This article describes the major steps in PLC system design. Programmable Logic Controllers PLCs are an important component in industrial automation, and it is considered in the level L1 of industrial automation. The PLC processes the field IOs and works according to the logic written in it.
Without the PLC, it is not possible to work at higher levels like cloud networks or IoT. This is because cloud networks or IoT cannot work with field devices and get data from them. Thus care must be taken while designing a PLC system properly. There are some procedures, considerations, and factors which need to be taken care of before choosing a PLC system.
PLC System Design
Some common steps that are crucial for designing of PLC are:
- The Environmental Specifications
- The Grounding and Earthing
- Safety
- The Networking
- Field Devices and the IO count
- Proper Grouping of Devices
- Field Wiring Voltage Levels
- Program Complexity and Redundancy
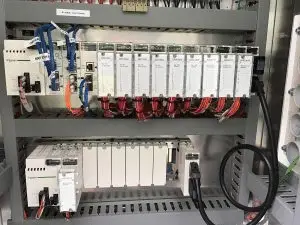
Now, we will discuss the Steps in PLC System Design.
1. Environmental Specifications
All electrical devices have some amount of environmental design constraint. The PLCs are also a type of electronic device and PLC components are very sensitive to environmental effects. So, it is important to see that no damage is caused because of any abnormal surrounding effect. The PLC must be able to perform functions that are mentioned in the catalog.
Some basic environmental factors which need to be considered are ambient temperature (during operation and storage), relative humidity, operating altitude, and mechanical stress for example vibrations.
The PLC installed should meet the nearby environmental specifications. When the temperature is outside the operating range whether extremely hot or cold, it is advised to use a hard-rugged PLC that would meet the given specifications. Some supporting equipment like fans, air conditioners, heaters, etc can be used when using PLC in such an environment.
2. Grounding and Earthing
Grounding and earthing are crucial aspects of designing a PLC system. If there is improper grounding, it can result in physical hazards, electrical equipment damage, and life loss. In a PLC, there are grounding points in the power supply and input-output terminals. During the installation of the PLC panel, it is important to ensure that the ground is connected at each and every point available.
There are two types of earthing in a PLC panel. They are instrument earth and power earth. The PLC input and output card should be connected to the instrument earthing. They should not be connected to power earthing. It must be noted that the voltage between earthing and neutral should always be less than 0.5V.
3. Safety Concerns
The safety concern is very paramount in PLC system design. In an industry, a PLC will deal with many critical field devices. Hence it is very important to look at the safety aspect. The PLC must be programmed in such a way that digital outputs must be assigned for a hooter, fault lamp, tower lamp, and buzzer. This will alarm the operator whenever there is a fault.
It is advised to have the safety review at the actual site to check whether it can be impacted by any mechanical, environmental, thermal, electrical, or chemical hazard or not.
Safety PLCs are also available. These have safety integrity level functionalities that deal with different types of IO safety and programming safety. They can detect permutations and combinations of failures to safely shut down the system.
Also, based on the process criticality, different PLCs with different scan times are available.
4. Networking
A PLC needs to deal with external communications with third-party or same-party devices at some other point. For communication to provide more flexibility in dealing with data, we use many protocols in communication with field devices, for example, SCADA. Therefore, networking
The communication can be sensitive to noise or some other electrical disturbances, it is thus important to properly choose the cable with shielding. In an Ethernet protocol, it is recommended to provide an Ethernet hub switch in the panel, whether managed or unmanaged. This is done so that many people can use data from it.
5. Field Devices and IO Count
When a PLC is chosen, the number of IOs and field instrument types are already taken into consideration. The proper knowledge of voltage and current is required for working with field devices. Based on this, the required PLC and cabling length are decided. It must be noted that it is always advisable to consider a minimum of 20% spare in IO counts. This gives flexibility in case of end-time additions in IOs.
In case the distance between PLC and the field device is more or if the PLC would be installed in a hazardous area, then barriers and isolators are also installed within the panel. In the case of analog IOs, properly shielded cables are used because they are more prone to noise.
6. Grouping of Devices
In a PLC, a proper grouping of devices is done according to the voltage level in the PLC panel during design. This will make sure that the AC and DC devices are grouped separately, for example, circuit breakers, relays, terminal boards, power supplies, and transformers.
It is advised to keep these groups separate and not mix them. Also, the circuit breaker must not be kept near the PLC. It is better to keep isolation between the devices of the same voltage level.
Thus, troubleshooting will be easier, and unwanted performance and noise in the panel can be reduced. When an AC and DC device are separated and grouped, the panel looks more attractive. It also becomes easier to identify each and every device properly.
7. Voltage Level Based Field Wiring
In a PLC panel, both AC and DC voltages co-exist. When a particular field device is powered by a separate power source, it must be ensured to use the common point for working with it. Care must be taken so that the unwanted common field signals do get mixed, otherwise, they can damage the PLC or the field device.
8. PLC Program Complexity and Redundancy
The redundancy factor must be taken into consideration when designing a PLC. The PLC must be chosen accordingly. Also, the PLC should be able to perform the task in the required scan time, memory, and redundancy.
Programming Basics
The CPU of PLC will execute two different programs. They are:
- Operating system
- User program
Operating System
The operating system performs the function of organizing the entire functions, operations, and sequences of the CPU that are not associated with a control task. Some tasks of an operating system include:
- Handling of a hot restart and a warm restart
- Updating and outputting the process image tablets of input and outputs
- Execute the user program
- Detect and call the interrupts
- Manage the memory areas
- Establishes communication of programmable devices
User program
The user program is a combination of many functions that are required to process an automated task. This should be created by the user and must be downloaded to the CPU of the PLC. The user program performs the following tasks:
- Initialization of all conditions in starting the specified task.
- The reading and evaluation of all binary and analog input signals.
- The specifying output signals to all binary and analog output signals.
- The execution of interrupts and handling errors
There are many PLCs that range from small to high-end PLCs. All PLC manufacturers have their own dedicated software to program and configure the PLC hardware. The PLC programming language varies depending on the manufacturers. Some of these manufacturers have common programming languages and some have different languages. These languages are of two types. They are:
- Textual language
- Instruction List (IL)
- Structured Text (ST)
- Graphical Language
- Ladder Diagrams (LD)
- Function Block Diagrams (FBD)
- Sequential Function Chart (SFC)
The graphical languages are preferred in comparison to the text languages for programming a PLC because they are having simple and convenient programming features. There are some necessary functions and functional blocks which are present in the standard library of all PLC software. There are timers and counters, comparators, strings; numeric, arithmetic, bit-shift and calling functions, etc. in the functional blocks.
This is all about the PLC system design.