In this article, we will discuss the causes of contact sticking and coil burning in the contactors. The contactor is a type of electromagnetic switch. When the coil of the contactor receives the rated voltage, it produces a magnetic field and produces a magnetic pull that attracts the armature of the contactor and closes the contacts. On de-energization of the coil, the contacts get open.
Contactors are widely used in numerous applications like motor control, heater control, and many more. The contactors are generally used with Type-2 coordination. It means the thermal overload relay is used in the contactor’s circuit. The relay senses the overcurrent and de-energizes the contactor, thus it protects the electrical circuit from damage.
Contactors are the most important circuit element that is used for controlling the supply of equipment. Contactors must be selected as per the applications, or else there are possibilities of contactors failure. Although contactors are very reliable and failures are very rare, however, the wrong selection of contactors can cause damage to the contactor. There are remote chances of failure if the contactors are selected as per the requirement of the application and operated under its rated operating conditions.
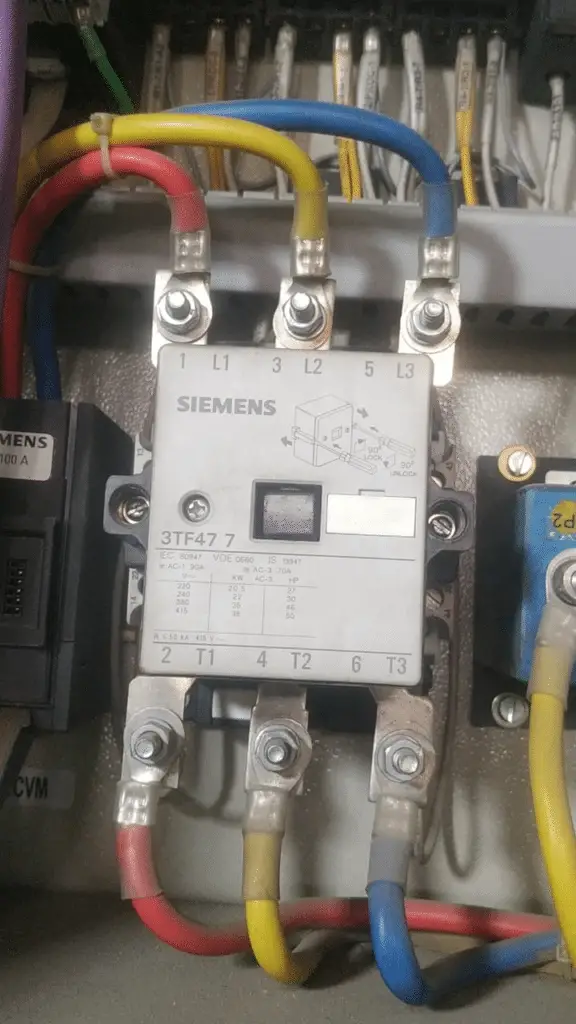
Have you ever encountered the problems like contact sticking and coil burning in contactors? Yes, these are the common problems that you may see in the contactors Let us discuss the reasons for these problems.
Reasons for Contact Sticking in the Contactor
Contactors have fixed and moving contacts. On contactor energization, the fixed and moving contacts come in the contacts, and current flows through them. The contacts have finite resistance and heat loss(I2R) takes place in the contacts due to contact resistance. The contactors are designed to carry a certain current through them. If the current flows through the contacts are equal to or below the rated current carrying capacity of the contactor, then the heat generated can not damage the contact.
However, what will happen if the current through the contacts is more than its rated current carrying capacity? Of course, it will generate more heat that may cause the sticking of the contacts. The sticking of contacts means the contacts get welded and when the contactor is de-energized the circuit will not isolate from the supply source. This may cause mammoth damage to the electrical system in view of safety and process control.
Now, we can say that the sticking of contacts happens when the current flow through the contactor’s contacts is more than the rated current. Now, you would like to know, what are the reasons for higher current through the contacts.
The reasons for contact sticking are the following.
1. Short Circuit
A short circuit occurs when the phase wire touched to neutral wire. In this condition, enormous current flows through the contacts, and if the protection devices do not trip the circuit in a timely manner, the huge current may cause contact sticking or contact welding. In the case of a short circuit, the fuse must blow out or the overload relay should issue a trip command to the upstream circuit breaker.
2. Wrong Selection of Contactor:
The contactors are designed for different duty classes. For continuous duty, AC-1 class contactors are suitable. AC-1 contactors are used for the resistive load that draws an almost constant current. Another type of load is a motor that is widely used in the industry. You all know, that motor draws about 6-7 times the current of its rated full load current(FLC). If we use an AC-1 contactor for motor application then its contacts are apt to stick because it can not carry this huge starting current. For motor applications, AC-3 duty contactors must be used to avoid contact sticking. Similarly, for capacitors AC-4 duty contactors must be used.
Reason for Coil Burning
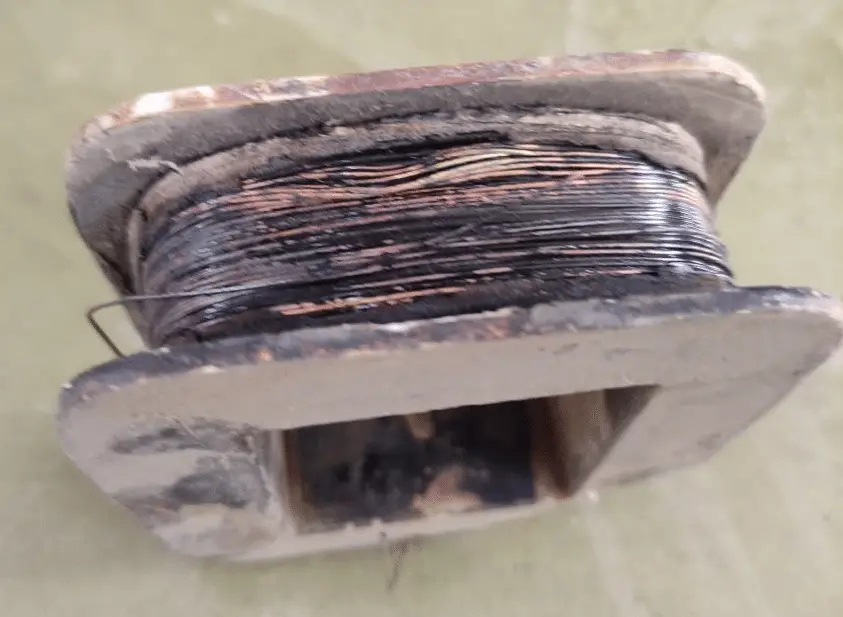
The followings are the reasons for coil burning.
1. Overvoltage
The coil is designed for the rated voltage. If the voltage exceeds the rated voltage the coil is vulnerable to burn. The overvoltage causes increased coil current above its rated current and heating of the coil cause insulation failure.
The reasons for overvoltage may be a lightning surge, voltage surges, transients, capacitor switching, and system overvoltage. The best method to keep the voltage within the limit is to use a control transformer. The control transformer provides the isolation between mains and secondary voltage and thus it eliminates the chances of transient voltage to the contactor coil.
2. Overcurrent due to Physical Obstruction
If the contactor’s coil draws more current than its rated current, then the heat generation can cause insulation failure and damage the contactor. One of the reasons we discussed is the overvoltage. Another reason for overcurrent in the coil is dust and foreign bodies in the air gap. The increased air gap causes the coil to draw more current for producing more magnetic pull. Therefore, contactors must be cleaned thoroughly during maintenance.
3. Under Voltage
If the voltage is much below the rated voltage the coil tries to make the rated magnetic field by drawing more current to activate the contactor, however, the contactor does not pick up and eventually, the coil burns out. Therefore, the voltage must be kept within the permissible limits of the coil.
4. Under Frequency
The frequency also plays a vital role in the current of the coil. The coils are specified for a certain voltage and frequency. The impedance of a coil depends on the frequency and can be given by the following formula.
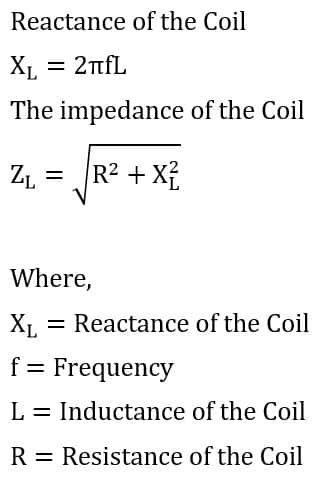
The higher frequency than the rated coil frequency causes impedance to lower and coil draws less current and the contactor does not activate. If the frequency is lower than the rated frequency of the coil, then the coil has less impedance and draws a large current. Thus, a lower frequency than the rated frequency may cause coil burning.
This is all about the causes of contact sticking and coil burning in contactors.