In this article, we will discuss the important points of PLC selection criteria. The PLC is the key equipment for plant automation and the smooth operation of the plant depends on the reliable operation of the PLC.
This article will give information about the important factors that we should keep in mind while selecting the PLC for New Project.
We all have seen many new projects coming in the process plants. The main heart of any project is the control system. Many plants use PLC as a system for controlling the process. So, we definitely have to choose one PLC from the variety of options available. Let us see How to Choose a PLC?
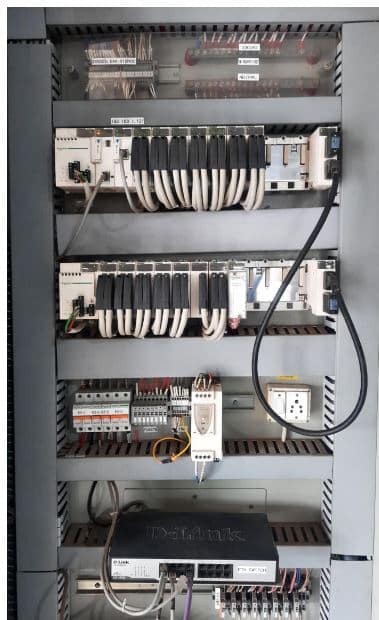
Various Criteria for PLC Selection
We should consider the following criteria for the selection of PLC when choosing PLC.
- Power supply
- Number of Inputs and Outputs
- Communication Protocols
- Surrounding Environment Specifications
- CPU Requirement
- Application Requirements of PLC
- Operator Interface
- Vendor Support
Power Supply
Before choosing a PLC, the first thing which comes to our mind is the power supply to the PLC. PLC can run on 24 VDC, 24 VAC, or 230 VAC depending on the model types. Now the power supply to the PLC is one of the most important factors.
Almost all times field instruments need a 24 VDC power supply. These devices are generally compatible with Input Cards and Output Cards. So having a PLC which runs on 24 VDC is preferable in such a case. From the electrical side, we are already getting 230 VAC.
So, simply an SMPS can be used to give the required power to the PLC. Sometimes there are constraints and we need to use a transformer, so here we need to use a PLC running on an AC power supply. But generally, PLC running on 24 VDC is preferred. Some PLCs also have inbuilt SMPS.
Number of Inputs and Outputs
The number of Inputs (AI, DI) and Outputs(DI, DO) is one of the important criteria for PLC selection. PLC type selection mainly depends on the number of inputs and outputs. PLC types based on the number of inputs and outputs are Nano PLC, Micro PLC, Medium PLC, Large PLC, and Very Large PLC. If the plant has different processes at distant locations, then Remote Input & Output option is also available. Remote IO can also be used to add more modules.
We can always increase the number of IOs in PLC by using expansion modules. Always make sure to have 20% to 30% spare channels in input as well as output. This is because some input or output can fail during the running plant and we need to assign a new channel. Or we can also have a few expansions also based on some MOC.
Communication Protocols
It is obvious that a PLC which is installed needs to communicate with field devices as well as some other systems also. For this reason, we need to know the devices as well as other systems’ communication protocols. The field devices might use HART, Profibus PA, Device Net, or any other communication protocol. So PLC needs to be compatible to communicate with the field devices. Thus, the communication protocol is one of the important criteria for PLC selection.
Also, PLC needs to communicate with a network or other systems also. So Ethernet and MODBUS kind of protocols should also be supported by the PLC. PLC must be able to interface and communicate with all field devices, such as process instruments, VFDs, soft starters, and other plant equipment.
Surrounding Environment Specifications
The plant can be in any location where environmental conditions also vary. So PLC must be designed to withstand the surrounding environmental conditions. The conditions can be high or low temperature and varying humidity. Harsh environment conditions can damage the PLC and can even have an effect on the performance of PLC if the system is not designed well.
CPU Requirement
PLCs are of different types like a Process PLC and Safety PLC. The scan rate of both PLCs also has a great difference. The scan rate totally depends on the CPU of the PLC, and the scan rate of the process needs to be confirmed before ordering the PLC.
The PLC scan rate also becomes one of the important PLC selection criteria when it comes to changing parameters in a process. Suppose a process has a thermal runaway reaction, then here we need to keep an eye on the temperature. So in such cases safety of the plant personnel as well as the process also. So a CPU that takes quick actions is desired here.
Application Requirements of PLC
Some PLCs have libraries where pre-programmed software is stored. If you need some special type of program for your application, and that type of program is already available in the PLC, then we should consider that PLC. As a result, it becomes easy to program the PLC, to serve your specific requirement.
Operator Interface
The plant operator needs to run different processes or machines from one place, then for such cases, a graphical display is needed. For such Human Machine Interface (HMI) becomes a difficult choice. This is because in such cases an operator has to go to roam around the place for controlling different processes or machines.
One best example supposes a plant has 10 different compressors and each compressor has a dedicated PLC. In such a case, there will be 10 different HMI. So for an operator to control all these 10 compressors through 10 different HMI at different locations will be very difficult. Therefore, the operator interface is one of the important PLC selection criteria.
Vendor Support
The last but most important factor is vendor support. If you installed a PLC and then encountered a problem that cannot be solved by plant engineers then in this situation, PLC vendor support is a must. The vendor must be having a large customer base, a strong team to troubleshoot in case of problems, and be easy to communicate with. Past experience of vendors helps a lot in deciding on a proper vendor.