Introduction
An oil circuit breaker (OCB) is a type of circuit breaker that uses oil as an arc extinguishing medium. In electrical power systems, circuit breakers play a crucial role in protecting the system from faults by interrupting the flow of electricity during abnormal conditions like overloads or short circuits. The breaker’s contacts are isolated within an insulating oil. The circuit breaker’s contacts are opened under the insulating oil during a fault, creating an arc that generates heat and is dissipated by the surrounding oil. Oil circuit breakers are widely used in medium and high-voltage systems and are known for their reliability in handling large fault currents.
This article explores the construction, working, and types of oil circuit breakers in detail.
What is an Oil Circuit Breaker?
Definition and Basic Function
An oil circuit breaker is a device designed to interrupt electrical circuits under fault conditions. It uses oil as the insulating medium and as the arc extinguisher when the contacts separate. When a fault occurs, the breaker separates the contacts, and the resulting arc is extinguished within the oil, which helps absorb the heat and prevent the arc from continuing.
Purpose in Power Systems
Oil circuit breakers are integral to power systems, particularly in substations and power generation plants, where they protect critical equipment from high currents. By breaking the circuit during faults, they prevent potential damage to transformers, generators, and other components.
Construction of Oil Circuit Breaker
Major Components
Tank:
The core of the oil circuit breaker is the tank, which holds the oil used for arc quenching and insulation. The breaker has current-carrying contacts enclosed in this oil-filled tank. The tank is typically made of steel and designed to withstand high pressures caused by the decomposition of oil during arc quenching.
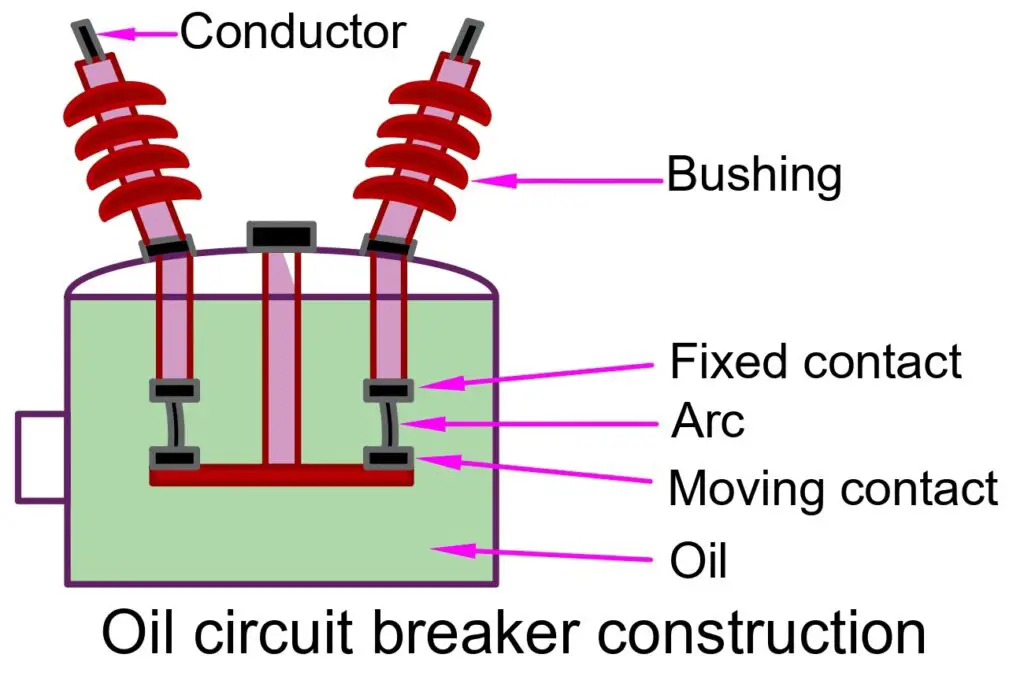
The breaker tank is securely bolted to withstand the vibrations that occur when high currents are interrupted. The oil tank has air filled at the top to cushion and control the displaced oil when gas is formed around the arc. It also helps absorb the mechanical shock caused by the upward movement of oil. The oil circuit breaker (OCB) includes a gas outlet fitted in the tank cover for removing gases.
Moving and Fixed Contacts:
These contacts are responsible for creating or interrupting the circuit. The moving contact is connected to the operating mechanism, while the fixed contact remains stationary inside the oil-filled tank.
Arc Quenching Chamber:
This chamber is the area where the arc forms when the contacts separate, and it is here that the oil rapidly cools and extinguishes the arc.
Insulating Oil:
The insulating oil plays a dual role: it acts as an arc-quenching medium and provides insulation between the breaker contacts. During the arc formation, the oil breaks down into gas, creating pressure that pushes the arc away from the contacts, ultimately extinguishing it.
Mechanism of Operation
The mechanism of an oil circuit breaker involves the separation of contacts during fault conditions. When the contacts separate, an arc forms between them, and the oil absorbs the arc’s energy, creating gas bubbles and vapor. The rapid cooling of the arc causes the arc to extinguish, breaking the circuit and preventing the flow of fault current.
Working Principle of Oil Circuit Breaker
Arc Formation and Extinguishing Process
When the breaker contacts are closed, current flows through them. During a fault, the contacts open, and an arc forms between them due to the ionization of air. The arc is drawn through the oil, and as it heats up, the oil decomposes into gases, mainly hydrogen and small quantities of methane, ethylene, and acetylene. These gases help to cool the arc and increase the dielectric strength of the gap, which extinguishes the arc and interrupts the fault current.
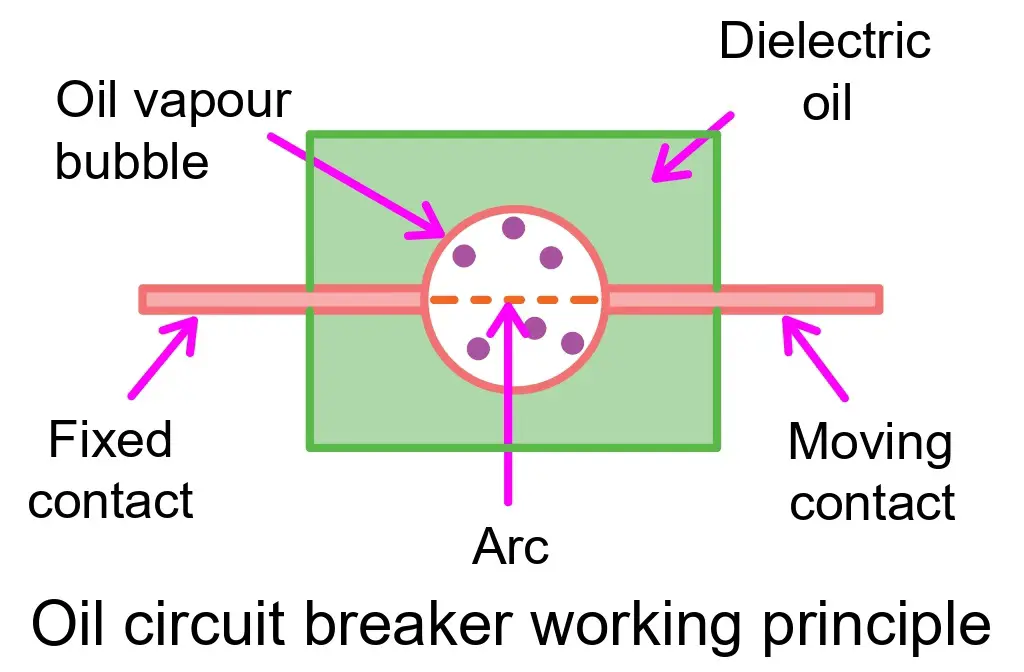
These decomposed gases form a gas bubble surrounding the contacts. When hydrogen gas is broken down into atomic form, it releases heat that heats the arc. This, in turn, increases the vaporization of oil. The volume of gas produced is much greater than the oil decomposed, with the gas bubble rapidly expanding due to high temperatures. Because the gas bubble is enclosed by oil, this puts a lot of pressure on it. As pressure increases, the medium surrounding the contacts starts to de-ionize and rapidly increases the dielectric strength of the medium. The arc is ultimately quenched at the following current zero-crossing.
Besides the cooling effect of the oil, gas bubbles also help in arc quenching.
Types of Oil Circuit Breaker
Based on Tank Design
There are two types of Oil circuit breakers.
Bulk Oil Circuit Breaker(BOCB)
In a Bulk Oil Circuit Breaker, a large volume of oil is used for both arc extinction and insulation. The large tank holds enough oil to provide effective quenching and ensures high dielectric strength. These breakers are reliable for high-voltage systems but have large size due to the need for a significant amount of oil.
There is a classification for BOCB, which can be divided into two types.
- Plain Break Oil Circuit Breaker
- Arc Control Oil Circuit Breaker
Plain Break Oil Circuit Breaker- BOCB has no control over the arc except to increase its length by separating the contacts. They are simple and easy to design.
Arc Control Oil Circuit Breaker- BOCB features a unique arc control system that effectively extinguishes arcs.
Minimum Oil Circuit Breaker(MOCB)
Oil is used as a medium to break the electrical current in circuit breakers. In minimum oil circuit breakers (MOCBs), the interrupting unit is placed in an insulating chamber at the live potential. These breakers are designed to use less oil and are called “minimum oil circuit breakers.” A Minimum Oil Circuit Breaker uses oil only for arc quenching and not for insulation, reducing the oil volume required. The MOCB is more compact and has a smaller tank than the BOCB, making it more practical for modern electrical systems.
Based on the Voltage Rating
Low Voltage Oil Circuit Breakers
These breakers are used in low-voltage systems, typically in industrial or commercial applications where currents are lower, but reliable protection is still required.
High Voltage Oil Circuit Breakers
Used in high-voltage transmission and distribution systems, high-voltage OCB can handle large fault currents, ensuring the safety and stability of the electrical grid.
Advantages and Disadvantages of Oil Circuit Breakers
Advantages
- Effective Arc Quenching: Oil circuit breakers can efficiently handle high-voltage and high-current interruptions.
- Dual Function of Oil: Oil acts both as an insulating medium and an arc-quenching agent.
- Durability: They are known for their long service life and reliability in harsh environments.
Disadvantages
- Maintenance: The oil degrades over time and requires regular testing and replacement.
- Fire Hazard: Due to the use of oil, there is a risk of fire in case of leaks or high-energy arcs.
- Size and Weight: Bulk oil circuit breakers are large and heavy, making installation and transportation challenging.
Applications of Oil Circuit Breakers
Power Generation and Distribution Systems
Oil circuit breakers are commonly used in substations and power stations, where they protect transformers, generators, and other critical infrastructure. They ensure the safe operation of electrical networks by interrupting fault currents.
Industrial Applications
In heavy industries, oil circuit breakers are used to protect large motors and high-voltage equipment from damage due to electrical faults. Their robust design makes them suitable for environments with high power demands.
High Voltage Applications
Oil circuit breakers are particularly effective in high-voltage applications, where large currents need to be interrupted. When the contacts separate under high voltage, the arc formed is intense, but the oil quickly cools the arc and suppresses it. This capability makes OCB suitable for transmission lines, transformers, and substations
Comparison of Oil Circuit Breakers with Other Circuit Breakers
Oil Circuit Breakers vs. SF6 Circuit Breakers
SF6 circuit breakers use sulfur hexafluoride gas for arc quenching, offering better insulation properties, smaller sizes, and lower maintenance requirements than oil circuit breakers.
Oil Circuit Breakers vs. Vacuum Circuit Breakers
Vacuum circuit breakers rely on vacuum as the medium for arc extinction, making them more compact and requiring less maintenance than oil circuit breakers. However, oil circuit breakers are still preferred in certain high-voltage applications.
Maintenance of Oil Circuit Breakers
Oil Quality Testing and Replacement
Regular oil quality testing is crucial for maintaining the performance of oil circuit breakers. Over time, the oil degrades due to arcing and needs to be filtered or replaced to ensure it maintains its insulating properties. The DGA test should be carried out to ensure oil healthiness.
Contact Inspection and Replacement
The contacts in an oil circuit breaker wear out over time due to repeated arcing. Routine inspection and replacement of contacts are necessary to ensure that the breaker operates reliably and safely.
Conclusion
Summary of Oil Circuit Breakers
Oil circuit breakers remain an important tool for ensuring the safety and stability of electrical systems. Their construction and working principles allow them to handle high-voltage faults effectively, making them valuable in various industrial and utility applications.
Future of Oil Circuit Breakers
While alternative technologies like SF6 and vacuum circuit breakers are gaining popularity, oil circuit breakers continue to be relevant in many high-voltage and high-power applications due to their proven performance and reliability.