There are two types of losses that occur in induction motors are- fixed and variable loss. The fixed losses are core loss and mechanical loss, and the variable losses are copper loss and stray loss. In this article, we will discuss in detail the losses in induction motors.
A motor is an electrical machine that converts electrical energy into mechanical energy. Does the electrical energy fully convert into mechanical energy? The answer is -NO. In the energy conversion process, the electrical energy can not be fully converted into mechanical energy because some part of the electrical energy gets wasted in the form of heat energy. The energy wasted in the motor in the form of heat energy contributes to power loss.
The following losses occur in an induction motor.
- Constant or Fixed loss
- Variable Loss
Constant or Fixed Losses in Induction Motor
Constant losses are the losses that remain constant when the motor operates as per its rated parameters. The constant losses can be divided into the following categories.
- Iron or core losses
- Mechanical losses
- Brush friction losses
Iron or Core Losses
Iron losses in an induction motor are the heat loss that gets dissipated in the core of the motor due to the alternating magnetic field created by the stator winding. These losses are also known as core losses or hysteresis losses.
Two types of iron losses occur in an induction motor:
- Hysteresis loss
- Eddy current loss
The magnetic core of an induction motor opposes changes in magnetic field direction and because of hysteresis lag the Hysteresis losses occur in the magnetic core. On the other hand, Eddy current losses occur because the alternating magnetic field induces a voltage in the core, and the induced voltage cause the setting up of circulating current(Eddy current), and this circulating current causes heat loss I2R in the core.
The iron loss does not vary with load, therefore these are the fixed losses. The iron losses remain constant whether the motor is operating at no load or at full load. These losses happen because of magnetic flux and we know, the average magnetic flux remains constant, provided the voltage and frequency are maintained as per the motor’s rated voltage & frequency. The iron losses can be reduced by the use of a high-quality laminated iron core.
Other factors like the shape and size of the core, the design of the rotor and stator slots, and operating temperature also affect the iron losses in the motor. A higher temperature leads to an increase in the core resistance, and consequently, it contributes to higher losses. Therefore, the motor should be adequately cooled to reduce the iron losses as well as the copper losses.
The iron loss can be mathematically calculated by the Steinmetz equation.
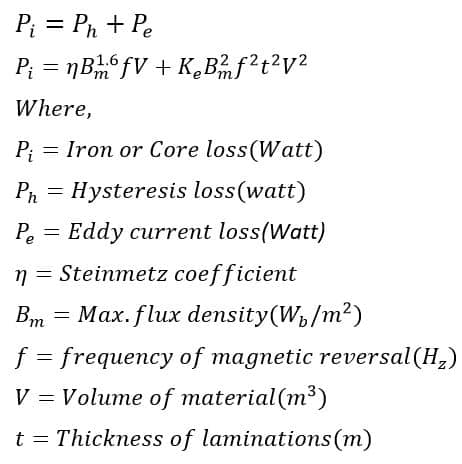
Mechanical Losses
The mechanical losses in an induction motor occur because of two reasons. They are-
- Friction Loss
- Windage Loss
Friction and windage loss are the two types of mechanical losses that occur in an induction motor. The main reason for these losses is the rotation of the motor. The rotating parts like the rotor shaft, fans, and bearing cause mechanical losses in the rotating machine. All the rotating equipment has these types of losses.
The friction and windage losses depend on the speed of the motor, the quality of the bearings, and the design of the motor.
The friction loss occurs because of the rubbing of moving parts of the motor with each other, such as the friction between the rotor shaft and the bearings, friction between the balls and outer cage of the bearing, and friction between the inner and outer cage of the bearing. The motor takes extra power from the mains to overcome this friction loss.
When the motor rotates, it has to cut the surrounding air for its rotation. The air exerts a force on the motor’s components, like the rotor fans. The resistance offered by surrounding air cause windage loss. The windage loss depends on the speed of the motor and the density of the surrounding air.
Mechanical losses are constant losses and they do not vary with load. The mechanical losses can be minimized by the proper design of the rotor and the use of high-quality bearings.
Brush Friction Loss
Squirrel cage induction motors do not have carbon brushes, it’s rotor is internally short-circuited. Therefore, no brush friction loss occurs in this type of motor. However, the slip ring or wound rotor induction motors have slip rings and carbon brushes and the power loss on account of brush friction happens in these types of motors.
Carbon brushes collect the current from the slip ring. The slip ring is a rotating part and the carbon brushes are fixed parts, and there exists friction between the contact surfaces of the carbon brushes and the slip ring. Thus, the brush friction loss occurs in the slip ring induction motor.
Variable Losses in Induction Motor
The losses that vary with load are called variable losses. The major variable loss in an induction motor is copper loss. The followings are the variable losses in an induction motor.
- Copper loss
- Stray loss
Copper Loss
The winding of the induction motor is made of copper that has finite resistance R. When current flow through the stator and rotor winding, the power loss( I2R loss)in the form of heat occurs in the winding is called copper loss.
The copper loss occurs in the stator and rotor of an induction motor. The copper loss in the stator is called stator copper loss, and copper loss in the rotor is called the rotor copper loss. The copper losses depend on the magnitude of the current passing through the stator and rotor, and it is proportional to the square of the magnitude of the current. The copper loss in the induction motor can be calculated using the following formula.
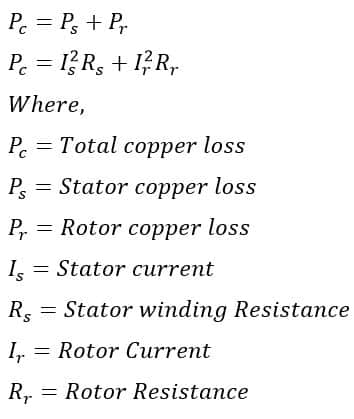
The total copper loss in a 3-phase induction motor is;
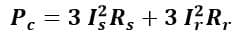
The current of the motor increase with an increase in load, therefore these losses are not constant and vary with load. The copper loss is also called a variable loss. The slip of the induction motor varies with load and losses also vary accordingly. Therefore, the copper loss in the rotor is also called slip power loss. The copper loss can be minimized by selecting a high-quality copper wire for stator and rotor winding.
The resistance of the winding also depends on the temperature. The resistance of the conductor increases with an increase in the temperature. Thus, the operating temperature also contributes to copper loss because copper loss is proportional to the resistance of the winding. Therefore, adequate cooling of the motor is a must for reducing the copper losses in the induction motor.
Stray Loss in induction motor
It is desired that all the generated flux in the stator must be 100% coupled to the rotor and there should be no leakage flux. However, practically the entire flux does not link to the rotor and some parts of the flux leak in the magnetic path. The leakage flux gets linked to other conductive parts of the motor such as the motor frame, bearings, and housing, and creates eddy currents that cause energy loss. Thus, the leakage flux contributes to stray loss in the induction motor. The stray loss is a variable loss, and it depends on the factors like design of the motor, core material, and the load on the motor.
The core of the motor should be of high-quality material in order to minimize the stray loss in the induction motor.