A pneumatic cylinder is also known as an air cylinder or pneumatic actuator. It is a mechanical device that utilizes compressed air to produce linear motion or force.
It is a common component in many industrial automation applications requiring controlled movement or force. Pneumatic cylinders are often used in conjunction with other pneumatic components like valves and actuators to create automated systems.
Table of contents
Principle of Pneumatic Cylinder
The basic principle of a pneumatic cylinder is based on the utilization of compressed air to generate linear motion or mechanical force. Pneumatic cylinders are devices that convert the potential energy stored in compressed air into kinetic energy (motion).
Parts of a Pneumatic Cylinder
The parts of the pneumatic cylinder are as follows.
- Cylinder Body
- Piston
- End Caps
- Seals
- Ports
- Tubes
- Rings
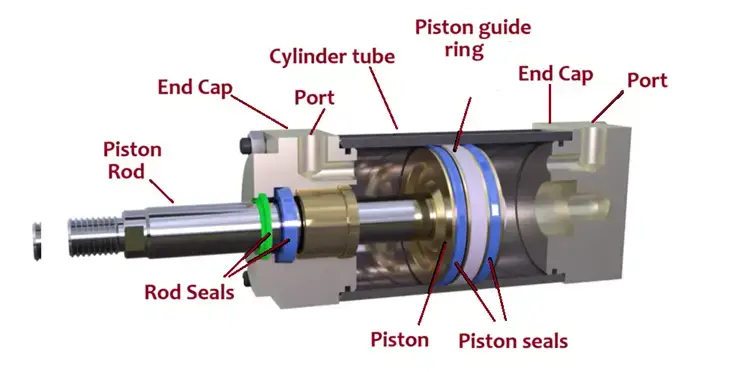
Cylinder body: The main housing of the pneumatic cylinder is a cylindrical housing or tube that contains the piston. Cylinder body is typically made of metals like stainless steel, aluminum are often used due to their strength and durability. Plastic or composite materials are used for corrosion resistance.
The choice of material for the cylinder depends on factors like operating conditions, strength, weight, and corrosion resistance.
Piston: Inside the cylinder body is a piston that moves back and forth along the length of the cylinder. The piston divides the cylinder chamber into two halves. The role of a piston in converting compressed air pressure into mechanical work makes it a fundamental component of pneumatic systems.
End caps: The cylinder has two end caps, one at each end. These end caps are securely attached to the cylinder body so that they provide structural support, sealing, mounting options, and port connections. These components help maintain a proper seal between the piston and cylinder walls and reduce friction as the piston moves. Some pneumatic cylinders have built-in cushioning mechanisms in the end caps.
Seals: These components of the pneumatic cylinder help maintain a proper sealing between the piston and cylinder walls and reduce friction as the piston moves. The use of seal material Polyurethane, Buna-N, Viton, and other depend on the temperature range.
Ports (Size and Type): Size like ½”, or ¼” etc. Type means BSP, NPT, etc. Ports in a pneumatics cylinder help in controlling the flow of compressed air. Compressed air is supplied to the cylinder through ports on the end caps. The air enters one of the chambers behind or in front of the piston, causing pressure to build up.
Valves: Valves control compressed air flow into and out of the cylinder, allowing for precise control of the piston’s movement. The cylinder can extend and retract or maintain a specific position depending on the valve configuration.
Pneumatic cylinders are valued for their simplicity, reliability, and ease of control. They are commonly used in manufacturing, automotive, robotics, and automation for tasks requiring precise and controlled linear motion or force.
Types of Pneumatic Cylinders
There are two types of cylinders.
- Single-acting cylinder
- Double-acting cylinder
Single acting cylinder
Push-type and pull-type single-acting cylinders are used in various applications to perform linear work, such as lifting, pushing, or pulling objects. They are both single-acting cylinders, which means they exert force in only one direction. That is in the pushing or pulling direction, with the return stroke typically being accomplished by an external force, such as gravity or a spring.
Types of Single-acting Cylinders
There are two types of single-acting cylinders.
- Push-type Single acting cylinder
- Pull-type Single acting cylinder
Push-type Single acting Pneumatic cylinder
A push-type single-acting cylinder is designed primarily for pushing or extending a rod or piston out of the cylinder’s housing.
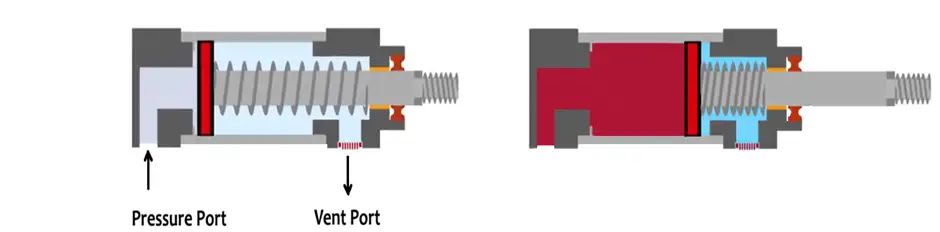
It typically consists of a cylinder barrel, a piston or rod, and a single port (usually on one end of the cylinder) through which hydraulic fluid or compressed air is applied.
When pressure is applied to the pneumatic cylinder, it forces the piston or rod to extend outward, pushing an object or performing some work.
The return stroke, where the piston or rod retracts back into the cylinder, is achieved passively through external forces, such as gravity or a spring. Some designs may include a spring or other mechanism to assist with retraction.
Pull-type Single acting cylinder
A pull-type single-acting cylinder is designed primarily for pulling or retracting a rod or piston into the cylinder’s housing.
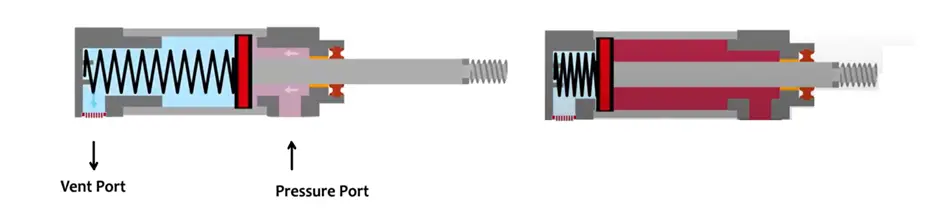
Similar to the push-type pneumatic cylinder, it consists of a cylinder barrel, a piston or rod, and a single port for applying hydraulic fluid or compressed air.
In this case, the cylinder is typically mounted in a way that allows it to be anchored to a structure, while the object to be moved is attached to the rod or piston.
When pressure is applied to the cylinder, it pulls the rod or piston into the cylinder, exerting a pulling force on the attached object.
Like the push-type cylinder, the return stroke is passive and is achieved through external forces or mechanisms.
Both push-type and pull-type single-acting cylinders perform linear work in one direction, but they are designed for opposite actions, pushing and pulling, respectively. The choice between them depends on the application’s specific requirements and whether the primary task is to extend or retract a rod or piston.
Double-acting cylinder
The following are double-acting cylinders.
- Standard Double-acting cylinder
- Tie-rod Cylinder
- Welded Cylinder
- Telescopic Cylinder
- Rotary actuator Cylinder
- Multi-position Cylinder
- Impact Cylinder
- Cushioned Cylinder
- Spring Return Cylinder
Standard Double-acting cylinder
This is the most basic type of double-acting pneumatic cylinder. A standard double-acting cylinder is a versatile actuator that can convert fluid pressure into linear mechanical motion in both directions. It plays a crucial role in many industrial and mechanical systems that require controlled and precise movement.
Tie-rod Cylinder
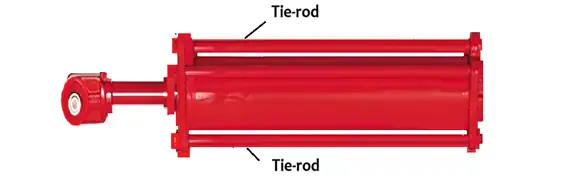
These cylinders are characterized by the presence of tie rods that run parallel to the cylinder barrel. These tie rods provide structural support and allow for easy maintenance and repair by disassembling the pneumatic cylinder. In industrial applications, Tie-rod cylinders are commonly used.
Welded Cylinder
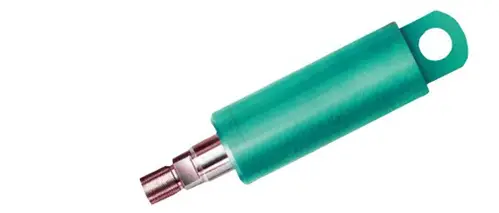
Welded cylinders have a one-piece construction with no tie rods. They are often more compact and suitable for applications where space is limited. Welded cylinders are robust and can handle high-pressure applications.
Telescopic Cylinder
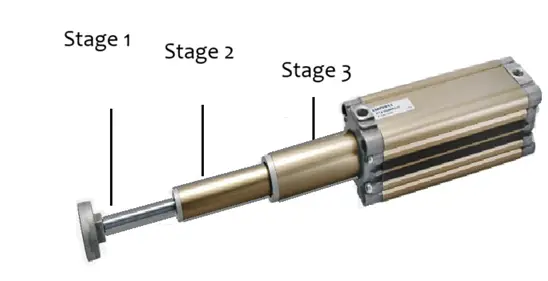
Telescopic cylinders consist of multiple nested stages that allow for an extended stroke length while maintaining a compact retracted length. They are often applied in applications requiring a lengthy stroke, but available space is limited.
Rotary actuator Cylinder
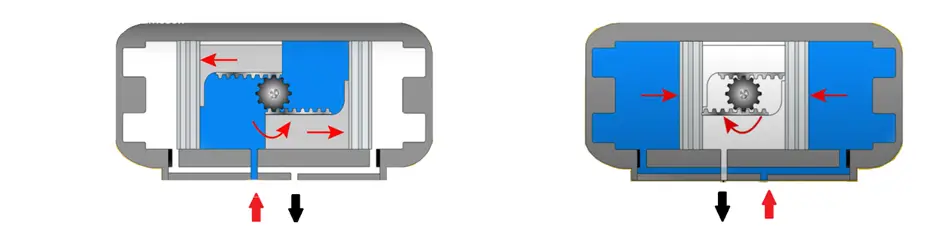
These cylinders provide rotary motion instead of linear motion. They are often used in applications that require a rotating movement, such as turning a valve or controlling a rotary motion.
Multi-position Cylinder
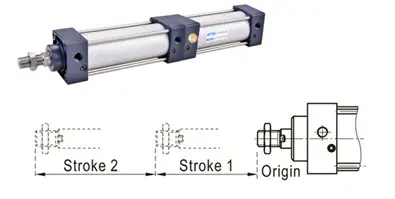
Multi-position cylinders have multiple ports and can stop at various positions along their stroke length. In applications where precise positioning is required, they shall be used. The pneumatic cylinders exert force by converting potential energy that comes from compressed air into kinetic energy.
Impact Cylinder
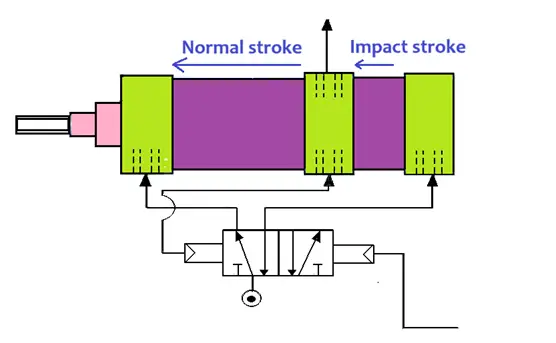
Impact cylinders are designed to deliver a sudden force at the end of their stroke. They are used in applications like stamping or compacting.
Cushioned Cylinder
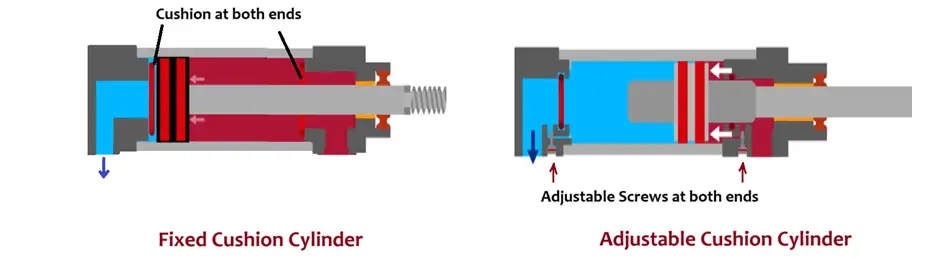
Cushioned cylinders have built-in shock absorbers to slow down the piston’s movement before it reaches the end of its stroke. This helps reduce impact and noise in applications where smooth operation is essential. Cushioning can be fixed or adjustable (external screw); selection can be based on requirements.
Spring Return Cylinder
While not strictly double-acting, spring-return cylinders use a spring to retract the piston when fluid pressure is removed. They are often used in applications where a fall-safe return is required.
The choice of a double-acting cylinder type depends on a combination of technical requirements, environmental factors, safety considerations, and budget constraints. Careful consideration of these factors will help us select the most suitable cylinder for specific applications.
Ordering Specifications of Pneumatic Cylinder
- Material
- Bore size,
- Stroke length
- Mounting style
- Seals
- Cushioning
- Port size
- Operating temperature
- Operating pressure
Applications
Single-acting and Double-acting cylinders have a wide range of applications in various industries. They offer flexibility and reliability in a wide range of applications.
Single-acting cylinders are used for simple applications where force is required in one direction. For example, in pushing, stamping, clamping, and lifting.
Double-acting cylinders are used in applications involving bidirectional force and precise control movement. For example, in linear motion, raising, lowering, opening/ closing valves, and material handling.