In this article, we will discuss the definition, types, advantages, and applications of resistance heating or electric resistance heating. So let us begin with the basic introduction of resistance heating.
What is Resistance Heating?
The method of electric heating in which the resistive property of materials is utilized to generate the required heat is known as resistance heating. From elementary physics, we know that the resistance of a material is the property by which heat is generated when an electric current flows through the material. This property is used in several heating devices such as electric iron, electric heater, etc.
In resistance heating, a heating element made of a material of high resistance is employed for producing heat when an electric current flows through it. The operation of resistance is based on Joule’s law of heating. According to the Joules law, the heat produced by the material is directly proportional to the square of current passing through the material and the resistance of the material, i.e.
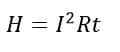
Where t is the time for which current flows through the material.
Principle of Resistance Heating
When the electric current is passed through a highly resistive material, the electrons traveling through the material collide with its positive atoms and result in the generation of heat.
Types of Resistance Heating
Resistance heating is classified into the following two types namely,
- Direct Resistance Heating
- Indirect Resistance Heating
1. Direct Resistance Heating
The type of resistance heating method in which the electric current is directly made to flow through the charge (a substance to be heated) so that the charge gets heated due to its own resistive effect is known as direct resistance heating.
In direct resistance heating, the flow of electric current through the material to be heated causes ohmic loss (I2R loss) in the substance itself and causes the material to be heated.
The schematic arrangement of the direct resistance heating is shown in figure-1 below.
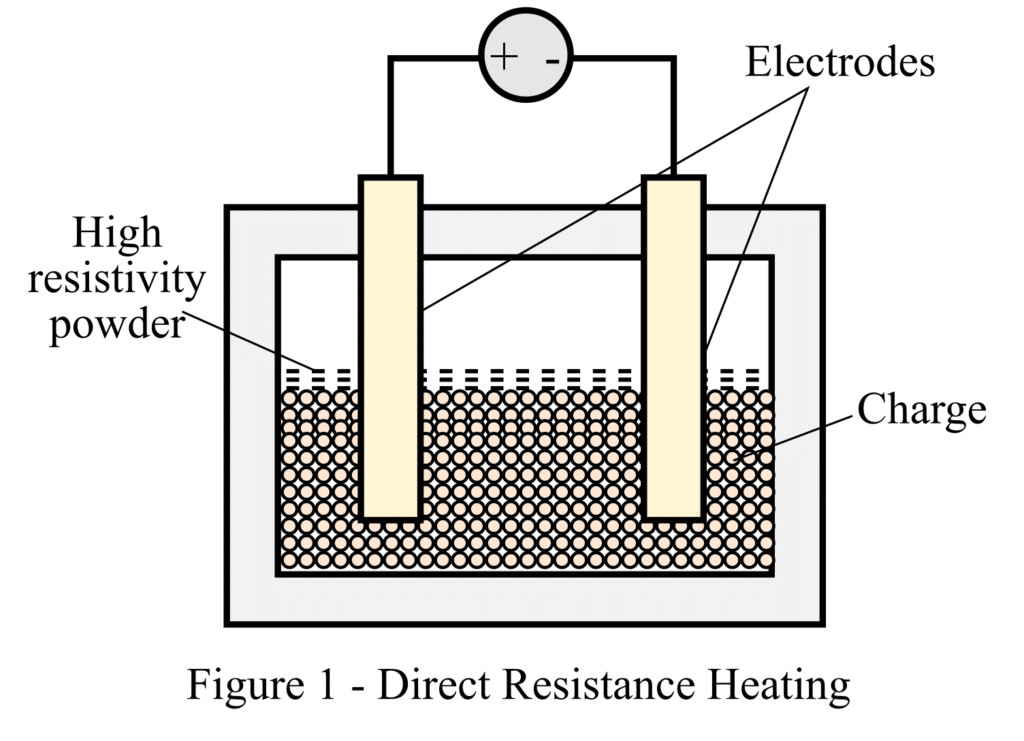
Here, the material or charge to be heated can be taken in any form, i.e. liquid, powder, pieces, etc. Two metallic electrodes are immersed in the material and connected to a source of electric supply. When electric current flows through the electrodes and charge, heat is produced in the charge due to its electrical resistance.
Advantages of Direct Resistance Heating
- The major advantage of direct resistance heating is that it is more efficient because heat is produced in the charge itself.
- Direct heating produces uniform steady heating at a higher temperature.
- It does quick heating of the material.
- It needs a minimum maintenance
- Reduced metal scale
Disadvantages of Direct Resistance Heating
- The major drawback of direct resistance heating is that this type of resistance heating is applicable to only materials which are electrically conducting like metals.
- Also, automatic control of direct resistance is not possible because there is no control of the current.
Application of Direct Resistance Heating
The followings are the applications of direct resistance heating.
Salt Bath Furnace
A salt bath furnace, also known as a salt bath heat treatment furnace is widely used for high-temperature heat treatment processes like tampering, quenching, and hardening of steel and other metals. It provides rapid and uniform heating with a selective localized heating
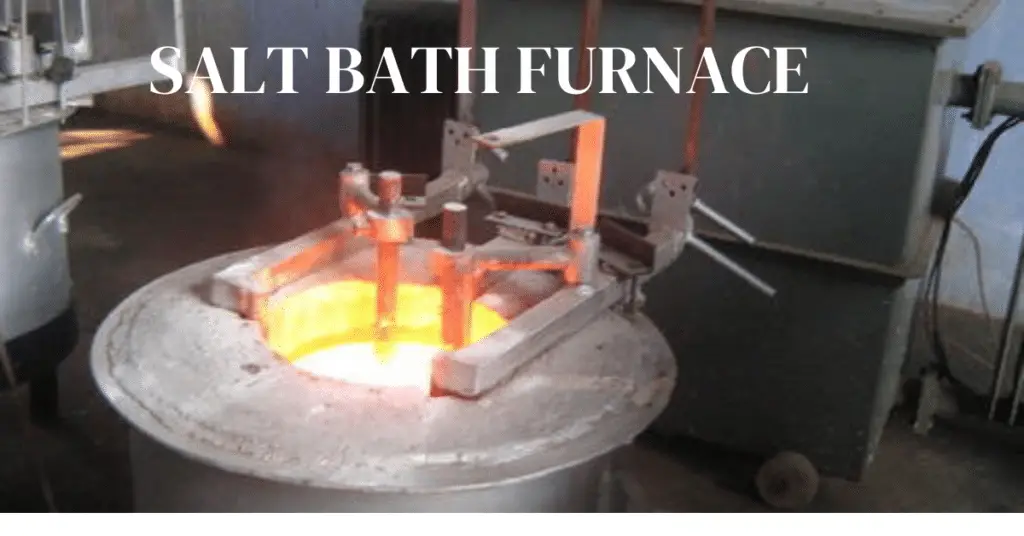
The furnace has a bath and sodium chloride with two electrodes immersed in it. When current flow through the electrodes that are immersed in the salt cause heating of the salt and the temperature of the salt varies between 1000°C-1500°C. The temperature of the salt depends on the type of salt used.
Electrode Boiler
The electrode boilers find their applications in water heating. It has a water tank and two electrodes placed in it.
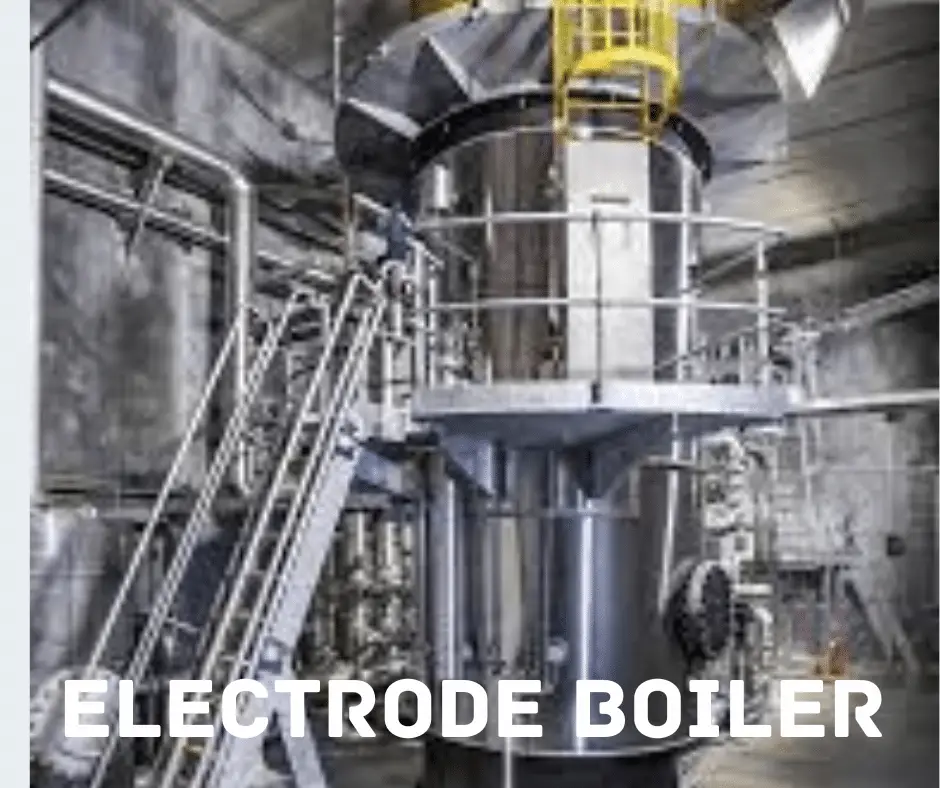
When we feed the electric supply to electrodes, the current flow in the water through the electrode to water, and the heating is produced because of the water resistance. The water tank is solidly earthed and connected to the earthed.
2. Indirect Resistance Heating
The type of resistance heating in which heat is generated in an element of high resistance by passing electric current and the charge is placed either above or below the element, is known as indirect resistance heating.
Therefore, in indirect resistance heating, heat is produced by a heating element according to the I2R law and this heat is then transferred to the material to be heated. The mode of heat transfer from the element to the charge could be either conduction or convection or radiation.
The schematic diagram of indirect resistance heating is shown in the figure-2 below.
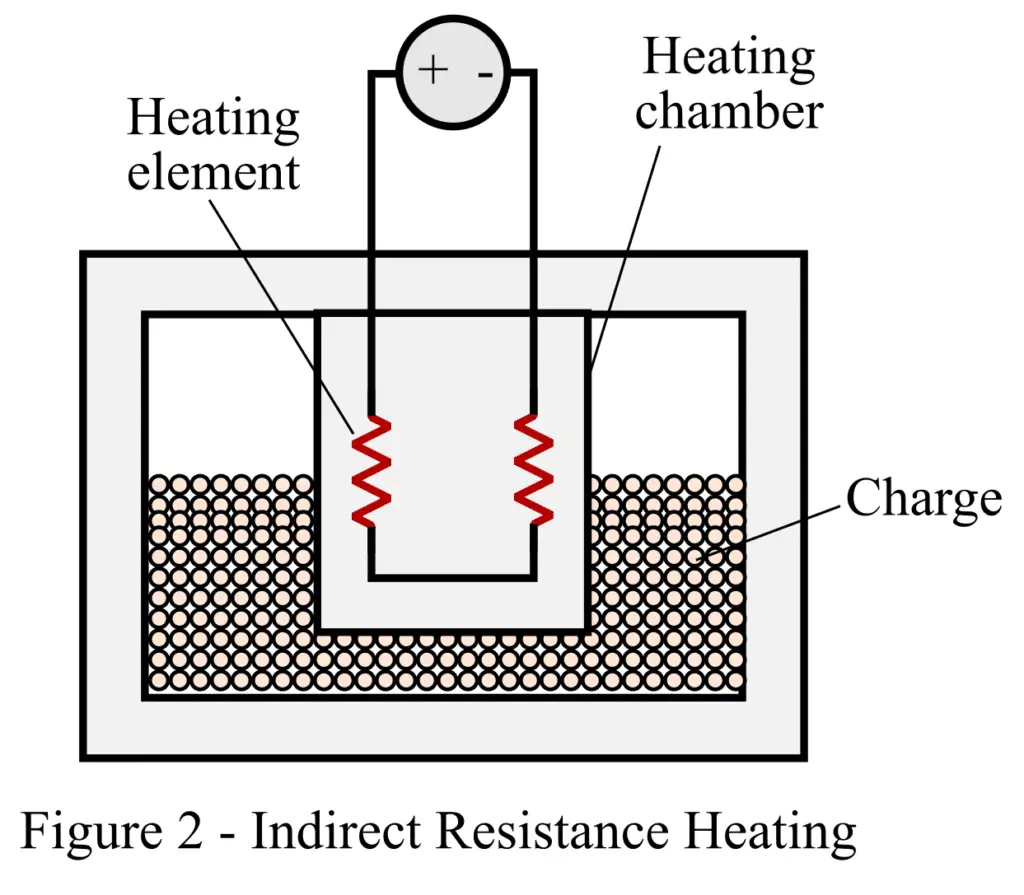
Here, a heating element is installed in a heating chamber and the charge is poured around the heating chamber. When electric current flows through the element, heat is produced and is transferred to the charge.
Advantages of Indirect Resistance Heating
- Indirect resistance heating provides uniform temperature.
- In indirect resistance heating, automatic temperature control is also possible.
- Indirect resistance heating can be used for heating almost all kinds of materials.
Disadvantages of Indirect Resistance Heating
- The time required for heating is longer compared to direct resistance heating.
- It is less efficient than direct heating because some amount of heat is lost during the transfer from the element to the charge.
- Explosion hazard with indirect resistance heating
Applications of Indirect Resistance Heating
The followings are the applications of indirect resistance heating.
Resistance Oven
The resistance oven has a chamber made of insulating material. The resistive elements are placed inside the oven. The element can be made in the form of strips or coils and these elements are placed on the top and bottom of the oven.
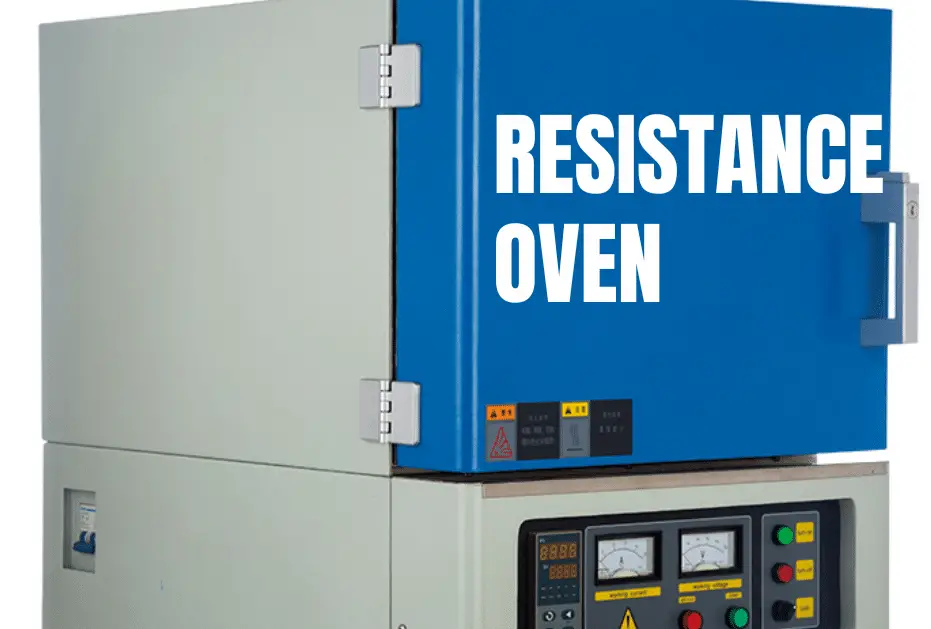
For high-temperature applications, two electrodes projected from the opposite walls of the oven are used to get high temperatures when current flows through these electrodes. The size and shape of the oven are made according to the applications.
The temperature of the oven can be controlled by varying the voltage or current, resistance, and time duration of heating.
These ovens are widely used for various applications like drying and baking of pottery materials, cooking of food, and heat treatment of metals.
Immersion Water Heater
The immersion water heater has a resistive coil placed in slotted cylinders of ceramic material.
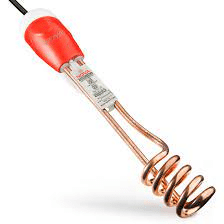
The Nichrome wire (80% Ni, 20% Cr) coated with magnesium oxide is used for the resistance coil. This material has the property of preventing oxidation of the element.
Temperature Control Methods of Resistance Heating
In resistance heating, temperature control is one of the crucial practices which is followed to maintain the temperature at the desired value. The temperature in resistance heating can be controlled manually as well as automatically. For controlling the temperature of resistance heating, the following three methods are used.
- By changing voltage across the element – In this method, the voltage across the heating element is changed by using voltage regulators or connecting series resistors or by varying the supply voltage. The increased voltage push more current through the element and hence the temperature raise, and the reduced voltage cause less current to flow through the elements and hence the lower temperature.
- By changing the element resistance – The temperature of the resistance heating can also be controlled by increasing or decreasing the resistance of the heating element.
- By periodically switching On and Off the supply – By periodically switching the supply to the heater, we can also control the temperature of the resistance heating. But this method is applicable to only small-sized resistance heating devices.
Characteristics of Resistance Heating Element
The following are the important characteristics of resistance heating elements:
- The heating element should have high resistivity so that a small length of the element can produce a significant amount of heat.
- It should have a high melting point so that it can withstand high temperatures.
- The temperature coefficient of resistance should be low so accurate temperature control becomes possible.
- At high temperatures, it should not oxidize.
Note – The most widely used heating element in resistance heating is made of either Nickel-Chromium or Nickel-Chromium-Iron or Nickel-Chromium-Aluminium or Nickel-Copper.