A self-actuated temperature regulator decrease or increase the fluid flow rate according to the rise or fall of the temperature at the measuring point. Thus, it regulates the fluid flow to control the temperature of a process medium.
The temperature regulators are usually denoted on the process flow diagrams (PFD) by the TCV symbol. Its application is limited to small load changes, laboratories, or where precision measurement is not concerned.
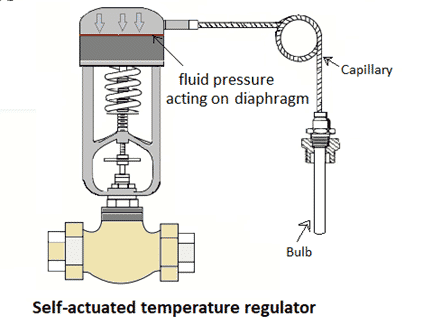
Self-actuated temperature regulators consist of actuating elements and actuators with a valve body as an integral unit. Actuating element consists of a bulb with a certain length of a capillary. The actuating part can be a diaphragm or bellows construction.
In general, the self-actuating regulators are the blind type. Typically, non-indicating type actuators have a lower profile and should be used in applications where space is limited. The precise indication is available scaled in °F and °C or separately scaled °F or °C dial thermometers.
The regulator bodies are fitted with a dial thermometer gauge for local indication to check the loop performance. A dial gauge indicating type actuators facilitates the operator to check the process temperature and adjust the new set-point.
Self-actuated Temperature Regulator Principle
- During self-operated temperature control, the sensing bulb absorbs thermal energy from the process medium. Thus, expands the fluid it contains which causes the actuator to regulate the stem position up or down.
- The fluid inside the bulb expands and exerts a force on the actuating mechanism. Thus, the force moves the stem downwards.
- By closing the valve in opposition to the spring force, the flow of the heating medium gets reduced.
- When flow reduces, the temperature comes down and the valve achieves a new position.
Types of Self-actuated Temperature Regulator
There are two types of Self-actuated temperature regulators.
- Direct operated
- Pilot operated
Direct-Operated Self-actuated Temperature Controller
In the direct-operated self-actuating type temperature regulator, the fluid expansion in the bulb drives the actuator. The power unit of the thermal actuator has a direct connection to the plug unit. Therefore, it develops the force and travels from fully open to close and vice versa.
Direct actuator regulators are purely proportional action, a compact and single unit in construction, the cost is less.
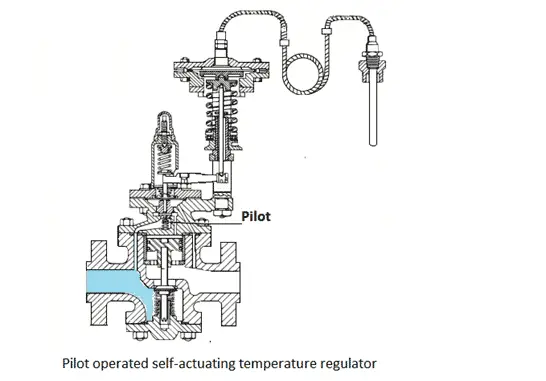
Pilot-Operated Self-actuated Temperature Controller
The thermal actuator moves a pilot valve, it may be internal or external or externally located. The pressure energy transfers from fluid to the valve plug through the diaphragm or piston. The pilot controls this energy. As a result, the valve plug attains a new position.
Pilot operated type self-actuated temperature regulators are fast in response, narrow proportional band. It consists of small-sized bulb elements. The pilot actuated temperature controller has good accuracy in comparison to direct actuated regulators.
Temperature Regulators
On the basis of the construction of sensing methods, there are two types of temperature regulators.
- Remote sensing regulators.
- Self-contained regulators.
Remote sensing regulators
In remote sensing regulators, the bulb is separate from the actuating element (diaphragm or bellows) of the thermal actuator. The bulb has its connection to the actuator by a flexible capillary of the required length.
Self-contained regulators
Self-contained regulators generally use liquid expansion elements or fusion-type thermal elements. It contains the entire thermal actuator within the valve body, and thus the actuator serves as the primary detecting element.
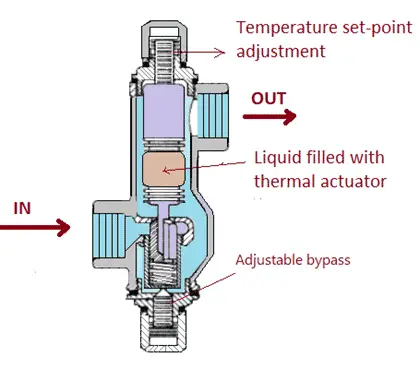
Thus, the self-contained style can sense the temperature of the fluid flowing through the valve. In other words, we can say the fluid is both the controlling agent and the controlled medium.
The self-contained style is simpler and cheaper. But we use it in limited applications such as regulating the temperature of coolant (water) etc.
Regulator Valve Body of Self-actuated Temperature Controller
The valve action refers to the relationship of stem motion to plug and seat position. The movement of the actuator produces the valve action, resulting from a temperature change.
The direct-acting regulator completes the heating control by reducing the flow of the heating medium on temperature rise. A direct-acting valve moves the stem down, as a result, it closes the valve.
We can achieve the cooling control by a reverse-acting regulator with a reverse-acting valve. The reverse-acting regulator increases the flow of coolant at rising temperatures. In the case of a reverse-acting valve, the valve opens as the stem moves down.
A three-way valve combines these on port opening and other ports closing on the downward movement.
In remote sensing designs, the primary sensing element of the temperature regulator is called the bulb. The proper fittings are used to install remote sensing design.
Special designs of Self-actuated Temperature Controller
Integral temperature gauge
Temperature indication is available. It usually consists of a pressure gauge sealed in a thermal system and calibrated to correspond to a particular range.
Fail-safe design
Failure loss of fill thermal actuator produces downward movement of the valve stem. As a result, the valve goes to the safe position producing a shutoff of the heating medium or flow of the cooling medium depending on the valve action.
Manual wheels
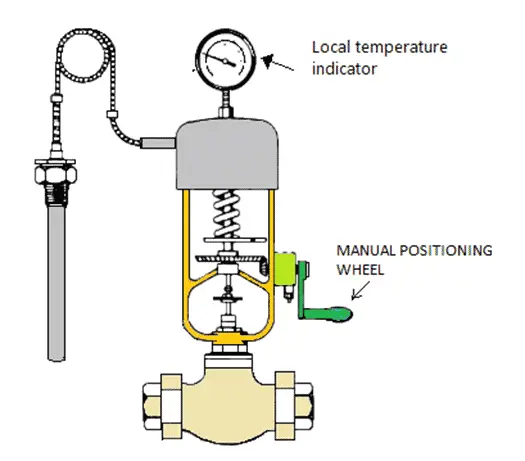
The temperature regulators are available with manual wheels, and dial thermometers in a few regulator versions as shown in the above diagram.
Advantages of Self-actuated Temperature Controller
- A unique feature of the self-actuated temperature control system is that it does not require an electrical or pneumatic connection to operate. Hence it is electrically safe.
- Self-actuated temperature regulators are mechanically robust. Therefore, it requires very less maintenance.
- Low maintenance and simplicity.
- Ideal for maintaining the temperature of storage tanks, process streams, and various types of industrial equipment.
- In general temperature, regulators are most successful on control applications having slow processes.
Disadvantages
The failure of the diaphragm causes the main valve to open. Further, this leads to the passage of process fluid through the main valve.
Applications
We use self-actuated temperature regulators for many process applications like duct hot air, and tank hot water temperature regulation.
Read Next: