This article describes the electric drive block diagram, types, and applications. B.S. Iakobi in 1838 developed the first electric drive for propelling a boat by use of a DC battery in a DC motor. The speed of an induction motor can be precisely controlled by varying the voltage and frequency simultaneously. The drive used to control the speed of the induction motor is called the VF drive.
Thus, an electric drive is very important for controlling the speed of the motor for process optimization coupled with energy saving as well.
What is an Electric Drive?
When we think to control the speed of a motor, the first name that comes to our mind is electric drive. An electric drive is a system that controls the speed of an electrical machine. The drive has a prime mover like a petrol engine, diesel engine, steam turbine, hydraulic motor, electric motor, gas or steam turbine. The prime mover supplies energy to drive for controlling the motion.
An electric drive controls the speed of the motor. An electric drive can be a VF drive or a DC drive, depending on the applications.
Block Diagram of Electric Drive
The block diagram of an electric drive is shown below.
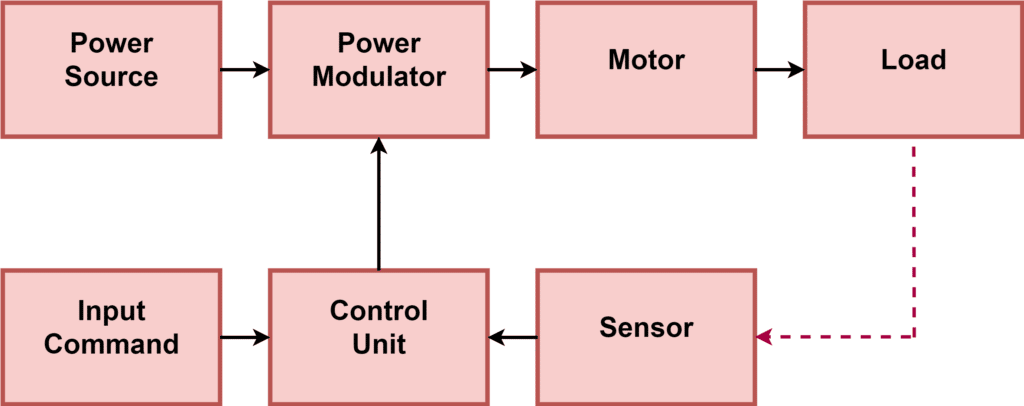
The electric drive has a source, power modulator, motor, load, sensing unit, control unit, and input command.
Power Source
The power source provides the necessary energy for the system. The converter converts the energy source into variable voltage and frequency as per the motor’s control philosophy.
Power Modulator
The power modulator controls the output voltage and frequency to control the speed of a motor. The power modulator outputs the voltage and frequency to the motor that controls the speed of a motor. The power modulator provides the features like starting torque boost, ramp-up start and ramp-down stop, etc.
The drawn current from the power source may excess it otherwise can cause a voltage drop. Therefore the power modulator limits the motor current as well as the source.
The power modulator has the capability to change the energy based on the motor requirement. For example, the inverter converts direct current into alternating current to operate an induction motor. Moreover, the modulator has the capability to drive a motor in braking modes as well. Hence the power modulator controls the source voltage and motor current. If the source is DC and we need to drive an induction motor, then the power modulator converts DC into AC.
Load
The load connected with the electric drive may be an inverter, converter, motor, or any kind of mechanical load, such as a Pump, Fan, or Machine tools. The load characteristics may be of constant and variable torque.
Control Unit
The control unit controls the power modulator, which can operate at power levels and small voltage. The control unit receives input commands and feedback from the motor and gives its output to the power modulator. And, the power modulator further controls the motor speed.
Sensing Unit
The sensing unit senses the motor speed and current and feedbacks the signal to the control unit of the drive system. The sensing unit forms a closed-loop system for precise motor speed control. Examples of sensors are speed sensors and current sensors.
Motor
The electric motor drives the mechanical load. The motor can be of DC or AC type. The controller of the motor is selected according to the kind of motor.
Commonly used motors are as follows.
- DC motors – series, shunt/parallel DC motor, compound, and permanent magnet DC motor.
- Induction motors – squirrel cage and slip ring induction motor
- Brushless dc motors or BLDC motors
- Stepper motors.
Types of Electrical Drive
The drives are classified into three types: group drive, individual drive, and multi-motor drive. Additionally, we can classify the electrical drives as follows.
On the basis of supply
- AC Drives– AC drive controls the speed of an induction motor by changing the frequency of the electrical supply to the motor. AC drive is also known as variable frequency drive(VFD) or variable speed drive(VSD).
- DC Drives– DC drives control the speed of DC motors by changing the voltage at the motor’s armature. There are two types of DC drives- Analog DC drives and digital DC drives.
On the basis of Speed
- Constant Speed drives-In the machine tools applications, there is a need for constant speed. To achieve this feature, a squirrel cage induction motor is preferred with manual controls.
- Variable speed drives- In some process control, it is desirable to have a speed control for process optimization and energy saving. For these applications, variable speed drives are used.
On the basis of the Control Parameter
- Constant torque drives– Some loads demand constant torque in the entire speed range. The drive supplies the constant torque to the load. In variable frequency drive, the constant torque is maintained by keeping the volt/Hz ratio constant. Examples are screw compressors and belt conveyors.
- Variable torque drives– The variable torque drives deliver the variable torque as per the torque requirement of the load. The Variable frequency drive can be programmed to run in constant torque or variable torque mode.
- Constant power drives- When a drive is operated above its base speed, it operates in a constant power mode. The speed increase is done through the flux weakening technique. Therefore, the torque reduces with an increase in the speed. Thus, the drive operates in constant power mode.
- Vector control drives- In VFD, vector control provides more accurate speed control than scalar control. In vector control, the speed and torque are simultaneously controlled to achieve the best performance of the drive. This method is widely used in induction motors & AC synchronous motors.
On the basis of a Number of Motors
- Single motor drives– There is a single motor for a particular application. Example-Lathe Machine
- Multi-motor drives– There are separate motors for motoring the different parts of a machine. Example- EOT crane
- Group drives-One motor drives two or several machines. The other machines are connected to the motor’s shaft through belts and pulleys. Coupling is made through clutch arrangement.
Advantages of Electrical Drives
The followings are the advantages of the use of electrical drives.
- Electric drives are eco-friendly because they do not produce smoke, fumes, ash, etc. As a result, electric drives are most suitable for underground railways.
- Electric drives have versatility in their operation—the electric drives use electronic devices like SCR, IGBTs, MOSFETs, and microcontrollers, therefore the drive can be easily controlled and their performance is superior.
- Electric drives can be controlled from remote locations.
- Electric drives occupy significantly less space because they are compact in size.
- Electric drives can control the torque, speed, and power in a wide range.
- Electric drives instantly start the motor because they do not need warm-up time.
- Electric drives are very reliable.
- Electric drives can be operated in different environmental conditions, such as chemical, mining, explosive, and radioactive environments.
- Electrical drives which are powered by electrical energy have numerous advantages over other sources of energy.
- Electric drives need less terminal space because they have high scheduled speed and high traffic handling capacity.
- The electrical drives are the most economical because they require less maintenance and less maintenance time.
Disadvantages of Electric Drive
The followings are the disadvantages of using electric drives.
- They are costly.
- Can not be installed where electric power source not available
- Electric drives produce harmonics and pollute the electrical power network,
- They produce electronic noise.
- Electric drives are only suitable for electrified tracks.
- The control circuit is complex
- The dynamic response of an electric drive is poor.
- In the event of power failure, electrical drives can not work.
- The output power obtained from an electric drive is low.
Applications of Electrical Drives
Electrical drives are widely used in the following applications.
- Electric Traction– Electric trains, trams, buses, trolleys, and solar-powered vehicles inbuilt with batteries are the different types of electric tractions used for the transportation of materials from one location to another location. For these applications, electrical drives are widely used.
- Electrical drives are widely used the domestic and industrial applications, such as motors, cement plants, steel plants, factories, rolling mills, machine tools, Paper mills, transportation systems, textile mills, pumps, fans, robots, etc.
- The electrical drive is the preferred choice as the primary mover for petrol or diesel engines.