This article describes the concept of commutation in DC machines, including DC generators and motors. Learn how it works, its importance, types, and methods to improve commutation for efficient operation.
What is commutation in a DC machine?
The armature winding of a DC generator generates an alternating voltage because it experiences a rotating magnetic field. Commutation in a DC machine, in the case of a DC generator– is the process of converting this alternating current into direct current with the use of a commutator and stationary brushes, and in the case of a DC motor– commutation is the process of converting the input direct current into alternating current AC in the armature with the use of a commutator and stationary brushes.
In a DC machine, the transfer of current from the rotating armature to the stationary brushes requires a continuous moving connection between the commutator segments and the brushes. With the rotation of the armature, the coils under one magnetic pole (such as the north pole) go between a positive and a negative brush. During this process, current flows through these coils to the commutator segments.
Then the coil gets short-circuited for a short duration of about 1/500 the of a second. The duration for which the coil remains short-circuited is known as the commutation period. After commutation, the armature coil rotates under the south(S) pole and moves between a negative brush and the next positive brush. During this rotation, the direction of the current reverses and it leaves through the commutator segment. The reversal of the current must happen at the end of the commutation period for ideal commutation.
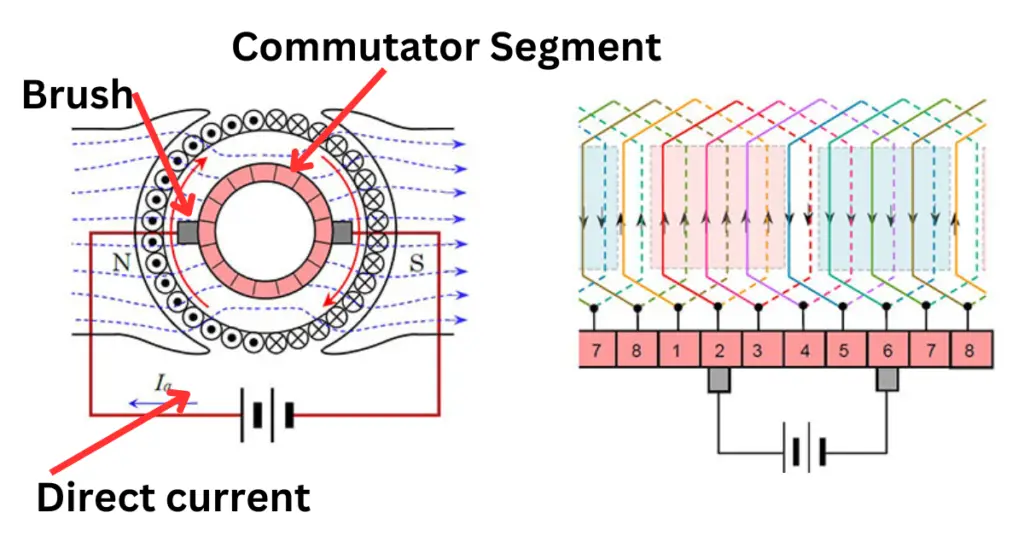
When the current does not completely reverse at the end of the communication period, you can observe the sparking at the brush contacts. This can lead to overheating and may cause damage to the surface of the commutator. In this condition, you can term the commutation as poor commutation.
How Commutation in DC Machine Works
To explain the commutation process, we consider a DC machine with its armature having a ring winding. Assume that the commutator bar and the brush have the same width, and the current flowing through the conductor is denoted as IC.
With the rotation of the armature, let the commutator move from left to right, then obviously the movement of the carbon brush is from right to left because the brushes do not rotate and remain fixed.
In the initial position, the brush makes contact with commutator bar b (as shown in Fig. 1). At this point, the total current flowing from commutator bar b to the brush is 2IC.
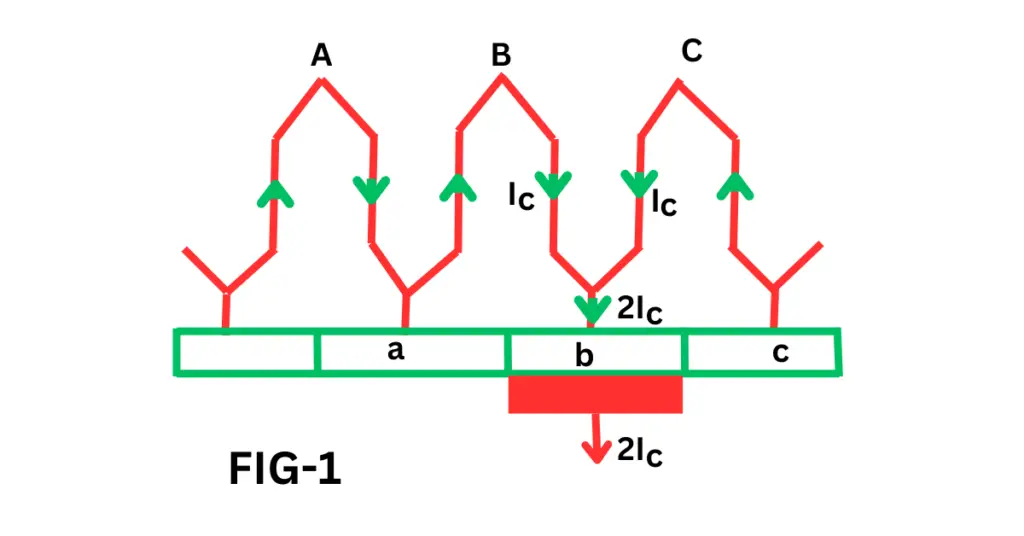
The brush comes into contact with the commutator bar when the armature moves to the right. At this point, the armature current divides and flows through two paths via bars a and b (as shown in Fig. 2). However, the total current (2IC) collected by the brush remains unchanged.
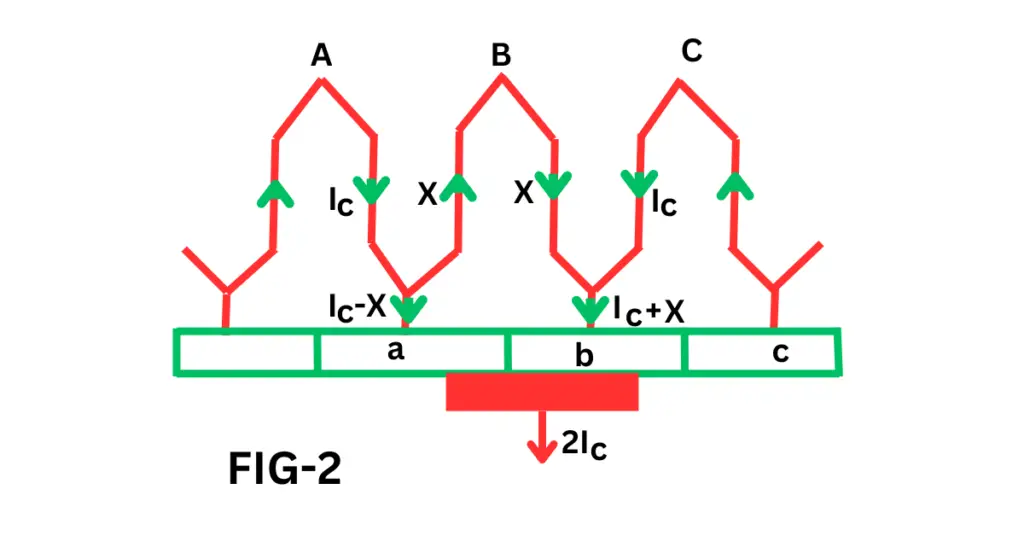
As the brush makes more contact with bar a and less with bar b, the current in bar A increases and the current in bar b decreases. When both bars have equal contact with the brush, the current divides equally between them (see Fig. 3).
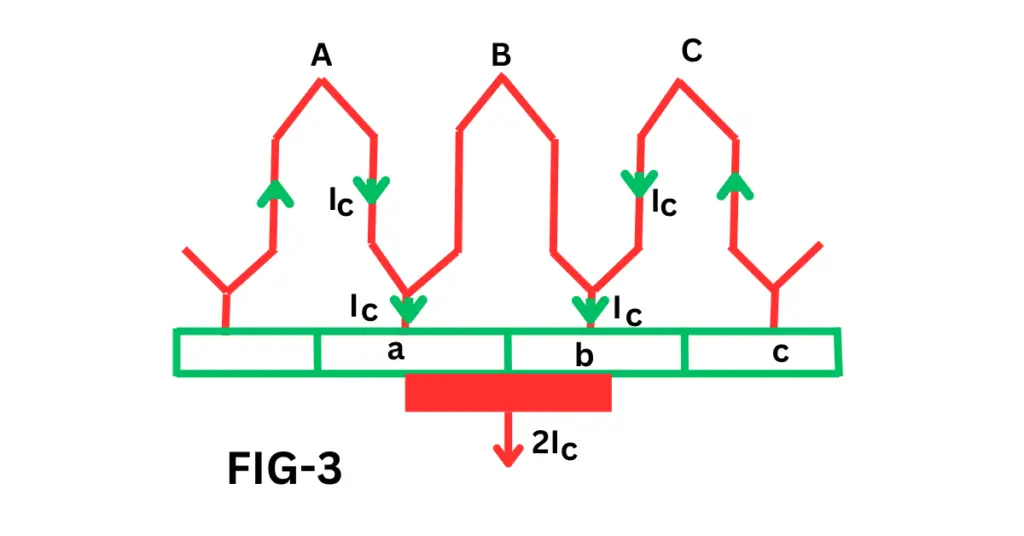
The brush connected to bar b moves further and its contact area with bar b decreases and causes current through bar b to decrease. Finally, the current in coil B reverses its direction and starts to flow counter-clockwise (as shown in Fig 4).
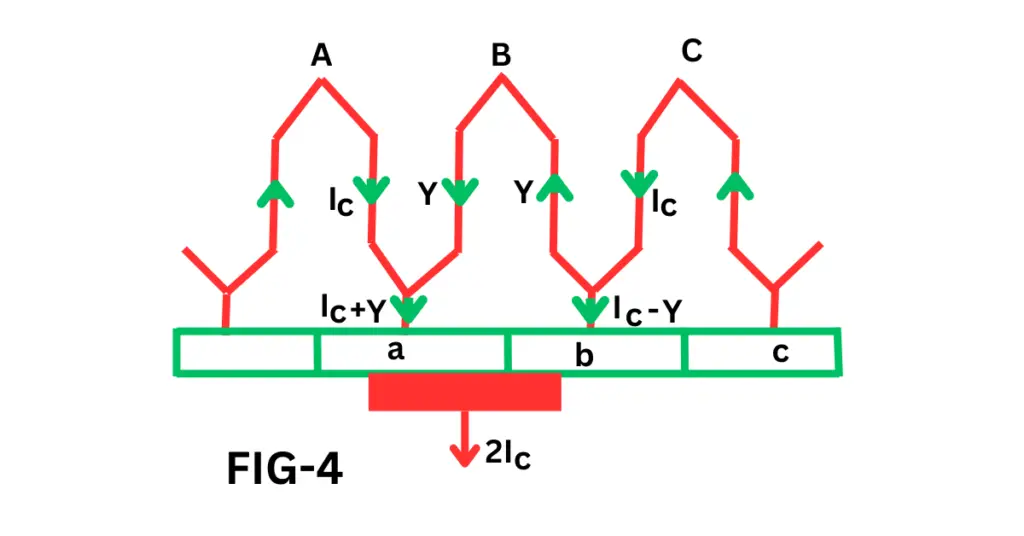
When the brush makes full contact with bar A and disconnects from bar B, the current IC flows in a counterclockwise direction through coil B, breaking the short circuit (as shown in Fig 5).
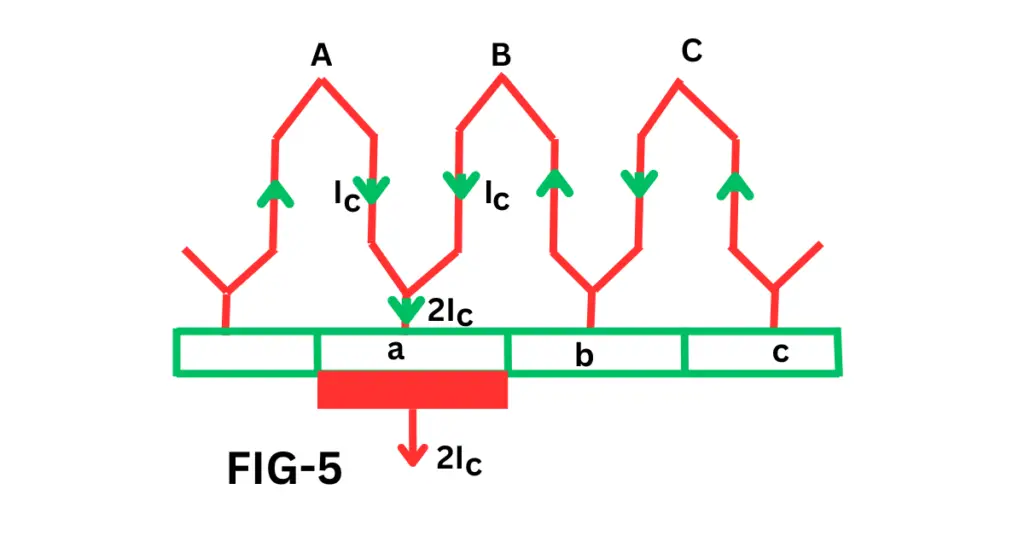
Methods of Improving Commutation
Sparkless commutation can be achieved through three different methods:
- Resistance Commutation
- Voltage Commutation
- Use of Compensating Windings