A hot wire anemometer is a thermal transducer widely used to measure instantaneous flow velocity. The hot wire’s cooling rate causes a change in the resistance, which measures the flow of air or wind.
An anemometer is an instrument used for the measurement of moving fluids, particularly wind or air, by heated wire. An anemometer is used for air in a duct or unconfined flows, such as an atmospheric wind.
The anemometer is derived from the Greek word anemos “wind” metro “measure.”
There are several types of hot wire anemometers, each with its own design and application.
Choosing the right type of hot wire anemometer type depends on factors such as specific application, the range of velocities to be measured, environmental conditions, and the level of precision required for the measurement.
Table of Contents
The article discusses the principle of and its types.
Hot Wire Anemometer Principle
An Anemometer is a thermal transducer. The principle of a hot-wire anemometer is that “the heat transfer from a fine filament which is exposed to a cross-flow varies with variation in the flow rate”. In other words, the rate of heat loss from a wire heated electrically and placed in an air steam is proportional to the stream velocity.
Types of Hot Wire Anemometer
- Constant Current Anemometer (CCA)
- Constant Temperature Anemometer (CTA)
An anemometer’s electronic circuits and measurement systems process and analyze the electrical signals that sensors and transducers generate. The systems may include amplifiers, filters, analog-digital (ADC) converters, and microcontrollers. Its main function is to convert electrical signals into wind speed and direction values.
Constant Temperature Anemometer (CTA)
The operating principle of constant temperature anemometers (CTA) is based on the fact that the sensor current undergoes variations according to the flow speed to maintain its resistance at a constant temperature.
These anemometers use a control loop that keeps the temperature difference between the superheated element and the flow constant. The power consumed to keep the superheated sensor at a constant temperature is proportional to the airflow velocity.
In this type of hot wire anemometer, the wire’s temperature is maintained at a constant level as the fluid flows past it. The electrical current required to maintain this constant temperature used to calculate the fluid velocity CTA is widely used for low to medium velocity measurements.
Construction and Operation
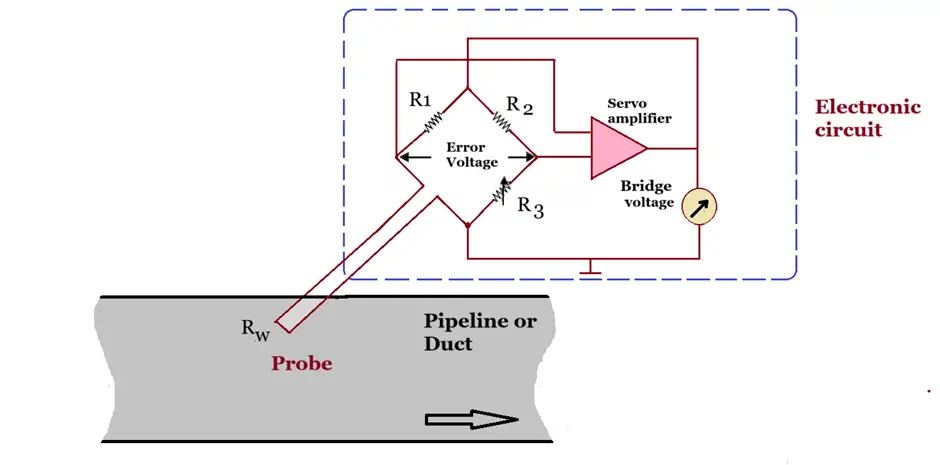
The instrument is composed of a small sensor and a controller or feedback circuit. A controlled electrical current is imposed on this filament, and the heat generated (by the Joule effect) is exposed to the flow.
The electrical circuit used to evaluate variations in electrical resistance is the so-called Wheatstone bridge. It is composed of four electrical resistances, two of which are fixed; one is a reference, and the other is the resistance of the sensing element (Rw), shown in the figure above.
The Wheatstone Bridge operates with a constant overheating resistance, the value of which is calculated by the bridge itself.
The feedback circuit is responsible for producing the current necessary to balance the Wheatstone bridge through an increase in the resistance of the sensor. This occurs because the filament (wire) has a positive temperature coefficient of resistance, which means that when the temperature of the filament varies, so does the value of its resistance.
Under operating conditions, the feedback circuit applies an electric current to the Wheatstone bridge, thus promoting an increase in the temperature and resistance of the hot wire up to a predetermined value, which is generally around 250°C. In this equilibrium condition, the bridge is said to be balanced. ,
A small increase in fluid velocity causes cooling of the hot wire anemometer sensor, decreasing its resistance and consequently unbalancing the Wheatstone bridge. This causes the feedback circuit to increase the current fed to the bridge, heating the sensor to bring the bridge back to equilibrium condition.
As the circuit’s response is very fast, the sensor’s temperature remains virtually constant during the variation of the flow speed. Then, the voltage difference between the ends of the bridge is proportional to the measured speed.
Constant Current Anemometer (CCA)
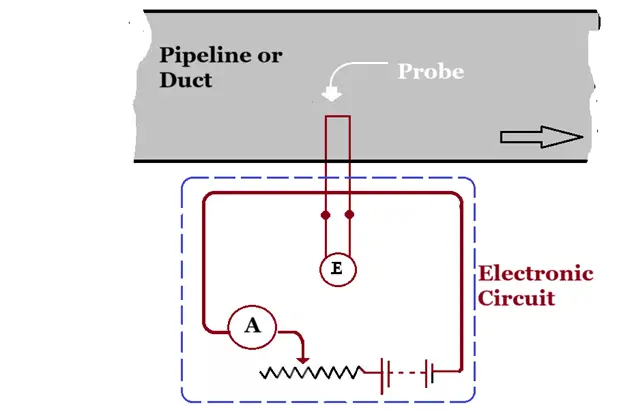
The constant current anemometer (CCA) is suitable for a wide range of flow velocities.
Instead of maintaining a constant temperature, CCA hot wire anemometer keeps the electrical current through the wire constant. Changes in the fluid velocity cause variation in the wire’s temperature, which is then used to determine velocity.
The above figure shows the general electronic diagram of the current method constant source (CCA), which is composed of a constant source of the sensor and a high ohm resistance. These components are placed as shown, forming a series circuit between them.
In this form, we have a constant current. Since the variation of the resistance of the sensor compared to the fixed high-ohm resistance is minimal, and therefore, since the current does not change, the circuit is governed by the large resistance value that has been placed.
Sensors and Models
There are 3 models of probes used in wire anemometry systems
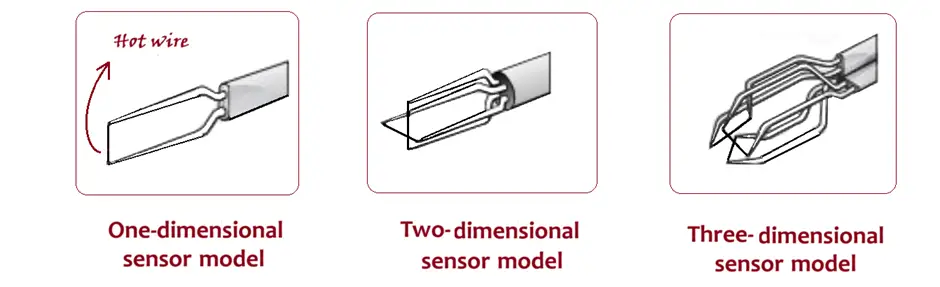
- One-dimensional sensor model
- Two-dimensional sensor model
- Three-dimensional sensor model
One-dimensional has a single filament between the base teeth to perform fluid turbulence measurements in only sense. In the two-dimensional ones, an additional filament is added. Three-dimensional are responsible for performing flow measurements in a more advanced way.
Interface and data visualization
The interface and data display on the anemometers allows the user to read and understand the wind speed and direction measurement easily.
Applications of Hot Wire Anemometer
- Its size is very small, therefore very easy to use.
- Hot wire anemometers are highly sensitive to rapid changes in speed.
- Frequency response characteristics are good compared to any other wind speed measuring system.
- Hot wire anemometers are used for environmental monitoring purposes.
- In research applications.
- In the aviation field.
- In industrial processes, where accurate measurement of fluid velocities is necessary.