The stepper and servo motors are widely used in industry. When properly selected for a particular application, both stepper and servo motors provide effective, reliable operation.
Stepper Motors:
Stepper motors are also known as step motor or stepping motor. This type of motor is a brushless DC electric motors that continuously divides a full rotation into a number of equal steps.
There are three types of stepper motors. They are-
- Permanent magnet (PM) stepper Motor
- Variable reluctance (VR) stepper Motor
- Hybrid synchronous stepper Motor
(1) Permanent magnet (PM) stepper Motor
Permanent magnet stepper motor use a permanent magnet (PM) in the rotor and operate on the attraction or repulsion between the rotor PM and the stator electromagnets.
(2) Variable reluctance (VR) stepper Motor
Variable reluctance stepper motors have a plain iron rotor and operate based on the principle that minimum reluctance occurs with minimum gap. Hence, the rotor points are attracted towards the stator magnet poles due to discussed phenomenon.
(3) Hybrid synchronous stepper Motor
Hybrid synchronous stepper motor are a combination of the permanent magnet and variable reluctance type stepper motors. They maximize power in a small size.
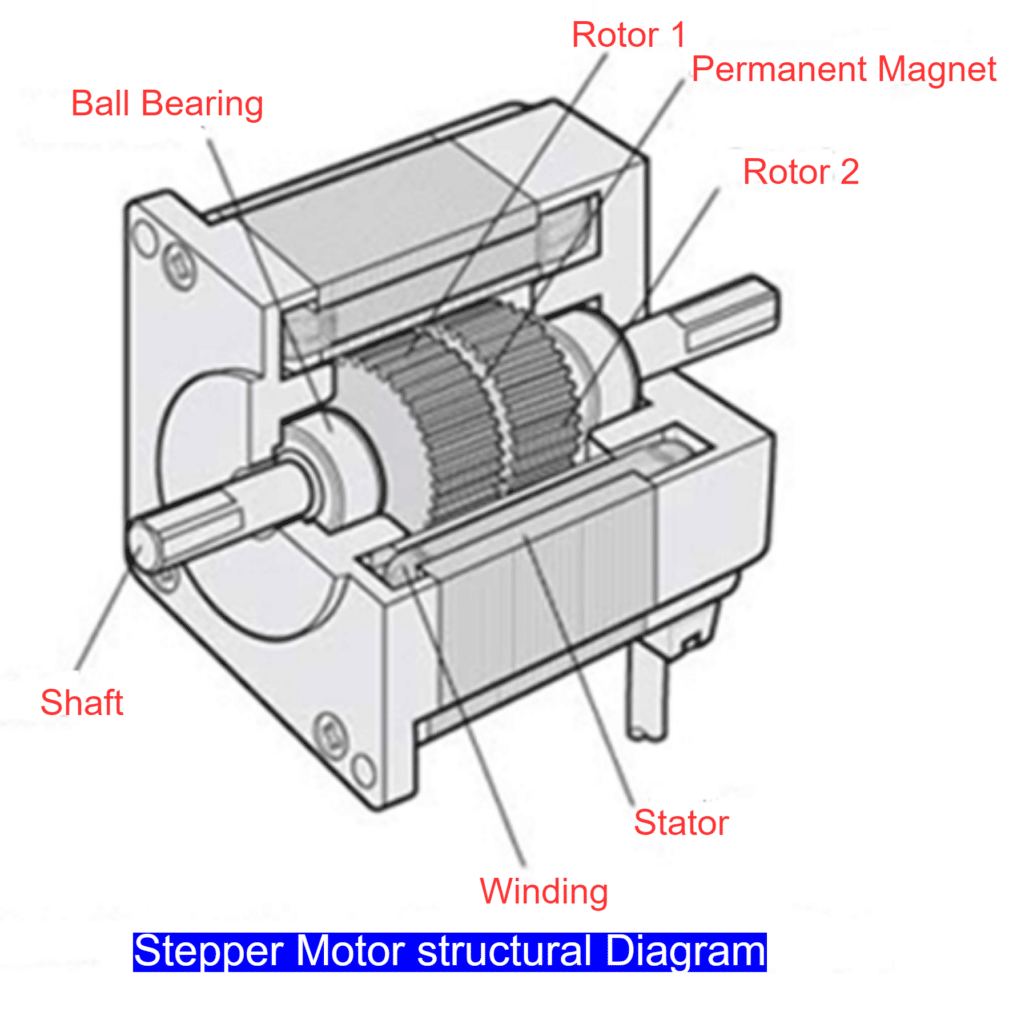
Stepper motors have the inherent ability to control position, as they have built-in output steps. This feature of stepper motor is used for an open-loop position control operation, without any feedback encoder.
The stepper motor’s drive signal specifies the number of steps of movement to rotate. But for this purpose, the controller needs to know the position of the stepper motor on power up condition. Therefore, during the first power up, the controller will have to activate the stepper motor and turn it to a known position (for example until it activates an end limit switch), like in an ink jet printer- the printer will check for left and right limits.
The lack of feedback of a stepper motor limits its performance, because the stepper motor can only drive a load that is within its capacity, otherwise the missed steps under the load may lead to the positioning errors and the system may have to be restarted or recalibrated again.
The stepper motor are used for precise positioning, such as for hard disk drives, movement in robotics, in antennas, in telescopes, and for some toys. In industries, stepper motors are widely used for automation in plants and also used in manufacturing/process control.
Servo Motors
A servo motor is a rotary actuator or linear actuator kind of device. Servo motor provides a precise control of angular or linear position, velocity and acceleration. Servo motor can be coupled to a sensor for position feedback. It also requires a relatively sophisticated controller. Generally, a dedicated module is designed specifically for use with servomotors.
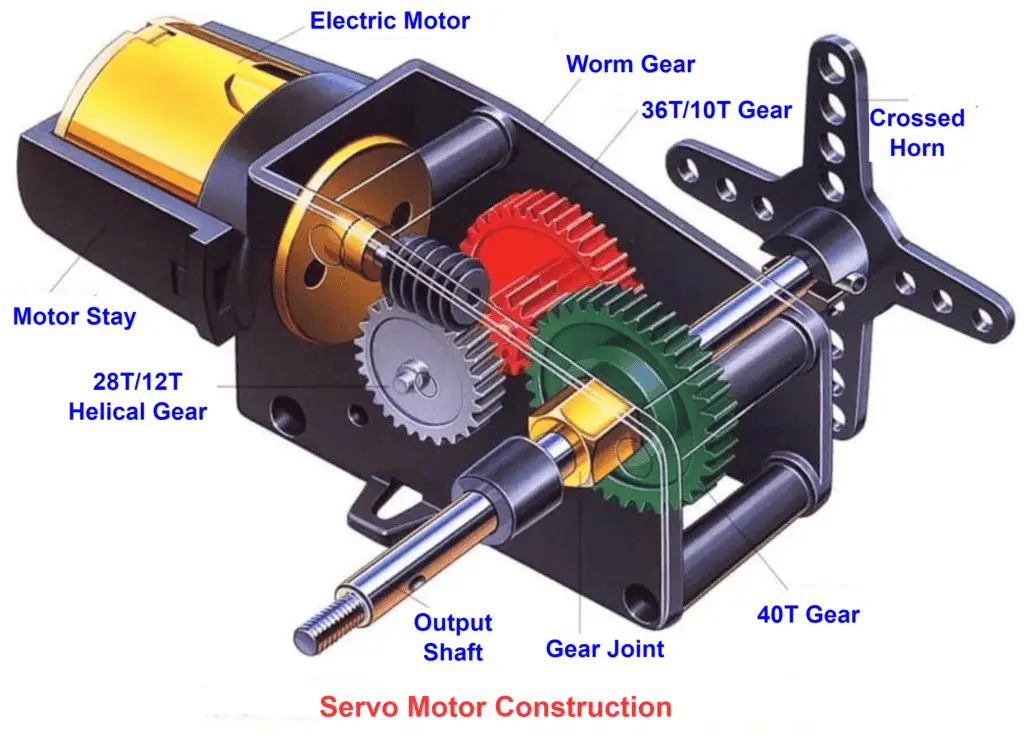
Servo motors are not a specific class of motors. The term servo motor is often used to refer to a motor which is suitable for use in a closed-loop control system. Servo motors are used in applications such as robotics, CNC machinery and automated manufacturing.
The encoder and the controller of a servomotor are an additional cost. But the encoder and the controller optimise the performance of the overall system (for all of speed, power and accuracy) in relation to the capacity of the basic motor.
Servomotors have the advantage in larger systems, where a powerful motor represents an increasing proportion of the system cost. Servomotors are usually used as a high performance alternative to the stepper motor.
Servo motors are widely used in robotics, cameras, for opening and closing of automated doors, vehicles, solar tracking, milling application and in textile production field.
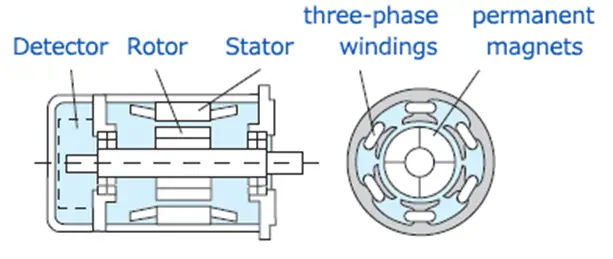
Key Difference Between Stepper and Servo Motors:
Stepper Motor | Servo Motor |
Stepper motor is used in open-loop. | Servo motor is used in closed-loop. |
Stepper motor does not have feedback system, so, chances of error are higher. | Servo motor has feedback system, so, chances of error are less. |
Stepper motor are small in size. | Servo motor are bigger in size as compared to stepper motors. |
Stepper motor provide high amount of torque at low speeds. | Servo motor provide lesser torque as compared to stepper motors. |
Stepper motor provide very low torque at higher speeds. | Servo motors provide very high torque at higher speeds. |
In stepper motor there is no need if an encoder. | Servo motor require an encoder and a gearbox for more accurate control. |
The speed of stepper motors is less than that of servo motors. | The speed of servo motors is higher than that of the stepper motors. |
At standstill position, there will be no vibration or pulsation in the stepper motors. | In servo motors, pulsation or vibration is seen at standstill position. |
Stepper motors are less costly as compared to the servo motors. | Servo motors are costly as compared to the stepper motors. |
Stepper motor have a high pole count, which is generally between 50 and 100. | Servo motor have a low pole count, which is generally between 4 and 12. |
Stepper motor’s system is mechanically simpler. | Servo motor’s system is mechanically complex. |