Flanges are used to connect pumps, pipes, valves, and other equipment for the construction of a pipework system. Flanges can be threaded or welded. Two flanges can be connected by bolting with a gasket and providing a seal which would give easy access to the piping system.
Types of Flanges
The different types of flanges are ;
1. Slip on Flanges
The slip-on flange is a ring (with or without a hub) that is placed over the pipe’s end. The flange face which extends from the pipe end that is at a sufficient distance is applied to a welded bead to the inner diameter. Slip-on flanges slip over a pipe and hence are known as slip-on flanges.
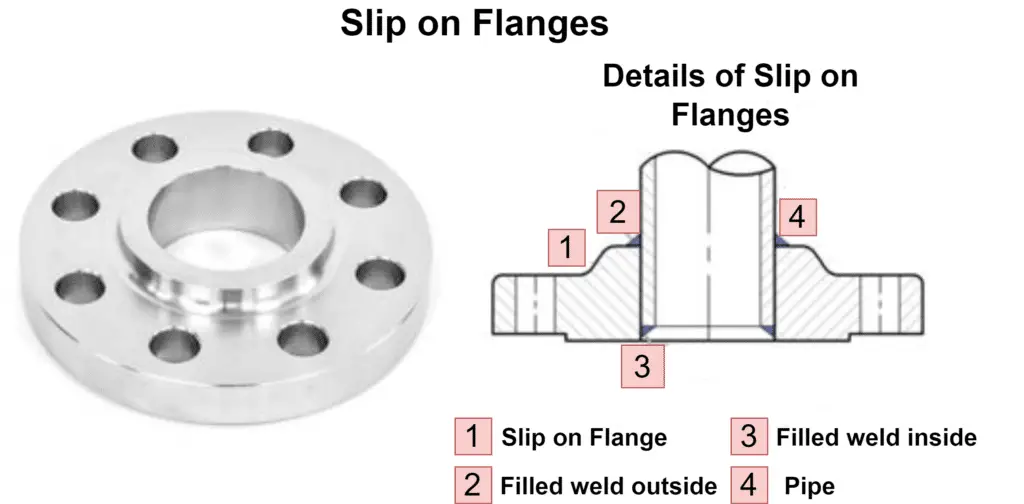
2. Weld Neck Flanges
Weld neck flanges are also known as high-neck flanges or tapered hub flanges. The weld neck flange has a neck that is able to transfer the pipe tension properly. Weld neck flanges also help in reducing the pressure that is gathered at the bottom of the flange.
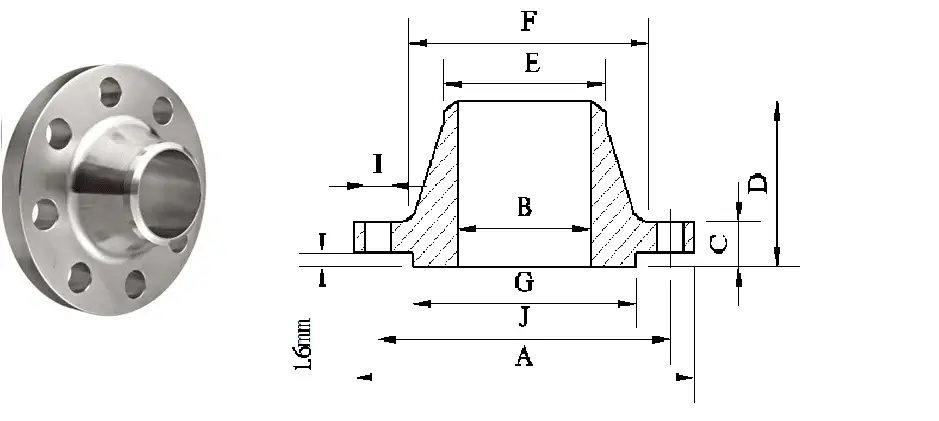
Weld neck flanges are compatible with pipelines that operate at low or high temperatures and withstand high pressures.
3. Socket Weld Flanges
Socket weld flanges are connected on the outside by a fillet weld. Socket weld flange is not advised for critical service. Socket weld flanges are also useful in small bore lines in the system. Socket weld flanges have static strength equivalent to slip-on flanges, but fatigue strength is 50% higher than double-welded slip-on flanges.
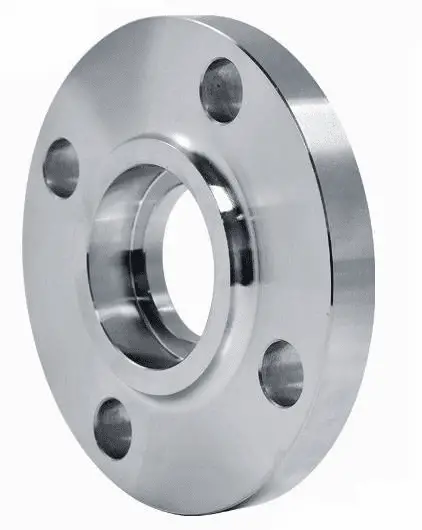
Socket weld flanges are generally used as an alternative to weld necks when there is a constraint of space. To use socket weld flanges, the thickness of connecting pipe must be defined in order to ensure proper bore length. Before welding the flanges, a gap must be formed in the socket weld flange/fit and the pipe. The socket weld flange is welded to the inner diameter of the pipe.
4. Threaded Flanges
Threaded flanges are generally made of steel. Threaded flanges have applications in special cases. The major advantage provided is that threaded flange can be connected to a piping network without welding. In some applications, a seal weld is used along with a threaded connection. Screwed fittings are generally used for small pipe sizes. The threaded flange is used to connect other threaded components at low pressure.
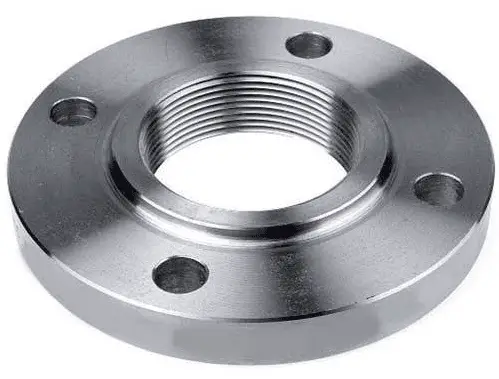
Threaded flanges are generally used for low-pressure and low-temperature applications like water and air utility services. Threaded flanges cannot be used in explosive areas as a welded connection can prove dangerous. Threaded flanges also can not be used in pipelines having thin walls as thread cutting will not be feasible. Threaded flanges can also not be used for conditions that involve temperature or bending stresses of any magnitude, because in cyclic conditions leakage may occur through the threads in a few cycles.
5. Blind Flanges
Blind flanges are used to close the ends that need to be reopened later. Blind flanges are used to blank off ends of piping, valves, and pressure vessel opening. Blind flanges are constructed without a bore. Considering the internal pressure and bolt loading, the blind flanges that are larger in size are the most highly stressed flange type.
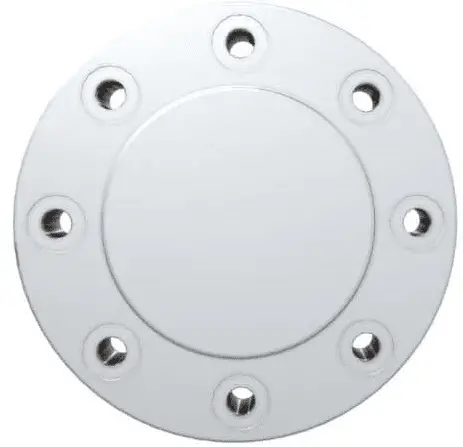
The blind flange is basically a flat metal plate that is used to block a flow in the piping system. When these are used, there is easy access to the vessels or piping system for inspection. Blind flanges can be used for high-temperature and pressure applications.
6. Lap Joint Flanges
Lap joint flanges are of use with stub ends when the piping is of costly material. Lap joint flanges are cost-effective in an expensive pipe, for example, stainless steel, as in these only the stub must match the pipe and the flange can be made of cheap carbon steel material.
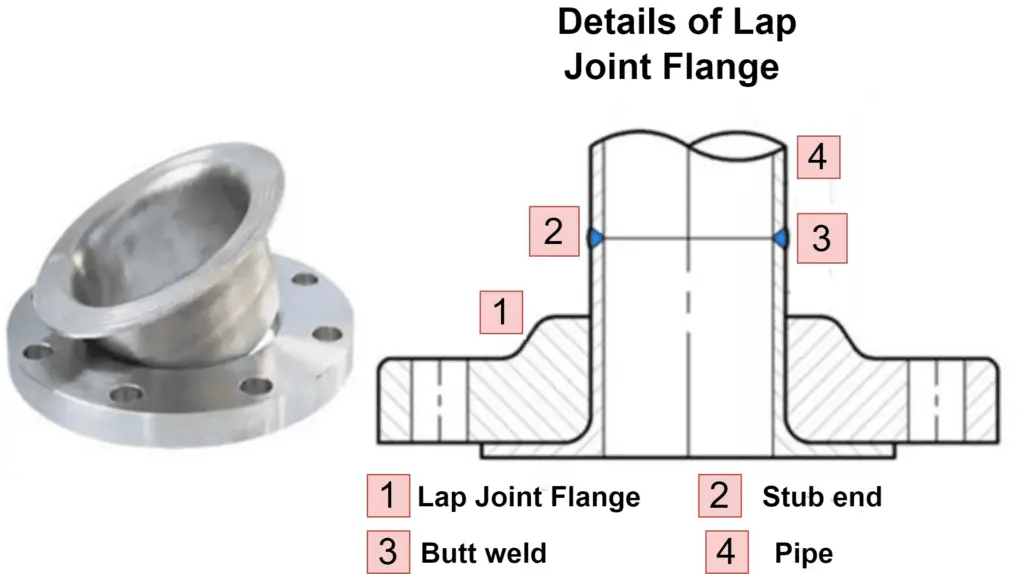
Lap joint flanges have the less pressure-holding capability. Lap joint flanges are used in services that need frequent dismantling for inspection and cleaning. Lap joint flanges are also used in systems where flanges would erode or corrode quickly.
7. Long Weld Neck Flanges
Long weld neck flanges are almost similar to weld neck flanges. Long weld neck flanges differ in the way that their neck is extended and acts as a boring extension.
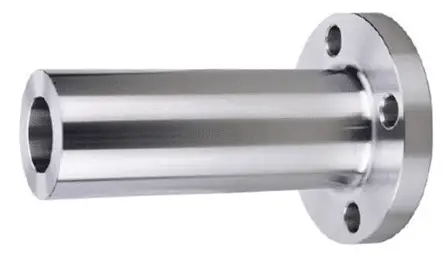
Long weld neck flanges are generally used in vessels, columns, or barrels.
8. Orifice Flanges
Orifice flanges are used when an orifice plate or flow nozzle must be installed. The orifice or flow nozzle needs pressure tapping points, these pair of pressure tapping points are machined into the orifice flange.
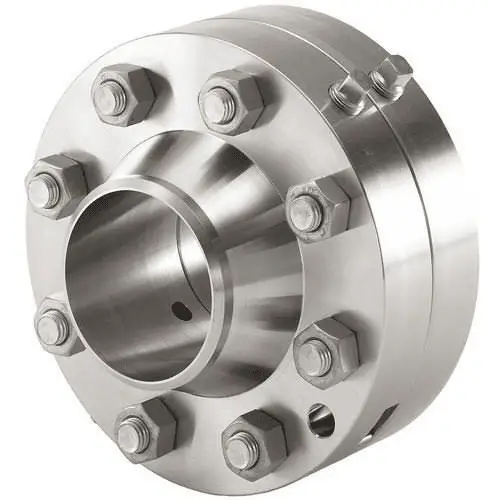
So, there are separate orifice carriers or tapping points in the pipe wall. Orifice flanges are used for instrumentation connections and are used in conjunction with a flow meter to indicate flow.
Materials used to manufacture flanges
Pipe flanges are manufactured from many different materials which depend on the piping material and requirements of the application. Selection of the materials depends on various factors like economy, flow, pressure, operating temperature, and environmental corrosion. The most commonly used materials are:
1. Carbon steel
Carbon steel is steel that is alloyed with carbon. As the carbon content increases, the strength and hardness also increase, the melting point lowers and ductility also lowers. Carbon steel is the most common material grade.
2. Alloy steel
Alloy steel is steel that is alloyed with one or more elements that change or enhance the property of steel. The common alloys are chromium, molybdenum, nickel, vanadium, and manganese.
3. Stainless steel
Stainless steel is steel that is alloyed with chromium in amounts above 10%. Chromium enables stainless steel to have high corrosion resistance compared to carbon steel which rusts readily from air and moisture exposure.
4. Cast Iron
Cast iron is formed when the iron is alloyed with silicon, carbon, and several other alloys. With the use of silicon, carbon is forced out of iron and forms a black graphite layer on the exterior of the metal. Cast iron has good machinability, castability, and fluidity.
5. Aluminum
Aluminum is a low-density, ductile and malleable metal which has medium strength. Aluminum has better corrosion resistance as compared to any other typical alloy and carbon steel. Aluminum is also the most useful during flange construction which requires low weight and strength.
6. Brass
Brass is an alloy of zinc and copper. Brass generally comes with additional elements like tin or lead. Brass has characteristics like good conductivity, cold ductility, high-temperature ductility, and good strength.
7. PVC
Polyvinyl chloride or PVC is a thermoplastic polymer that is easy to assemble, durable and inexpensive. PVC is resistant to both biological and chemical corrosion. If plasticizers are added, PVC is made more flexible and soft.