In this article, we will discuss the insights of feedforward Vs feedback control systems. The control loops are an integral part of a control system. The PID controller is used for controlling a closed loop system of temperature or pressure or flow or level. This PID controller is used in a control loop which may be feedback or cascade loop. Most of us get confused between the feedback control and the feedforward control loop. Now, we will discuss both the control loops and the significant differences between them.
Feedback Control
Feedback control is most widely used in plants for controlling a closed-loop system. In the feedback control loop, the measured output of the process is compared with the set point and an error is generated. The error is given to the controller which generates a manipulated variable to control the process. The measured output is measured by the feedback sensing element. In a feedback control system, the feedback element provides feedback after the disturbance has affected the process. Hence, the process always gets affected by the disturbance and responds later on.
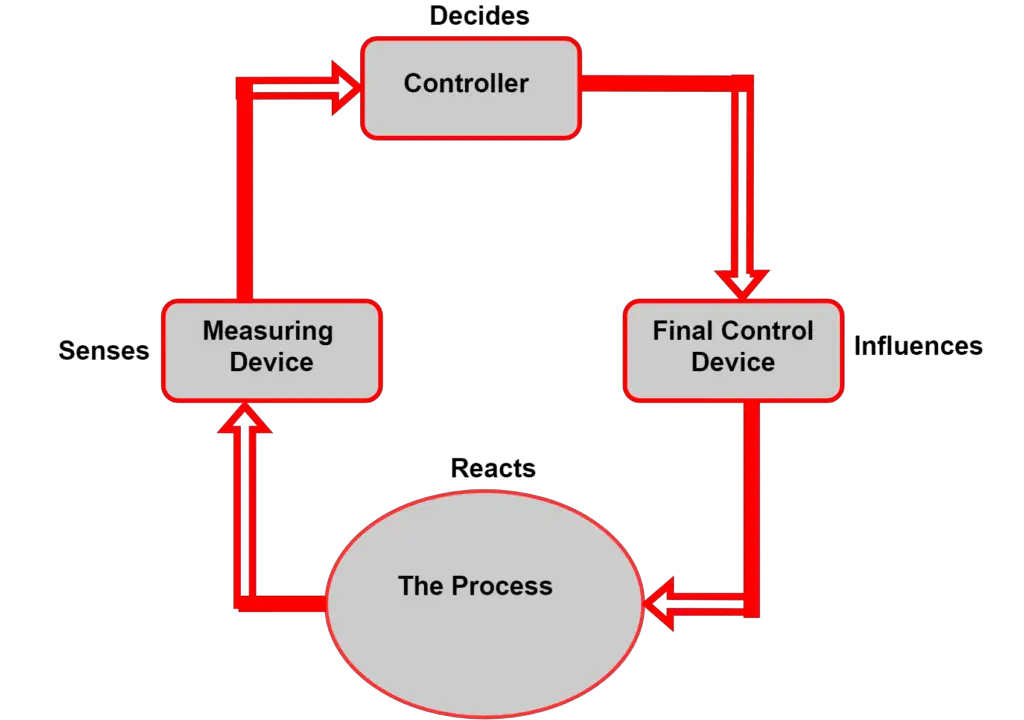
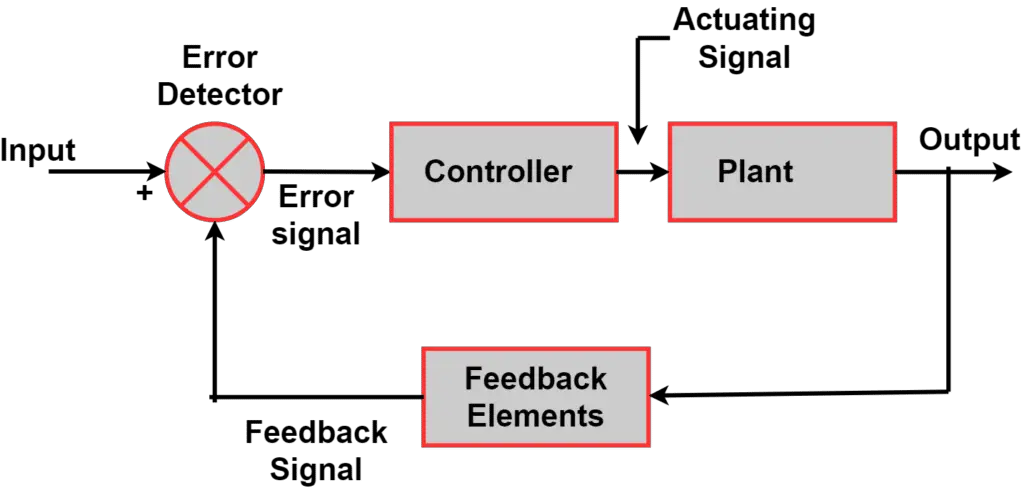
Examples of Feedback Control System
1. Temperature Control System
Suppose there is a system whose temperature control is needed (an electric oven in our case). So here a temperature sensor is needed as a feedback element. A temperature controller is also needed to control the power controller supplying power to the heater. Suppose, the temperature setpoint to the control system is 245 °C.
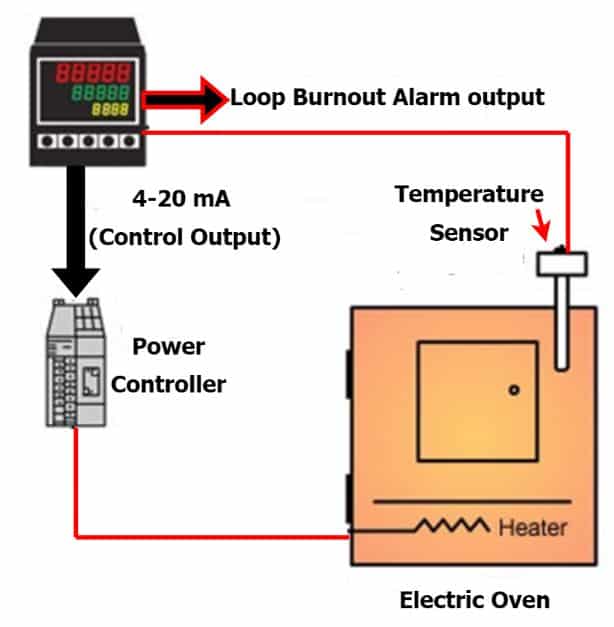
So, when the temperature is less than the set point, i.e. 245 °C, the heating will increase. Now when the temperature goes above 245°C, the heating will decrease but the temperature has gone above 245 °C. Similarly, when the heating is decreased, the temperature will go below 245 °C and again start increasing. So, a kind of oscillation will be seen which keeps affecting the process. No doubt these oscillations can be decreased by tuning the controller but it will definitely affect the process and control it only after the process is affected. This is a major disadvantage of the feedback control system.
2. Boiler drum level control System
A level transmitter continuously measures the level of the boiler drum. The level controlling is done by using a level control valve which controls the boiler feed water.

When the level goes below the set point, the level control valve opens and when the level increases above the set point, the level control valve closes. The disturbance is due to the steam demand downstream. Because of the changing steam demand downstream, the level keeps on changing.
Advantages of feedback control system
- As soon as the controlled variable deviates from the set point, the control action is taken by the system regardless of the source of the disturbance and the type of the disturbance.
- The feedback control loop is very simple when it comes to implementing the feedback control loop. Complex things like mathematical modeling are not required.
- When the PID controller is used in the feedback control loop, most of the system’s response is satisfactory.
Disadvantages of the feedback control system
- The feedback control loop does not take any action until any deviation in the output is not observed. Hence every time, the process gets affected by the disturbance and then the disturbance is eliminated by the feedback control loop.
- The feedback control loop does not provide predictive control for repetitive disturbances too.
- If the process has large time constants or a large time delay, then the output of the system will deviate from the set point for a longer period of time, and sometimes it may not achieve a steady state too.
- In some situations where the controlled variable cannot be measured, the feedback control loop cannot be implemented.
Feedforward Control
The feedforward control is used where there is a continuous change in the disturbance and the system’s output control is very important. In the feedforward control system, the controller senses the disturbance before this disturbance affects the process. Change in input or output for the process is done accordingly so that the process does not get much effect from the disturbance. This way the feedforward control system nullifies the effect of the disturbance. But as there is no feedback from the process. The control loop never knows whether the process working as per requirement or not.
Example of feedforward control system
Boiler Drum Level Control
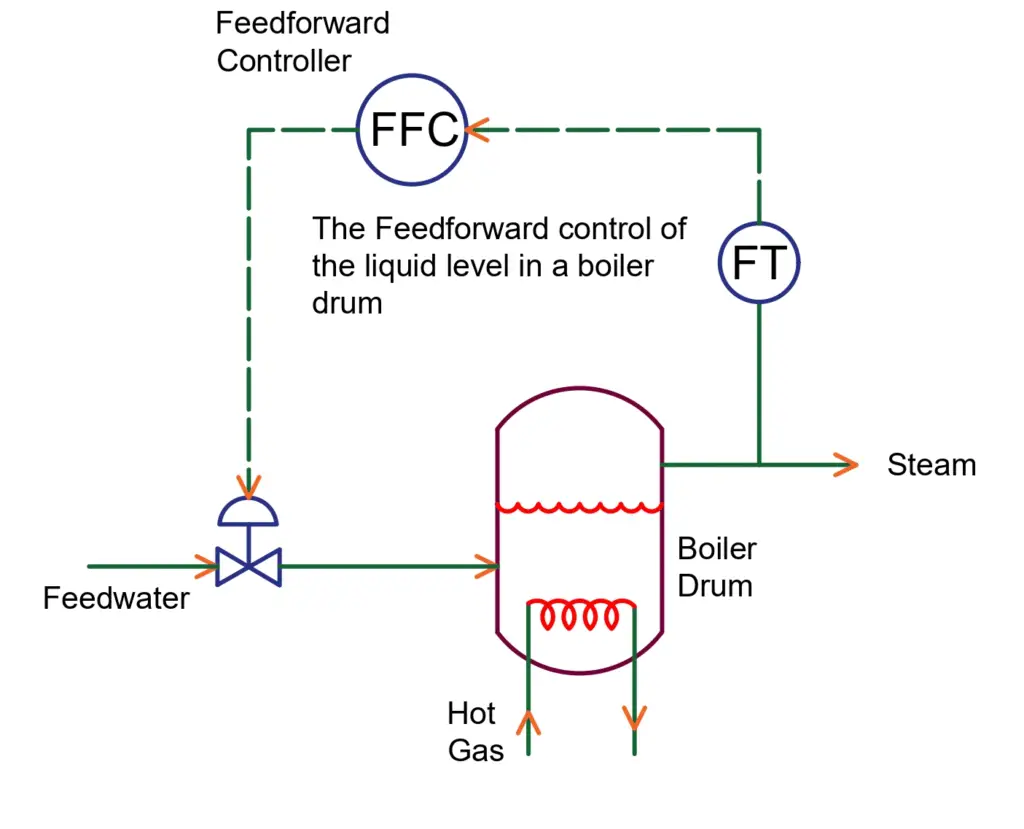
As seen in the figure, a flow transmitter measures the steam flow which is the disturbance to the level. As soon as the demand for steam changes, the Feedforward controller changes the boiler feedwater accordingly. This compensates for the change in a level before there is an actual change in the level. But in this case, there is no feedback on whether the level is ok or not as per the set point.
Advantages of feedforward control system
- The feedforward control system measures the disturbance before it affects the process and takes necessary action.
Disadvantages of feedforward control system
- To measure the disturbance before it affects the process is a bit difficult and not feasible in some cases.
- Perfect modeling of the control system is needed to implement the feedforward control system.
- As time passes, the system’s response also changes. So, the feedforward system fails because of the changed response of the process.