This article describes different types of valves. Valves are essential components that control fluid flow and are widely used in various industries in process control applications. After reading this post, you will gain valves insights and their applications.
Types of Valves of different designs and sizes are available in the market. The valves are used to control fluid through a pipe, cutting, bypassing, or modulating its pace.
Different valve designs cover different operating requirements. Valves are used for controlling the process, and knowledge of valves is crucial for every process and instrumentation engineer.
Table of Contents
The designer considers the following points before selecting a valve type and its construction materials.
- Temperature
- Flow
- Operating pressure
- Environment conditions (Fire Safe, Chemical hazards)
- Operating requirements
Types of Valves
In this article, we will discuss types of valves.
1. Gate Valve
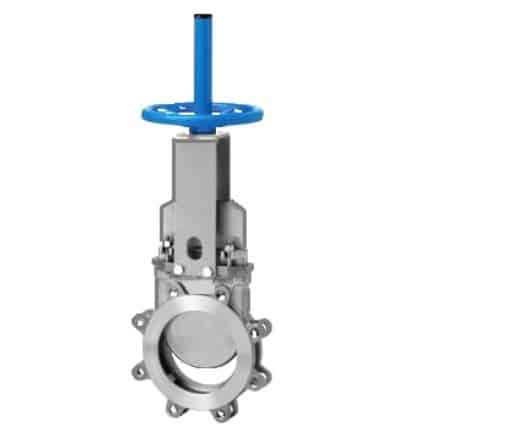
Gate valves are suitable for cutting or opening the way to a fluid, usually liquid. Their bidirectional design allows users to install the valve in any direction. These valves are most suitable for open or closed services (ON-OFF) and must always be open or closed.
Since it is in an intermediate position, a lever is generated in the stem that can deform it, leaving the valve inoperative; in addition, a lot of cavitation is generated due to the turbulence produced by the valve’s gate located at mid-stroke.
Gate valves are classified according to the design of the wedge (mirror, gate); their main designs are as follows:
Solid Wedge: This design is the oldest. It is most suitable in applications where a high level of tightness is not desirable. Usually metal-metal seat.
Flexible wedge: It is the evolution of the solid wedge; it allows a better level of a seal since the wedge enters a cavity of the valve body (seat) flexing towards each other. Due to the effect of the elasticity property of metals, it generates pressure on the seat, ensuring a better seal than the solid wedge. We use it in liquid and viscous fluids with a low percentage of suspended solids.
Resilient wedge: This wedge is the most used for water and wastewater since it allows a tightness level of 99% or higher. The entire wedge is covered with an elastomer that conforms to the valve body (seat), achieving the seal. This elastomer must be EPDM for clean water applications and NBR (Nitrile) for wastewater.
Read More: Gate Vale Construction, Operation and Applications
2. Ball valve
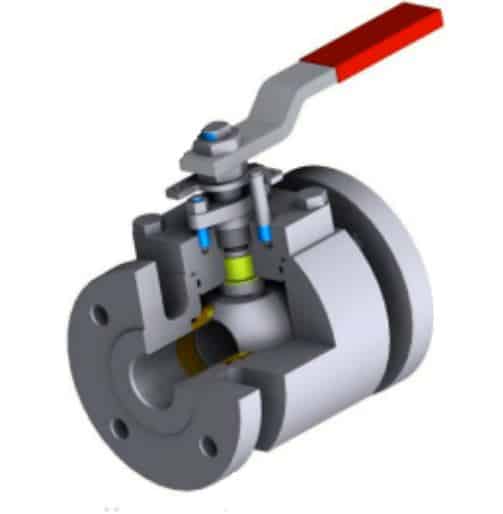
Ball valves are the most widely used bidirectional valves in small-diameter industrial applications because they allow a high level of tightness and easy operation. The valves have double ring-shaped seats, one at each end of the ball, giving a double level of seal reliability. The material and design must be selected according to each application.
They can be a full bore or reduced bore.
Full bore valves are suitable for fully open or fully closed (ON-OFF) operation and do not generate interruptions in their open position.
On the other hand, the reduced port valves, if used to modulate the flow of the fluid, nevertheless generate a considerable pressure drop, even in its fully open position.
Classification of Ball valves
Floating Ball Valves
This is the ball valve par excellence; we find it in the most demanding industrial applications to the taps in our homes. Ball valves can be made of different materials, with one, two, or three bodies.
Guided Ball Valves (Trunnion)
These valves are used in gaseous fuel applications where tightness is critical to avoid leakage. The valve seats are pressed into the ball through a spring (energized seat). Its design and tests follow API standards.
Read More: Ball Valve Construction, Operation & Applications
3. Butterfly Valves
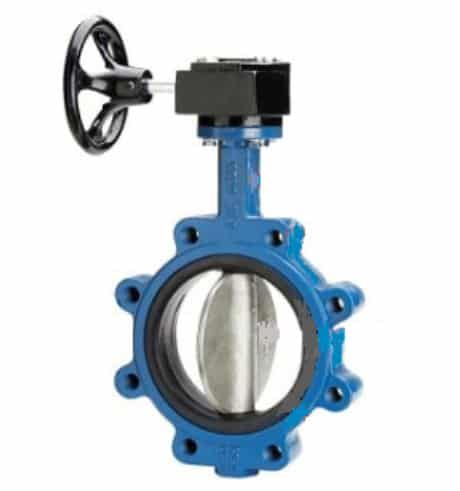
The Butterfly valves are the most versatile on the market. Butterfly valves can function as an ON-OFF or modulating service valve and, like ball valves, are bi-directional in design. Although in some cases, they tend to have a favorite sense of flow.
These valves are classified according to the convergence of the centers of their principal parts (disc, body, stem, and seat).
Concentric Butterfly Valve
A concentric butterfly is the most used and simple on the market; it is called concentric because the body, disc, and stem converge on the same axis. The seal between the disc and the seat occurs in a specific way around the entire perimeter of the disc.
They are reliable and inexpensive.
The seat material is usually made of an elastomer (EPDM / NBR / VITON), but they are also found with seats made of Teflon and other materials. We find them on the market in 2 designs.
Wafer, to be installed between flanges with studs and LUG, to be installed with bolts fitted in the valve body; the latter can be used as an end of the line.
Eccentric butterfly Valve
It is given this name because the centers of the valve elements do not converge on the same axis. This butterfly design improves the level of tightness of the concentric since the seal is not given in a punctual way, but there is a seal area between.
4. Diaphragm Valve
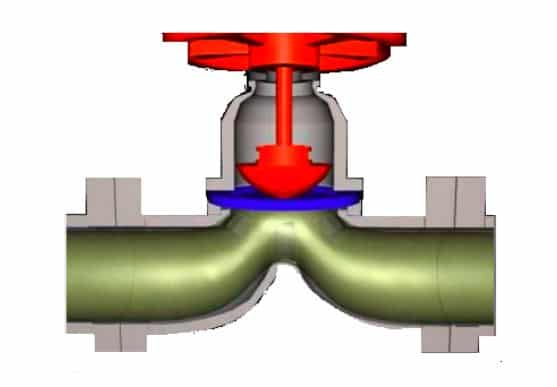
Diaphragm valves are multi-turn and close by means of a flexible diaphragm attached to a stem with a compression arrangement. When the valve stem lowers the compressor, the diaphragm seals the flow and cuts off circulation.
Diaphragm valves isolate the fluid from the operating mechanism’s stem, compressor, and other upper parts. This makes them ideal for corrosive or viscous services, as they avoid any contamination to or from the outside.
Diaphragm Material
Buna N (NBR), Ethylene Propylene (EPDM), Natural Rubber (NR), Neoprene (CR), PTFE, and Viton.
Read More: Working of Diaphragm Valve
5. Plug Valve
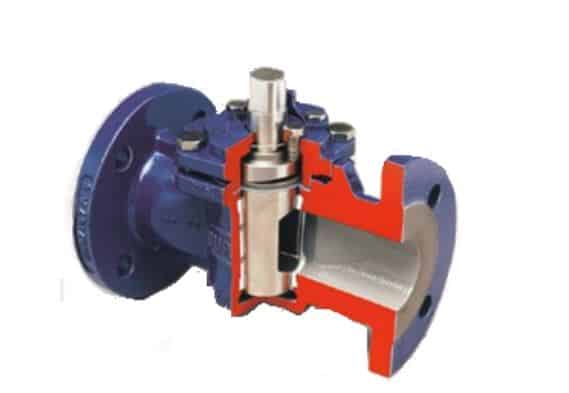
The plug valve is a quarter-turn valve, which controls the flow by means of a cylindrical or conical plug body having a hole in the center. The plug can be moved from the open to the closed position by a 90 ° turn.
Plug valves can generally be easily cleaned or repaired without removing the body from the plumbing system.
6. Globe Valve
The globe valve is a linear motion type of valve. It is used in on-off & throttling applications. The fluid through it flows in an S-path.
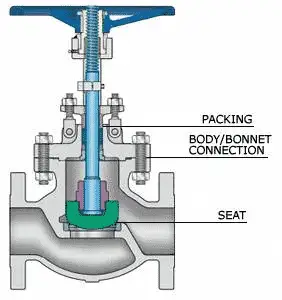
The higher pressure drop takes place in the globe valve because the fluid flow direction changes twice. Globe valve is most suitable for application that needs frequent throttling.
The Globe valve is used to cut off the flow of the medium and is suitable for occasions that need to be throttled frequently. The most commonly used is in chemical production.
Read More: Globe Valve Construction. Operation & Applications
Useful Resource: Wikipedia- Control Valves
Read Next :