A thermal overload relay is a safety device that triggers a circuit-breaking phenomenon by sensing a fault on the line it has been connected to.
What is a Thermal Overload Relay?
As the name suggests, a thermal overload relay protects a machine or a power system network against a fault due to rising temperature.
A rise in temperature can happen due to various reasons like continuous operation or load on the power system being higher than the stipulated capacity or any fault causing the flow of short-circuit currents. Therefore, it is critical to identify and mitigate any such fault at the earliest. A thermal overload relay is used for this purpose.
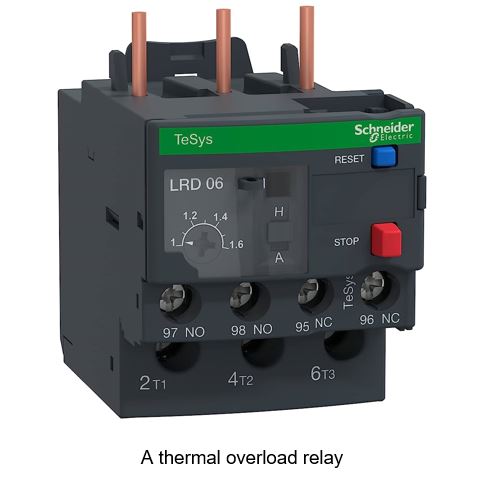
If the temperature of the given system increases beyond a set point, the thermal overload relay operates and disconnects the faulty element from the rest of the system.
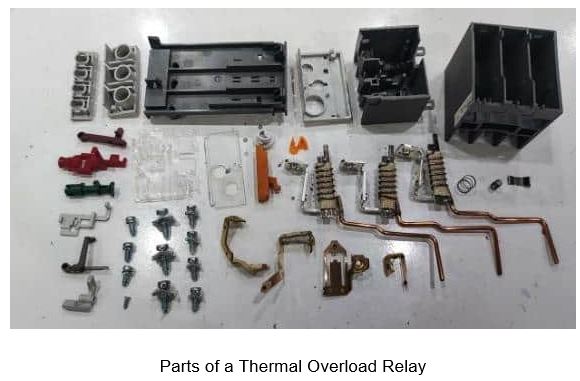
Various Sections of a Thermal Overload Relay
A thermal overload relay is essentially a feedback-based protection mechanism. The relay is connected to the system or the appliance withdrawing current from a certain source. This current goes to the system through the relay contacts. The basic idea is that the relay takes this current and recreates the heat generated in the system within itself.
Under normal situations, the heat generated within the relay remains normal. But during a short-circuit or overloading, the machine or the system begins to draw a huge amount of current which can cause damage due to heat. This current goes through the relay and it senses the increase in temperature. As a result, it breaks open the circuit and protects the device or the system from being damaged permanently due to heat.
A thermal overload relay comprises various movable parts that can sense heat and initiate the tripping of the faulty line from the others.
- Temperature sensing element: This is usually a bi-metallic strip. As the name says, a bi-metallic strip is made up of two distinct metal strips. Under high temperatures, the strips expand and bend. The amount of expansion depends on the temperature it faces which is directly proportional to the amount of current passing through the relay to the system. Thus, this bi-metallic strip acts as a physical temperature sensor based on which the relay can initiate any further action required.
- Tripping mechanism: This section consists of necessary levers, slides, and springs which can trip the circuit once the bi-metallic strip senses higher temperature for a prolonged period of time.
- Relay contacts: A thermal overload relay has two contacts – Normally Open(NO) and Normally closed(NC). When a fault is detected, both of these contacts switch their position to disrupt the high amount of current flowing to the system or the appliance.
Working Principle of a Thermal Overload Relay
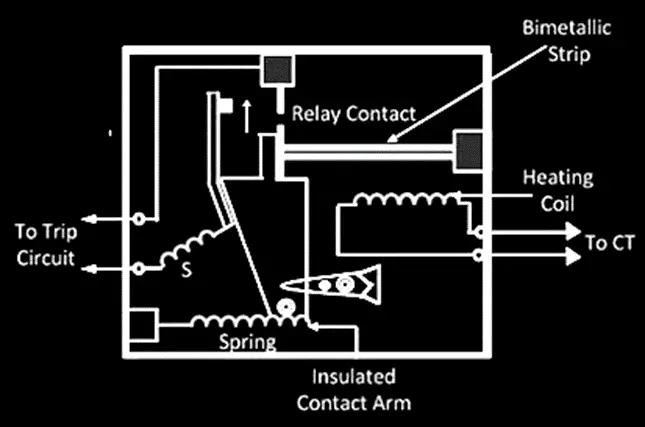
The picture above shows the internal structure of a thermal overload relay. It consists of a bimetallic strip made up of two different metals. One of them has a higher coefficient of expansion, while it is lower for the other one.
The relay has two contacts. One of those contacts remains Normally Closed (NC) while another remains Normally Open (NO) and hence they are named so. The current to the load goes through the heating coil of the relay which heats up in proportion to the current supplied.
Under normal circumstances, the current is not high enough to affect the position of the bimetallic strip. But if an overload current begins to flow through the heating coil to the load, the heat generated from the coil causes the bimetallic strip to bend. The one with a higher coefficient of expansion bends more than that with a lower coefficient of expansion. As a result, the bimetallic strip bends in one direction such that it closes the normally open contact. This contact is connected to the trip coil and as it is closed now, the trip coil gets energized causing the power to the load to be discontinued.
At the same time, the relay opens up the normally closed (NC) contacts causing the power to the load to be cut off. In this way, the relay protects the load from being overloaded.
A thermal overload relay is not an instantaneous relay. It depends on the heat generated in the heating coil due to the current passing through it. The heat generated in the heating coil of the relay can be calculated by the formula derived from Joule’s law of the heating effect of current given by

Where i is the current passing through the heating coil to the load, r is the resistance of the heating coil and t is the time for which the current passes through the heating coil. The action of the relay depends on the amount of heat generated.
As it is clear from the equation, the heat generated is directly related to the time for which the current flows. Hence, a thermal overload relay is a time-dependent relay that operates on the sustained flow of overload current. This is also desirable because some operations like in the case of a motor cause them to be in the state of overload for a short duration of time. A thermal overload relay allows that window unlike that of an instantaneous relay.
Once the problem of overloading is identified and corrected, the relay must be reset manually before resuming the operation. However, there are relays with automatic reset as well. The overload current for which the relay should operate can also be set manually.
Auto Reset vs Manual Reset on Thermal Overload Relays
The thermal overload relay needs to be reset once it trips on overloading. The relay has two types of reset options- automation and manual reset- that can be used as per your applications.
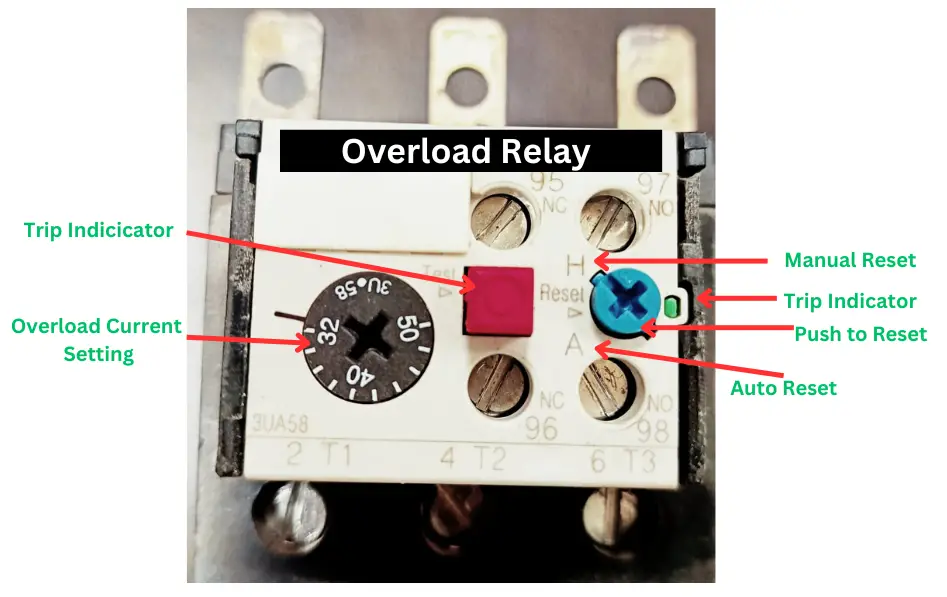
Manual Reset
The relay needs a manual reset after tripping due to overloading if the relay is set for manual reset. The electrician has to go to the site to reset the overload after every overloading. After resetting the relay, the motor can be started.
The relay does not reset if the temperature inside the relay does not reach to a particular temperature. Therefore, an electrician should wait for adequate cooling of the relay. Also, there is a need to ensure proper cooling of the motor feeder.
Automatic Reset
The auto-reset feature in the relay does not require manual intervention. The relay reset automatically after getting sufficiently cooled down. The Bi-metallic strip detects the cooling of the relay. The relay returns to its healthy state once the temperature reaches the predefined value.
In the auto rest feature, the motor gets the start command once the relay aquatically resets. The disadvantage of this feature is that the motor can get many commands in the fault or overloading conduction. This may lead to motor failure. In manual reset mode, the electrician can check the healthiness of the motor and electrical system before resetting overload.
How to Set Thermal Overload Relay
The relay needs the following settings.
- Selection between manual and automatic reset
- Adjustment of current setting as per the motor full load current
The improper settings may cause failure of the contactor and motor. Suppose the motor full load current is 12 A, and if the relay is set at 13 A will eventually cause motor insulation failure. The correct current setting is a must for timely tripping of the motor to safeguard the motor and electrical system.
Types of Thermal Overload Relays
- Bimetallic thermal relay: As we discussed above, this type of relay consists of a bimetallic strip that acts as a heat sensor and causes the relay to operate in case of a prolonged overload.
- Solid-state relay: Solid-state relays have no mechanical or moving parts. This relay simply calculates the information of the Thermal overload relay and the normal motor temperature by simply monitoring its beginning & running currents. These relays are faster compared to electromechanical relays and also include trip times & adjustable set points because they are not capable of generating a spark, so used in unstable environments.
- Temperature control relays: Temperature control relays detect the motor temperature directly using a thermistor and a Resistance Thermal Device(RTD) probe connected directly to the winding of the motor. Once the threshold temperature of the RTD reaches, its resistance rises rapidly. This is sensed by a threshold circuit that opens the contacts of the relay.
- Melting alloy relay: It consists of a heater coil, a low melting point alloy, and a mechanism to break the circuit. The heater coil heats up as the overload current passes through it and causes the relay to operate.
Advantages
- Thermal overload relays have higher accuracy.
- These relays protect electrical motors from overheating. So they can be used conveniently in single-phase and three-phase motors.
- These relays are easy to install
- They have an internal test button for testing the relay
- These relays operate on a sustained duration of overload current and hence allow the motor to be operated at overload for a short time if required.
- Operates on a wide range of current.
- Certain overload relays have internal trip class selection buttons.
- The relays have auto and manual reset options
- The relays have temperature compensation features for accurate functioning.
- They are cost-effective.
Disadvantages
- Thermal overload relays are mostly slow in their response.
- These relays need time to cool down after operating once and hence have low cycles of operation.
- These relays are not able to withstand shocks and vibrations.
- Not very helpful during short-circuit events where instantaneous tripping of the circuit is important.
- These relays are not very reliable in heavy-duty operations.
- They do not provide short-circuit protection.
- Thermal overload protection devices function reliably against low-resistance circuits. They are not suitable for heavy-duty circuits.