The feedback control system is a very important control philosophy for controlling the process accurately and precisely. In all industries, to get required output, many types of closed loop configurations are used. If the accuracy in the output is not required, then open loop control system can be used without any second thought. But for accurate outputs, closed loop control systems are used. Feedback control system is one of the most widely used closed loop configurations used in almost every industry.
What is a feedback control?
The feedback control system produces an output, and then senses the output which is fed back as a feedback to the controller. The feedback is an electric signal that is transferred from the output to the controller. Thus, the controller is able to calculate how the output is different from the required value.
The controller will get to know the past state of the output of the system by the help of the feedback signal. The controller calculates the error and may vary the system input to get the required output.
The feedback control system is also known as the closed loop control system. This is because the output is fed back as an input to the controller, so that the errors can be cleared and the output quality is maintained. The feedback control eliminates the measured disturbances.
The feedback controls are automated and must do the sensing; calculation and manipulation are to be performed by the equipment. Each element should communicate with other elements in the control system.
Characteristics of Feedback Control System
The feedback control system has the following characteristics:
- It has a good accuracy.
- The system has a slight oscillation and hence is somewhat instable.
- The non-linear effects are reduced.
- The effects of external disturbances or noise are possible to reduce .
- The system improves the quality of product by better control.
- The response to the variation in input is high in a feedback control system.
Feedback Control System
The system has five components:
- Input (known as set value)
- Output (known as process variable)
- Process being controlled
- Sensing devices
- Actuating / control devices
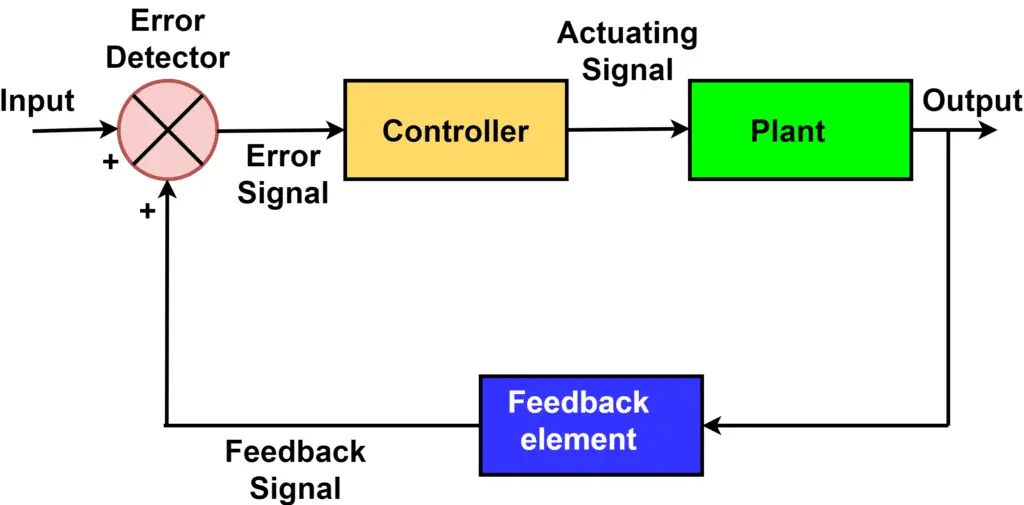
Let us understand the feedback control system by a simple air conditioning system. In an air conditioning system, the above parameters can be defined as:
- Input is temperature set point set by the remote controller
- Output is temperature
- Process being controlled is temperature in the room
- Sensing device is the temperature sensor
- Control device is the AC
In the air conditioning system, say the temperature in the AC is set at 28°C. But when we start the AC, at that time the temperature of the room is high. This temperature is measured by a temperature sensor. Let us assume it to be 34°C. Now, based on this feedback signal, the controller inside will start the compressor. Then the controller will try to bring the temperature lower till it reaches the set point. By this time, the sensor will continuously give its feedback to the controller. If the current temperature reaches the set point, the system will turn off.
Based upon the turning off condition, there can be two cases- temperature may increase or the temperature may continue to decrease.
In the first case, where the temperature is found to be increasing, the control system would turn on and bring the temperature down.
In the second case, where the temperature is decreasing, the control system will not take any action until the temperature increases again.
The calculation is based on two main factors. They are required value and current value. The difference between these two values is called error.
Error= Required Value – Current Value
Based upon this error, the controller will decide how to manipulate the controlling device would try to bring down the error to zero after a certain stage. The feedback system works on this principle. It works on the real-time calculation.
Example of a feedback control system is PID (Proportional Integral Derivative) controller. It controls a process either by digital output or analog output. An example of digital output is n air conditioning system mentioned above. An example of analog output is an actuator valve or VFD.
Types of Feedback
There are two types of feedback available for a feedback control system. They are:
Positive feedback
In the positive feedback type, the feedback signal is added with the input signal in the controller. A positive feedback type control system is rarely used, because of its less control over the error.
Negative Feedback
In the negative feedback type, the feedback signal is subtracted from the input signal in the controller. A negative feedback type control system is generally used because it has great accuracy and control in the process. The example of air conditioning system discussed above has a negative feedback. In the negative feedback type, the controller decreases the error by bringing the output near to the input.
Advantages of Feedback Control System
The feedback control systems have the following advantages.
- There is reduction of non-linear effects that are most often seen in open-loop systems.(open loop system means a system that does not have any feedback)
- Reduction in noise and disturbance.
- Improved efficiency, accuracy and quality
- Improved system stability and process certainty
- Improved gain and bandwidth
Disadvantages of Feedback Control System
The feedback control systems have the following disadvantages:
- The feedback system makes the system complicated by increasing the number of components like sensors and error detectors.
- In feedback system the overall gain of the system is reduced and must be compensated in the design.
- If feedback system is not configured properly, then the system will produce oscillating outputs which will make the system more unstable.
- If some unmeasurable disturbances affect the system, then the feedback control system takes time to produce desired output in such condition.
- The feedback control system is a type of lagging control system, which means that it will take some time to produce accurate outputs.