A cable tray is a unit, or set of units, with their fittings forming a rigid structure to support cables and assist in channeling them.
The cable trays are composed of a thin metallic plate and electro-welded steel rods. Their construction is based on the international standard IEC 61537, which specifies the requirements for cable tray systems, tests, and specifications.
Purpose
Cable trays, or carrier trays, are mechanical support systems for cables. They provide a robust structural system and are used to accommodate and safely transport cables from one point to another in the project. Cables include power, armored, control, instrumentation, telecommunication, and fiber optic cables.
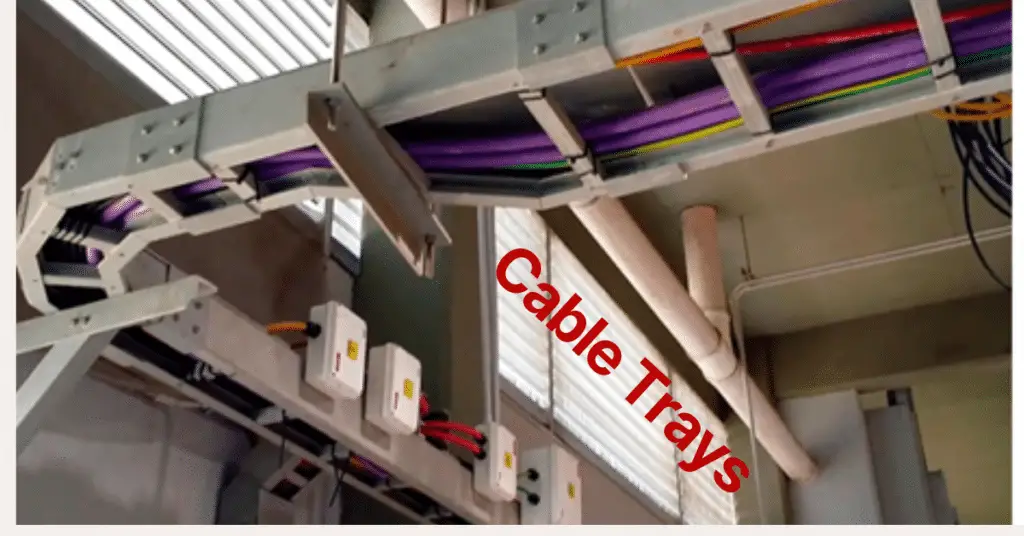
Cable trays provide an efficient, safe, and cost-effective solution for channeling electrical cables. Moreover, their simple installation reduces costs, making maintenance, and future expansions much easier. The primary purpose of a cable tray is to organize cables systematically. The cable trays keep the area clean and maintain the aesthetic look.
Types of Cable Trays
The following are common cable tray types.
- Ladder type
- Perforated type
- Solid bottom type
- Wire basket type
- Channel type
The project engineer or designer selects the type of cable tray for the project, based on the specific situation and environmental conditions. The cable tray selection depends on the number of cables, cable sizes, spacing between them, and total cable weight in the tray.
Ladder Cable Tray
As their name implies, these trays resemble ladders. Its structure consists of two longitudinal side rails connected by individual cross members. These trays allow the highest air flow between the cables and maintain high ventilation levels and heat dissipation so that the cables’ temperatures do not exceed operating temperatures.
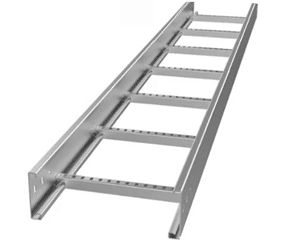
The rungs of a ladder-type tray are perforated, allowing cables to be securely fastened with cable ties. These trays are commonly installed in the upper section of buildings. Additionally, their open design prevents moisture buildup and provides better ventilation. This type of cable tray is useful because the ladder rungs allow easy access to the cables from the top or bottom.
Perforated Cable Tray
The bottom part of the perforated cable tray has openings, which provide ventilation and prevent overheating. It has about 60 % flat area which supports the cables laid within the longitudinal side rails. It offers greater support to cables than the ladder type.
These trays are used for instrumentation and power cables. They are perfect for organizing large industrial power or instrumentation cables and can be installed on any surface.
These trays provide enhanced security by fully enclosing the cables. Perforated cable trays prevent buckling or sagging. Their design offers better ventilation and maintains temperature even in a confined space.
Solid bottom Cable Tray
A solid or smooth background tray has no openings and is placed between the longitudinal side rails. It is designed to protect and support all types of cable. These trays offer maximum protection and prevent buckling or sagging.
These trays are mainly used in pipes with small-capacity cables. Their hermetic closure system completely isolates cables and prevents heat buildup.
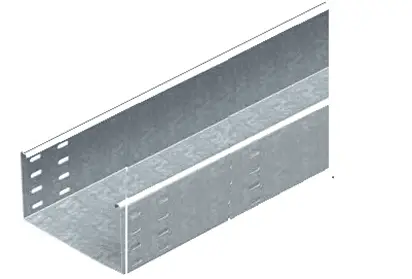
Solid background trays act as electromagnetic shields and protect control and data cables from RFI interference.
It is important to note that these trays accumulate moisture. This problem can be solved by performing perforations that allow continuous draining, as long as the trays are not used as a shield.
Basket Cable Tray
Basket cable trays are welded wire structures that support electrical cables in an orderly way, especially for control and data cables. These trays are also known as wire mesh cable trays. They provide ideal support for data communication cables (coaxial and braided pairs).
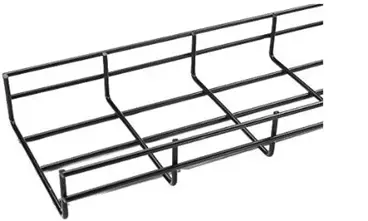
These trays are versatile and can be used in many situations. They allow horizontal and vertical adjustments by cutting as needed. They have a lightweight structure and open spaces. This design improves cooling, enhances electrical efficiency, and resists fire. They can also act as shields for cables.
Channel Cable Tray
The channel tray is narrow, making it a cost-effective option for supporting drop cables. It is used to carry one or two cables from the main tray to nearby equipment.
It is smaller than other types of cable trays. It prevents cable hanging and ensures a safe arrangement.
Materials of Cable Tray
Cable trays are available both in metal and non-metal types
1. Metallic
Metallic trays are available in Steel, Stainless Steel, Galvanized Iron, Low-carbon steel, and Aluminum. Aluminum trays are widely used because they have the following features:
- It Resists corrosion
- Excellent strength
- Lightweight.
Steel trays offer good electric shielding and have low thermal expansion. Stainless steel trays resist corrosion and can withstand high temperatures.
2. Non-Metallic
Fiberglass reinforced plastic (FRP).– It is lightweight, non-conductive & resists corrosion.
Accessories of Cable Trays
The accessories of the cable tray are shown in the picture below.
The following accessories are used with cable trays.
- Fastener
- Clamps
- Bends
- Reducers
- T-joint
- Internal risers
- External risers
- Short straight lengths
- Coupler plates
- Tray covers
- Tray crosses
- Tray supports, and
- Endcaps
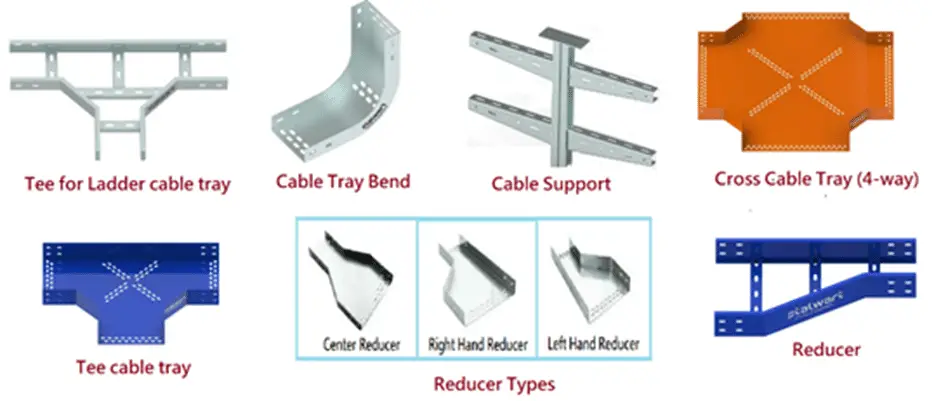
Advantages
The following are the benefits of the use of cable trays.
Easy Installation: One big advantage of cable trays is their quick and easy installation. No special training or expertise is required for cable tray installation.
Easy Maintenance: All the cables laid on the cable trays are visible, therefore it is easy to inspect and repair the faulty cables on open cable tray structures.
Less Expensive: One major advantage of cable trays is that they are more cost-effective than other methods of protecting wiring on the production floor.
Improved Safety: Reduces the risk of electrical hazards by keeping cables secure and organized.
Provides flexibility: Future cable additions can be made on the existing cable trays without requiring a major rework.
Disadvantage
The moisture can build up in the solid bottom type cable tray system.
Precautions
Cable trays in the open atmosphere should withstand harsh conditions, including exposure to atmospheric corrosion and corrosive chemical fumes. Therefore, selecting durable materials for the cable trays is essential.
As part of preventive maintenance, accumulations of dust and debris on trays are to be checked to avoid fire accidents in the plant.