A stranded conductor is a type of conductor used in electrical power transmission. In a stranded conductor several thin wire threads known as strands are taken and twisted or intertwined together to make it capable of carrying the required amount of electrical current from sending end to the receiving end.
Efficient transmission of power from the power station with minimum losses is of utmost importance. AC power while being transmitted to the distributing stations, is subjected to various losses like impedance losses, skin effect, corona losses, etc. Stranded conductors address the problem of skin-effect specifically. So, in the subsequent section, we are going to learn about skin-effect and how exactly stranded conductors address this issue.
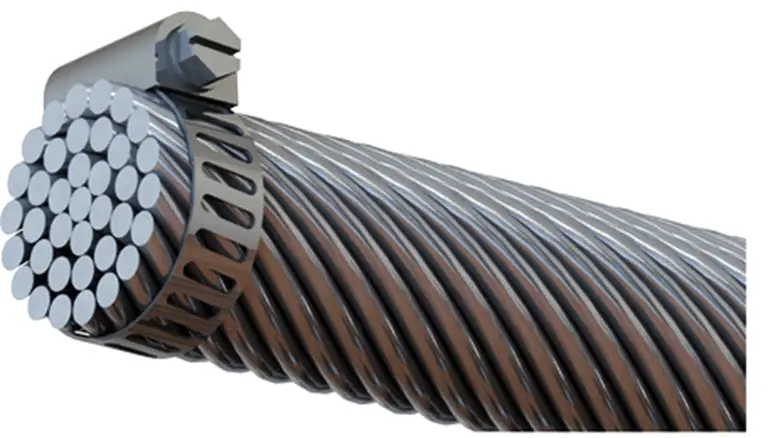
Solid Conductor Vs. Stranded Conductor
A natural question that may come up is why we are not using solid conductors instead of stranded conductors. This is because the problem of skin effect is very much related to that of the solid conductor due to which we have to make use of stranded conductors.
A solid conductor is one in which there are no wire strands and the current passes through it uniformly. The power transmitted is AC and the alternating current when passing through a conductor causes the generation of a time-varying magnetic field. This happens within a solid conductor as well. For a good conductor, a very small or negligible amount of this magnetic field leaks out while a greater proportion of it links within the conductor itself.
This time-varying magnetic field causes an emf to be induced within the conductor. According to Lenz’s law of electromagnetic induction, the generated magnetic field flux opposes the very cause of its own creation. Therefore, the induced emf is such that it tries to oppose the current flowing through the conductor in order to reduce the magnitude of the generated magnetic field.
Because of this, the current flowing through the conductor reduces and tries to find a path of less resistance. As the magnetic flux linkage is almost zero outside the conductor, the current begins to flow through the periphery of the solid conductor. This phenomenon is known as Skin-effect. Here, the current instead of flowing through the conductor begins to flow through the outer body or “skin” of the conductor. Skin effect is a problem because the conductor is not effectively used as the current distribution in the conductor is not uniform. It is higher through the periphery as compared to the core.
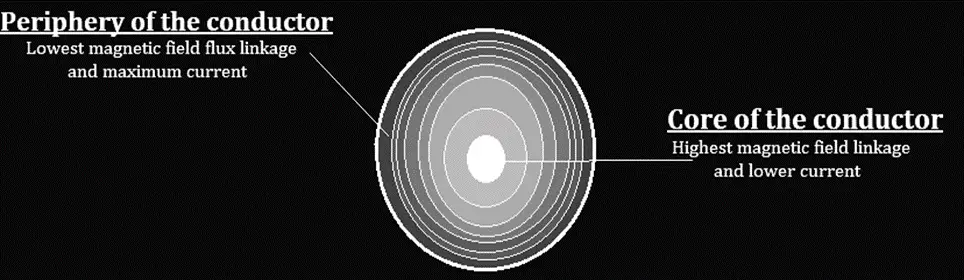
Cross-section of a solid conductor and skin effect
This effect can also be explained in terms of skin depth. The (electric current per unit area of the conductor) as we move from the surface of the conductor to the core is given by;
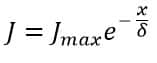
Where J is the current density, x is the distance measured from the surface of the conductor i.e., from x=0 to x=R (Radius of the conductor which means the surface of the conductor). is the skin depth of the conductor.
It is evident from the above equation that for x=0 i.e., at the surface, the current density or the current per unit area is maximum and falls exponentially to its minimum at the core.
To avoid this problem of skin effect, stranded conductors are used in place of solid conductors. In the case of stranded conductors, a number of strands are taken together and twisted. This is then placed inside the necessary protective enclosure i.e., the body of the cable. In the case of a solid conductor, the current wasn’t able to flow through the center and most of it used to flow through the skin because of the high magnetic field and induced emf at the center. In the case of the stranded conductors, the current flow through the periphery of each strand, and thus there is a uniform distribution of current through the conductor.
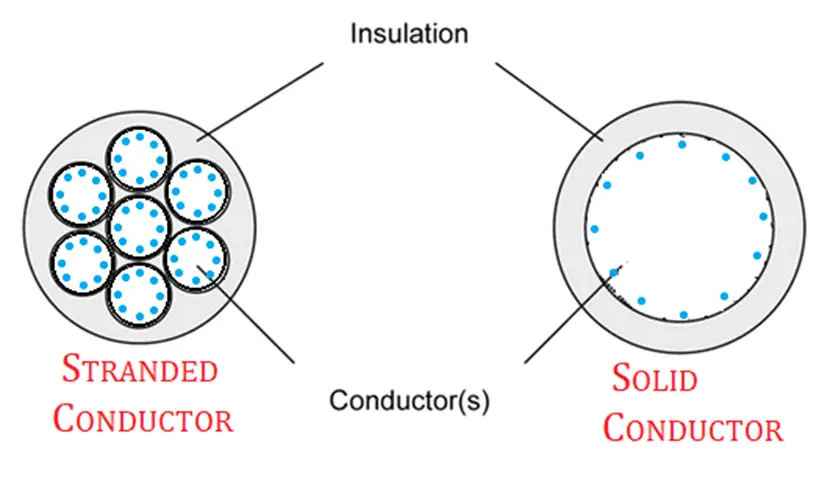
The image above shows the cross-sectional view of a stranded and a solid conductor. It is clearly evident that in the case of the stranded conductor, the electrical current passes through each strand and thus the magnetic field within the conductor or the induced emf is weaker as compared to that of the solid conductor (as shown by the blue dots).
The electrical cross-sectional area of the conductor increases in the case of the stranded conductor and thus the resistance of the conductor reduces allowing it to carry a higher current.
The total number of strands in any conductor is given by;
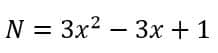
Where N is the total number of strands in a stranded conductor and x is the number of layers in the conductor.
The diameter of the conductor is given by;
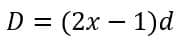
Where D is the diameter of the conductor and d is the diameter of each strand.
The Number of Strands and Diameter for a number of layers are shown in the below table.
Number of Layers ‘x’ | Total no. of strands N = 3x2 – 3x + 1 | Diameter of conductor D = (2x – 1)d | Cross Sectional View of Stranded Conductor |
1 | 1 | d | ![]() |
2 | 7 | 3d | ![]() |
3 | 19 | 5d | ![]() |
4 | 37 | 7d | ![]() |
Advantages of Stranded Conductors
The followings are the advantages.
- Increased Flexibility: Stranded conductors are more flexible than solid conductors. This makes them easier to work with in applications where the cable needs to be bent or moved around. This property makes the stranded conductors suitable for those applications where frequent movement or vibration happens. The stranded conductors are less prone to break or fatigue over time.
- Increased Surface Area: The multiple strands of wire in a stranded conductor provide a greater surface area for the conducting electric current through it. This reduces the resistance of the wire, which in turn reduces the amount of heat generated and energy lost during transmission.
- Improved Current Carrying Capacity: Stranded conductors can carry more current than solid conductors of the same diameter. This is because the multiple strands of wire increase the overall cross-sectional area of the conductor, which reduces the resistance and allows for more current to flow.
- Resistance to Breakage: The multiple strands of wire are more resistant to breakage due to vibration, bending, or other mechanical stress.
- Better Flex Life: The repeated bending and flexing of stranded conductors during use can cause strain on the wires. However, the multiple strands of wire in stranded conductors distribute this strain more evenly, leading to a longer flex life.
- Reduced Skin Effect: Stranded conductors have a smaller skin effect than solid conductors, meaning that they have a more even distribution of current across the cross-section of the conductor. This is particularly important for high-frequency applications where the skin effect can cause significant power loss as the skin effect is dependent on the frequency of the current.
Disadvantages
The followings are the disadvantages of stranded conductors.
- Cost: The stranded conductors are costlier than their solid counterparts as more manufacturing process is required in the case of stranded conductors.
- Less mechanical strength and tensile strength: These types of conductors have less mechanical and tensile strength as compared to the solid conductors and, that is why these types of conductors have more sag.
- Rough surface Area: The surface area of the conductor is not smooth and thus the electric field distribution is not uniform which results in increased Corona loss.
- Moisture Absorption: The multiple strands of wire provide a greater surface area for moisture to collect, which can lead to corrosion and degradation of the wire over time. A small gap between the wire strands can cause moisture and other contaminants to accumulate which can cause corrosion and reduced conductivity over a period of time.
- Spirality effect: Due to the spirality effect, the required length of the conductor is more than compared of a solid conductor. This incremental increase in the length causes the DC resistance of the conductor to increase slightly. However, the overall reduction in the skin effect compensates for the increased resistance.
- Difficult to terminate: It is easy to terminate a solid conductor, however, it is rather difficult to terminate a stranded conductor. It needs to ensure that all the strands of the stranded conductor are properly connected. If any of the strands remain unconnected, then there will be poor contact resistance that may cause reliability issues as well as safety hazards.