The factors like temperature, alloying, cold work, age hardening & mechanical stress affect the resistivity of electrical materials. In this post, we will discuss the factors in detail that affects the resistivity of electrical material.
Factors Affect the Resistivity
Temperature
How does temperature affects the resistivity?
In a metal, the electron moves randomly inside the metal. The degree of randomness in the movement affects the resistance of the conductor. The increase in temperature causes an increase in electrons speed. Thus, with an increase in the temperature, the collision between one electron to other electrons and atom increases. This phenomenon cause increase in the resistance of the conductor. Thus, with an increase in temperature, the resistivity of the conductor increases.
The formula of resistivity with increased temperature is given below.
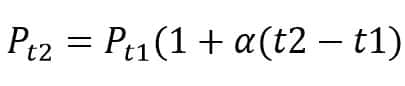
Where,
Pt1 = Resistivity at temperature t1
Pt2 = Resistivity at temperature t2
α = Temperature Coefficient of resistance
The resistivity of the metals increases with the temperature increase. Thus, the metals have a positive temperature coefficient. The resistivity of the insulators & the semiconductors decreases with an increase in temperature. Therefore, these materials have a negative temperature coefficient.
Alloying
What is an alloy? The process of combining metal with other substances to create a new metal is called allying. The alloying of metal is done to have some better mechanical % electrical properties as per the application requirement.
The atomic structure of the metal is regular as compared to the solid solution. A small content of impurity added to the metal may drastically increase the resistivity. It is not necessary that the impurity has high resistivity, even low resistivity impurity may cause a drastic increase in the resistivity of the base metal. Silver has the least resistivity among all the metals & when added to copper it increases the resistivity of the copper drastically.
The examples of alloys used for the electrical application are ALNICO, steel, Brass & solder wire.
Mechanical Stressing
localized strain develops in the metal on the application of the stress of the material. This localized strain disturbs the crystal structure of the metal and creates a hindrance to electron or current flow. As a result, the resistivity of the material increases.
Subsequently, to remove the strain annealing process ( Heat treatment process) is done. The annealing removes the mechanical strain & reduces the resistivity of the metal. The resistivity of the annealed copper is less than the resistivity of hard-drawn copper.
Age Hardening
Age hardening is the heat treatment technique. By the age-hardening process, we can increase the hardness of the alloy. The increased hardness leads to increased yield strength. As a result, the alloy resists permanent deformation by an external force.
We also call age-hardening “Precipitation Hardening”. The disadvantage of age hardening is that this process creates solid impurities or precipitates. Further, The solid impurities in the metal disturb the crystal structure of the metal. The disturbed crystal structure causes hindrance to the flow of electrons or current. Thus, the age-hardening causes change in the metal resistivity.
Cold Working
Cold working is a part of the manufacturing process. This process increases the mechanical strength of the metal through plastic deformation. The cold working disturbs the crystal structure of the metal. The disturbed crystal structure of metal interfaces with the movement of electrons in the metal and creates a hindrance for electron flow. As a result, the resistivity of the metal increase after performing cold working on metal. The cold working is also known as “work hardening” and “strain hardening”.
Read Next: