same. The torque produced by the series DC motor is proportional to the square of the armature current.
DC series motor is suitable for those applications that require high starting torque.
3. Shunt DC Motor
In a shunt DC motor, the field and armature winding are connected in parallel, and the voltage across each winding is the same.
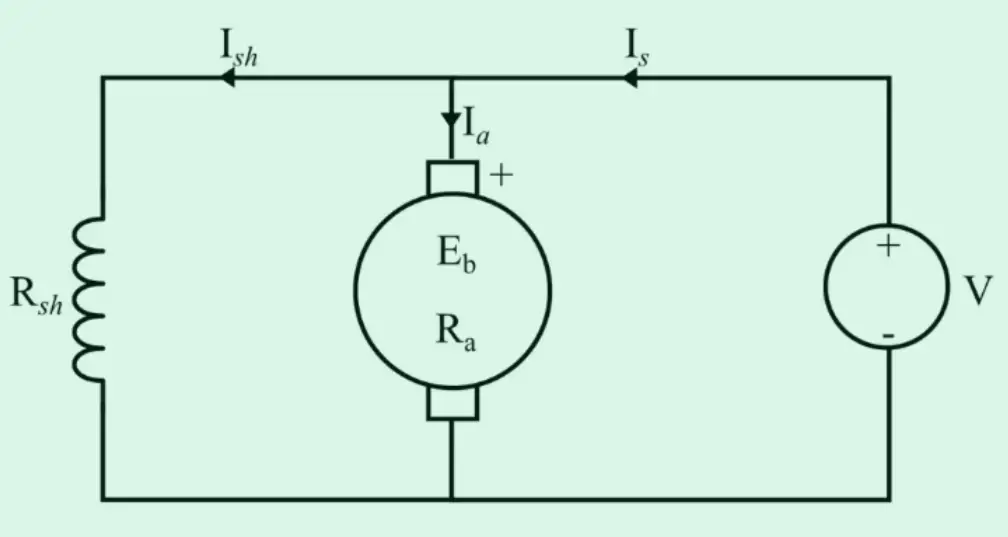
The field winding has high resistance and carries a fraction of the total supply current, and maximum current flows through the armature. These motors are used for those applications where constant speed is required.
4. Compound DC Motor
A compound DC motor is a type of DC motor that combines both series and shunt DC motors. This motor has both series field winding and shunt field winding, which work together to produce the necessary magnetic flux in the machine. In other words, the compound DC motor is a combination of the two types of motors and offers the advantages of both. There are two types of compound DC motors: short-shunt compound motors and long-shunt compound motors.
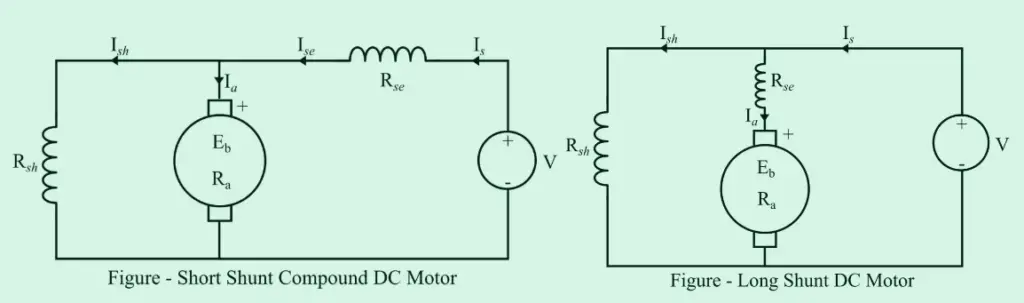
5. PMDC Motor
The PMDC motor uses a built-in permanent magnet in its rotor to create the required magnetic field. Its stationary part (stator) has a winding to generate an electromagnetic field. The interaction between these fields produces the rotational motion.
PMDC motors are more compact and lighter than other DC motors, making them suitable for limited-space applications.
These motors are suitable for applications requiring precise and controlled motion, such as electric fans, power tools, health care devices, home appliances, aerospace, consumer electronics, renewable energy, and some automotive systems.
Types of Special Purpose Electric Motors
Several special-purpose motors include servo, stepper, BLDC, universal, and linear induction motors.
1. Brushless DC Motors
Brushless DC (BLDC) motors are electronically commutated motors that do not use brushes for commutation. They use electronic controllers to change the direction of current flow in the motor windings.
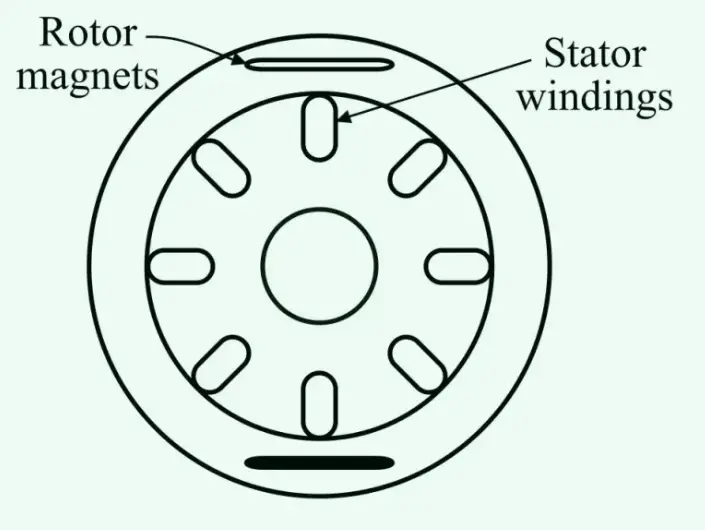
BLDC motors are highly efficient due to the absence of friction caused by brushes. This reduces wear and tear and requires less maintenance than brushed DC motors.
BLDC motors are used in electric vehicles, computer cooling fans, medical devices, consumer electronics, ceiling fans, and industrial applications.
Refer to this link to learn more about Brushless DC Motors
2. Stepper Motor
A stepper motor is an electric motor that divides a full rotation into equal steps. Unlike traditional DC motors, stepper motors do not rotate continuously but move in discrete steps. These motors are suitable for precise control of position and speed.
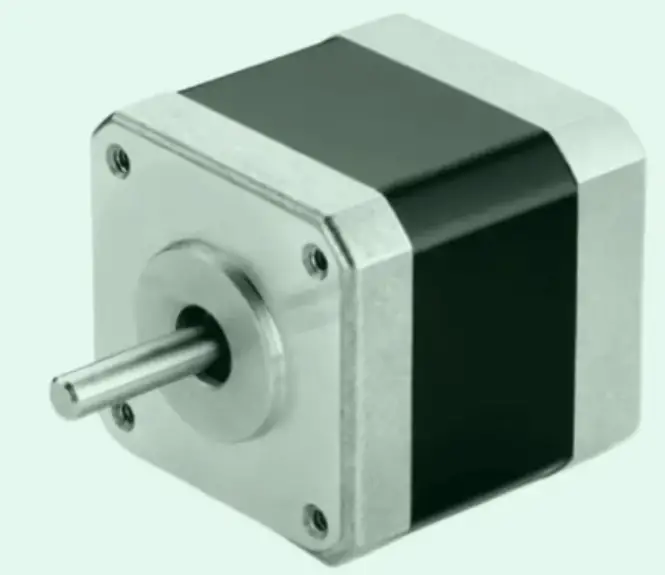
The motor rotates in steps of degrees, such as 5, 10, and 20 degrees. One rotation is considered 180 degrees. A stepper motor with a 5-degree step will take 36 steps to complete one rotation( 5 X 36 = 180 degrees).
The stepper motors are used in 3D printers, CNC machines, robotics, camera systems, printers and plotters, textile machinery, and positioning systems.
Refer to this link to learn more about Stepper Motors
3. Universal Motor
A universal motor is a DC series motor that can operate on alternating current (AC) and direct current (DC) power. It is called “universal” because it is designed to operate with a universal power supply. Universal motors are commonly used in various applications due to their ability to operate on different types of electrical power.
Universal motors are similar in construction to series-wound DC motors. They have a wound rotor (armature) and a field winding connected in series with the stator winding. These motors are designed to operate at high speeds above 3500 rpm.
The universal motors are used in power tools, home appliances, hair dryers, curling irons, kitchen appliances, handheld blenders, and vacuum cleaners.
Refer to this link to learn more about Universal Motors
4. Hysteresis Motor
Hysteresis motors are synchronous motors that operate on the principle of hysteresis loss in magnetic material. The rotor of a hysteresis motor is made of a high-coercivity magnetic material (a material that retains its magnetization well). The stator produces a rotating magnetic field, and due to hysteresis, the rotor follows this field with a slight lag.
Hysteresis motors are commonly used in applications that require low-speed, high-torque operation with minimal vibration and noise. Some examples include turntable drives in record players, tape recorders, and other applications where precise and quiet operation is crucial.
5. Reluctance Motor
The operation of the reluctance motor is based on the principle of magnetic reluctance. The rotor of a reluctance motor typically has salient poles (teeth). The stator poles align with the rotor poles when the motor is energized. The rotor is designed to minimize reluctance and achieve alignment with the stator poles. There are two types of reluctance motors: switched reluctance motors (SRMs) and synchronous reluctance motors.
Reluctance motors are used in industrial drives, electric vehicles, industrial automation, home appliances, power tools, HVAC systems, aerospace, and the oil and gas industries.
6. Linear Motor
Generally, the motors generate rotational motors, but the Linear motors produce a linear motion. The stator is flattened out, and the “rotor” moves past it in a straight line in a linear motor. Superconducting magnets are used in linear motors for cooling to reduce power consumption.
These motors are used in Maglev Trains, automation, robotics, and material handling systems.
Reference: Electric Motors-Wikipedia