There are many types of actuators that we use for controlling the motion of the control valve. Actuators are devices capable of generating a force from liquids, electrical energy, and air or gas. The actuator receives the command from a regulator or controller and gives an output necessary to activate a final control element such as valves.
The most common types of actuators are;
- Pneumatic
- Hydraulic
- Electric
Types of Actuators
Pneumatic Actuators
It converts the energy of pressurized air into mechanical movement. Pneumatic actuators work similarly to hydraulic actuators, except the driving force here is air.
A pneumatic actuator mainly consists of a piston or a diaphragm that develops a driving force. Keeps air at the top or bottom of the air chamber, allowing air pressure to force a diaphragm or piston to move a valve stem or to rotate its control element
Pneumatic actuators have widespread applications involving the opening and closing of valves. The actuators have many applications in process control like modulation, on/off control, packaging machinery, fuel car engines, and air compressors.
They are also common in robotics, automobile, aviation, and the transportation industry.
Diaphragm actuators & Piston actuators
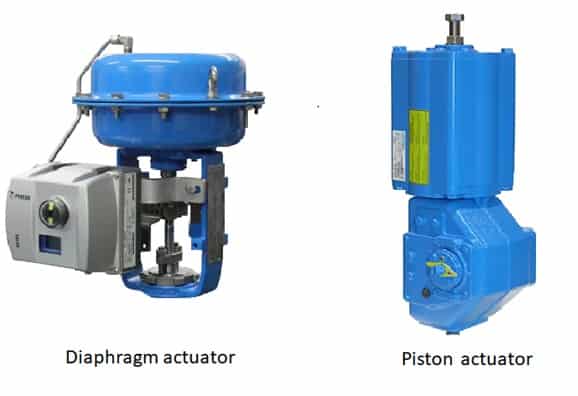
Diaphragm Actuator:
The diaphragm actuator functions on the principle of pressure on the diaphragm. When the air supply exerts pressure on the upper diaphragm and it generates downward thrust. The diaphragm has its connection with the stem. Thus, the downward movement of the diaphragm cause stems to move down and compress the spring. The diaphragm is a flexible material and responds to input signal variations.
On removing the air pressure, the spring creates a thrust on the stem, and the valve comes in its original position.
Diaphragm-type actuators are suitable for both modulating control and on-off service. These actuators provide an extremely long cycle life. They are suitable for low to medium thrust requirements.
Diaphragm Materials:
Molded nylon reinforced oil-resistant elastomer, nylon-reinforced nitrile rubber.
Piston Actuator:
There are two types of piston actuators.
- Spring (single action) and
- Without a spring (double action).
Piston actuator with spring type is a single action.
Piston actuator without spring is a two-position type actuator. Its working is based on the operating pressure on both sides of the inlet piston. The pneumatic pressure pushes the from the high-pressure side to the low-pressure side. We can use the valve positioner to make the stem displacement proportional to the signal pressure.
Piston actuators find their use where the stroke of a diaphragm actuator is too short or the thrust(force) is too small.
Pneumatic actuators are classified into linear and rotary.
Linear Pneumatic Actuators
The pneumatic cylinder consists of a piston inside a closed cylinder. The piston slides and transmits its movement to the outside through a rod. The linear Pneumatic actuator has the following.
- Rear and front covers,
- Ports for air connection,
- Sleeve for piston movement
- Piston
- Cushions to protect from shock,
- Static and dynamic piston seals
- Scraper ring that cleans the dirt on the rod
The pneumatic cylinder is the most common actuator for the pneumatic circuits, irrespective of their constructive form. There are two fundamental types of pneumatic actuators.
- Single-acting cylinders
- Double-acting cylinders
Single- acting cylinders
A single-action system has only one port, which supplies air to the chamber. A spring placed inside or outside pushes the piston into position. The inlet port receives the air and produces a working stroke in one direction. Please note that the single-acting cylinders can be push-type or pull-type, but, it is able to perform any one single action. It provides inherent fail-safe action either “air fail to close” or “air fails to open”.
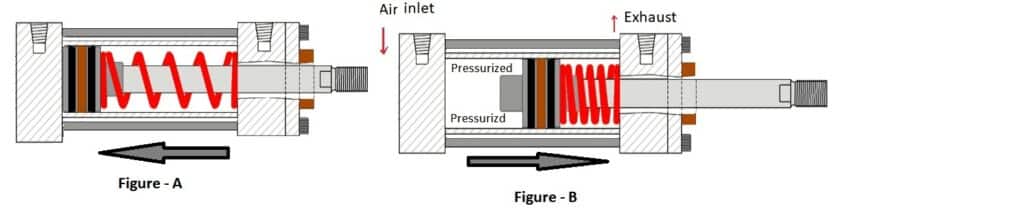
Figure – A:
In the above figure, the spring returns the air cylinder in the retracted stroke position (with no air pressure supplied through the rear end cap supply port). The air supply is usually through the “rear end cap” supply port. Finally, the air exhaust from the “ front-end cap” supply port.
Figure – B:
The spring returns the air cylinder in the extended stroke position (with air pressure through the “rear end cap” supply port). Hence overriding the spring.
We use single-acting cylinders in industrial applications such as ejecting, marking, and clamping extensively.
Double-acting Cylinder
A double-action system has two ports and is not spring-loaded. The port receives the air to move the piston. Meanwhile, the other port supplies air on the opposite side to push the piston into place. The concept is the same but they are different in the return method and the number of ports.
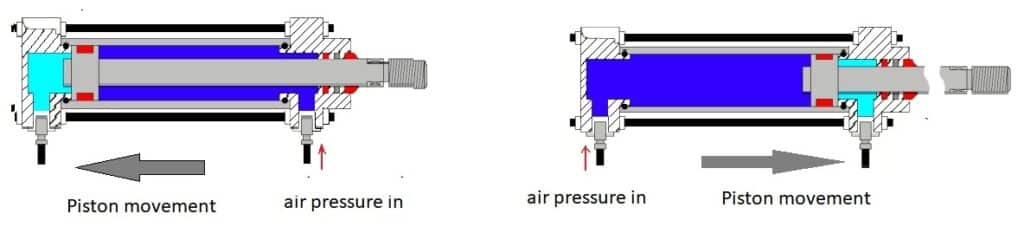
Double-acting cylinders have the possibility of doing work in both directions- forward and backward.
We use double-acting cylinders for a wide variety of industrial & non-industrial requirements.
Types of Actuators-Rotary Pneumatic Actuators
Rotary or rotary actuators are responsible for transforming pneumatic energy into rotary mechanical energy
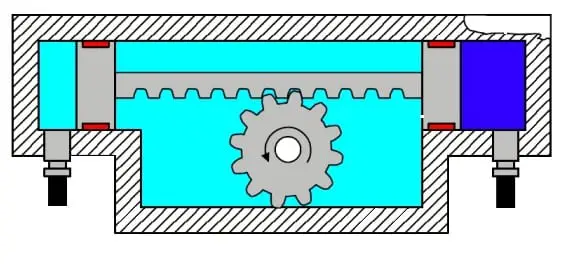
Single-acting pneumatic rotary actuator
We use single-acting rotary actuators for the actuation of 90 ° valves, such as butterfly and ball valves. The compressed air produces the activation in one of the directions of movement. and in the other by the force of the spring.
We can easily identify the installed spring sets from the outside by the shape of the end caps. In this way, it is possible to identify at first glance whether it is a single-acting or double-acting actuator.
Double-acting Pneumatic Rotary Actuators
We use double-acting rotary actuators for the actuation of 90 ° valves, such as butterfly and ball valves. Activation takes place in both directions by compressed air. The compressed air exerts a force on the plunger, further, the plunger exerts the force on the spindle. Its name is for the reason that they use both faces of the plunger (air in both chambers), so these components can do work in both directions.
Advantages of Pneumatic Actuators
- Pneumatic actuators are relatively simple, easy to do maintenance.
- The pneumatic actuators are relatively fast acting. As a result, the fastest cycle rate contributes productivity increase.
- In hot environments, Pneumatic actuators are safer than hydraulic or electrical actuators.
- They are especially in applications dealing with extreme temperatures because it uses compressed air, it does not require ignition or electricity.
- Double-action systems provide force even more quickly.
- Pneumatic systems also tend to be the cheapest option (cost-effective).
- Pneumatic actuators are long-lasting and easy to maintain.
Disadvantages Pneumatic Actuators
- They are best for light to medium applications because they supply limited power.
- Air compressibility and pressure losses make them less capable of producing higher forces.
- Oil or lubrication can also pollute the air.
- We should take care of monitoring the air for moisture content to avoid performance issues.
Types of Actuators-Hydraulic Actuators
A hydraulic actuator part of the hydraulic system. It uses hydraulic cylinders with pistons. A hydraulic actuator is a device that transforms fluid pressure energy into mechanical energy.
Hydraulic actuators use incompressible liquids to generate mechanical force. They produce linear displacement. The hydraulic actuators use oil as a fluid. We use hydraulic actuators to transmit power, speed, and force in different machines and devices.
Advantages of Hydraulic actuators
- They can hold constant force with less oil circulation.
- Hydraulic actuators produce much force.
Disadvantages Hydraulic actuators
- Many hydraulic spares, constant monitoring, and high maintenance.
- They require a lot of power supply, as well as regular maintenance.
- Heavyweight and size.
Electric Actuators
The electric actuator is a very simple actuator in compassion to pneumatic or hydraulic actuators because it requires electric power as a source of energy. As electric energy can travel long-distance, it is possible to mount the electric actuator at the exact location. Thus, there is no restriction of mounting distance from the source end.
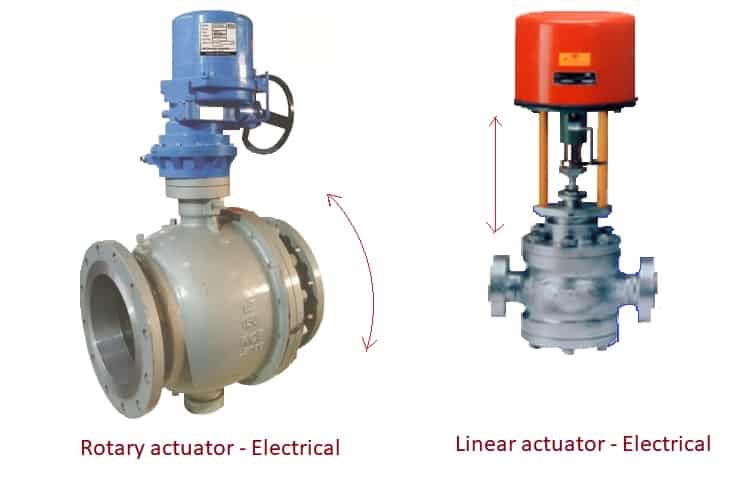
There is a lot of models and it is easy to use them with standardized electric motors according to the application.
Modern actuators have special components such as monitoring relays, stuck valve protection, limit switches, torque, thermostat, etc. The current technology allows operators to operate & control the electric actuators remotely through a two-wire connection. Even, many electric actuators can communicate to one PLC through a Profibus. Thus, it is possible to connect an electric actuator to a network.
Advantages of Electrical Actuators
- The electric actuator has large output thrust and high stability.
- Fast and highly precise operation.
- Electric actuators relatively have better accuracy and repeatability.
Disadvantages of Electrical Actuators
- Size of the actuators may be large.
- Electric actuators are not suitable in a flammable and hazardous atmosphere.
- It requires professional personnel with a higher technical level to operate and maintain it.
- Safety is lower than the other two actuators.
Read Next:
Images are very awesome, nice article with so much information about control valves.
Thanks