There are many DCS applications in industries for plant automation. Within the industry, all field instruments are connected to a junction box individually. From the junction boxes, a multi-pair cable will connect to the control room.
In the DCS, the cables are received in the marshaling cabinet. Here, the cables are sorted out as analog input (AI), analog output (AO), digital input (DI), and digital output (DO) cables. The signal then flows to the system cabinet, where signal conditioning takes place, and outputs are generated accordingly as per the program written in the controller.
Applications of DCS
DCS finds application in various fields. Some of them are listed below.
- Various power plants, such as nuclear power plants, hydroelectric, thermal, solar, geothermal, fossil fuel, etc.
- Chemical plants
- Petrochemical plants
- Metallurgical industries
- Automobile industries
- Food processing industries
- Water handling plants and sewage plants
- Environmental management systems
Various types of DCS manufacturers like Yokogawa, Honeywell, Emerson, Foxboro, etc are available in the market which supplies DCS for various applications mentioned above.
Automation Structure
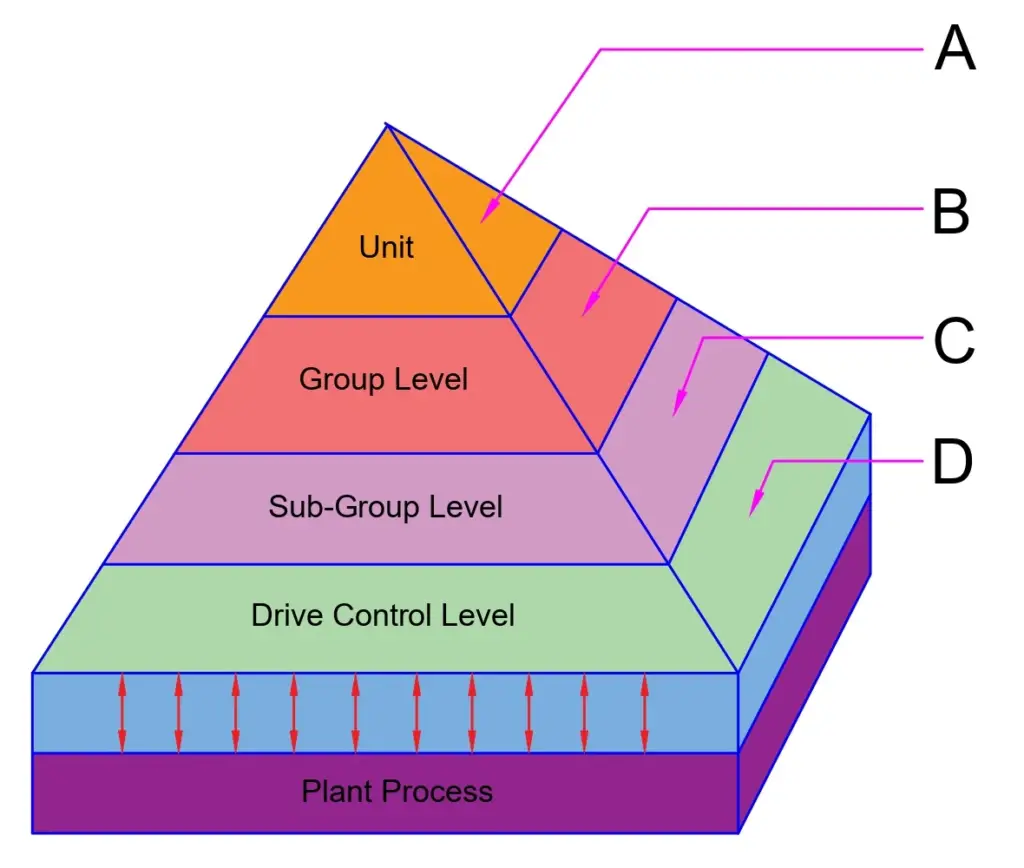
The DCS follows a structure at different levels. From field instrument in the field to the controller in the control room, a specific type of structure is followed by DCS. A common type of architecture is shown in the above image.
Unit Level
Unit level performs the function of monitoring, logging, and advanced control machine communication. The unit level is structurally distributed over centrally located computers. The unit level is also known as level 4. This level is the highest level.
Group level
The group level performs the function of modulation and binary control. Structurally, the Group level has microcomputers distributed over groups. The group level is also known as level 3.
Sub-group level
Sub-group level performs the function of modulation and binary control for a subprocess. The sub-group level is structurally also similar to the group level. Sub-group level also has microcomputers distributed over groups. Here, a Unit Master Controller (UMC) will control and coordinate the total plant and command the lower levels. The sub-group level usually controls the plant start-up and shutdown. Sub-group level also coordinates the plant process during the load variation. The sub-group level is also known as level 2.
Drive Control level
The drive control level performs the function of basic logic, protection, and equipment drive. The drive control level provides protection for the pump, valve, or damper. Drive control level terms of structure, the microprocessors’ solid state is distributed over all the drives. The computers here collect all the relevant data of the plant, alarm reports,s and log data to provide historical storage and performance calculations. The drive control level is also known as level 1.
Plant Process Level
The plant process level consists of the field devices like final control elements such as control valves, temperature sensors, and flow elements. We can say that the eyes and hands and legs of the control system are present in this level i.e. all types of transmitters and control elements are present in this group. The plant process level is known as level 0.
Hardware structure of DCS
The hardware structure of DCS can be made according to the DCS application. The general arrangement of the DCS structure is given below.
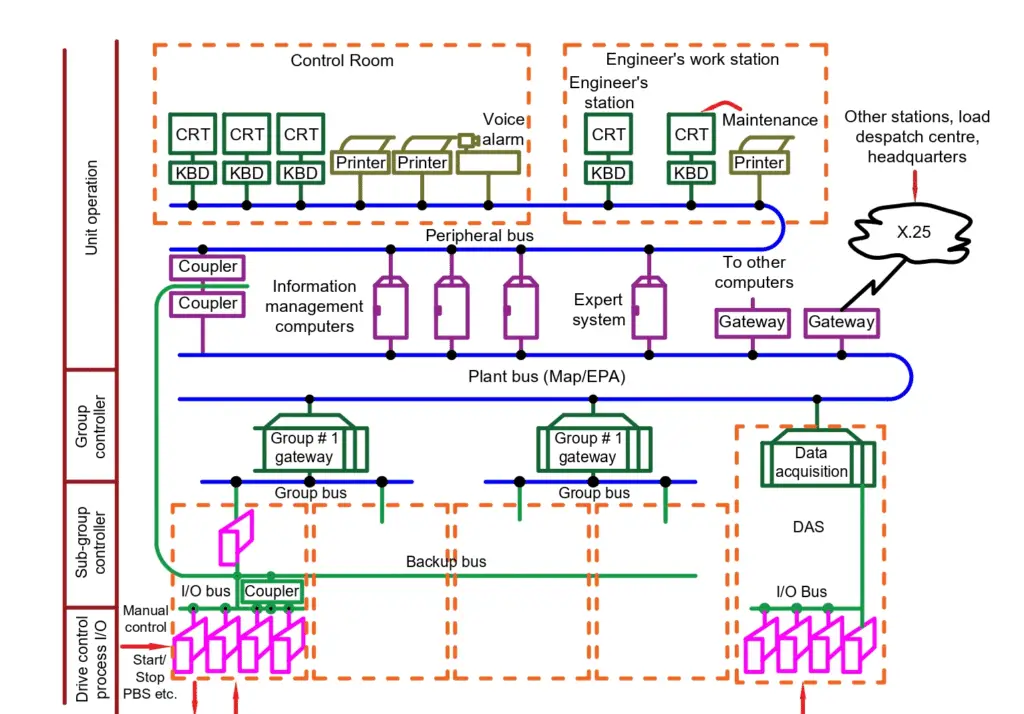
Components of Hardware Structure of DCS
The hardware structure of the plant has the following components:
Field Station
The field station has an input unit, an output unit, and some drive control modules. The function of these modules is to provide an interface to the process including push buttons, indicators, and drives. The protection logic is generally included in the drive control modules. This module basically ensures plant safety. This logic is implemented by Electrically Erasable Programmable Logic Devices (EPLDs).
The field station modules consist of the following characteristics:
- The field station modules have built-in microprocessor-based intelligence systems.
- Signal conditioning is also performed in the field station modules.
- They have built-in basic protection using EPLDs.
- The modules have programmable fail-safe output conditions.
- They also have direct manual intervention at drive levels.
- The field station modules have a plug-in interface for serial I/O bus for greater reliability.
- They have a modulating and binary control that is being controlled under the control of the sub-group holder.
Sub Group Controller Station
Sub-group controller station has a high-performance micro-computer module that has a direct interface with the serial I/O bus and a higher-level group bus.
Group Controller Station
The group controller station provides the control for each plant sub-process. The group controller station also coordinates the control of individual equipment groups. The group controller station is interconnected by the plant bus for exchanging data among themselves and with the higher-level controllers. These are equipped with high-performance microprocessors along with necessary memory modules.
Unit Level Control
Unit-level control has display and keyboards which are supported by hard copy units. Here, the plant data is evaluated, sorted, processed further, and assigned to various display units or printers for logging. Some color CRTs can be used as a part of low-cost PCs along with the necessary display functions. The unit-level computers will send the required dynamic data for reducing the processing overhead.
It depends on the control philosophy to be employed for a particular point to determine how many CRT workstations will be needed. The number of unit-level computers also depends upon the extent of functions required to be performed. A manual control station will help in the operation of final control elements while bypassing all the above control stations.
Unit-level computers have the following functions:
- Enhances plant automation
- Help in control operations
- Help with alarm and display control
- It does calculations and logs for historical recording.
- Unit-level control also supports software development.
- It also serves a major role in database management.
Plant Bus
The plant bus goes through the plant for connecting all sub-group control stations and level stations. The plant bus is a map-type system that is able to integrate other computers and systems. The plant bus updates the plant database through the lower-level buses that are maintained at the unit level. The plant bus transmits unit operation commands to the lower-level controller.
Bus System
- In the DCS architecture, the bus system is an organized system that is generally at the lowest level and connects the I/O cards and drive cards of a particular sub-group.
- The bus system is a short-distance bus that is generally confined to the cabinet that houses a sub-group controller. The I/O bus is controlled by the sub-group controller. It must have a short time response to the plant conditions. The I/O modules are intelligent and only status or other significant changes must be reported over the bus for reducing bus speed consideration by using RS 485 connector.
Group Bus
Group bus connects all the sub-group controller stations and the pertaining group controller stations. Group bus also enables the group controller for performing the overall control coordination in a group.
Peripheral Bus
The peripheral bus is used to connect all CRTs, keyboards, printers, and video copiers that are required to operate and monitor the plant.
Backup Bus
The backup bus provides a direct connection from the I/O bus to the plant bus. The backup bus has a CRT or keyboard of the plant which operates in case of any failure at the group or subgroup levels. When in case, intelligent sensors and actuators are introduced, then the need for many I/O and drive cards can be dispersed. It can be necessary to link these devices with a field bus.