Preventive maintenance of variable frequency drive(VFD) ensures smooth and trouble-free operation of the process. Any breakdown in VFDs causes production loss and power loss. Therefore, it is a must to do preventive maintenance of variable frequency drives in a scheduled time frame.
Variable frequency drives are known by various names. So many people can get confused and think that they are talking about different equipment but is the same. They are known as;
- Variable Speed Drives (VSD)
- Frequency inverters (not frequency inversion)
- Inverters
- Variable Frequency drives (VFD)
- Drives
All of these names apply to the same equipment and they are all correct in some way. The resulting function of everything that happens inside a variable speed drive is just the possibility of modifying the speed of the electric motors.
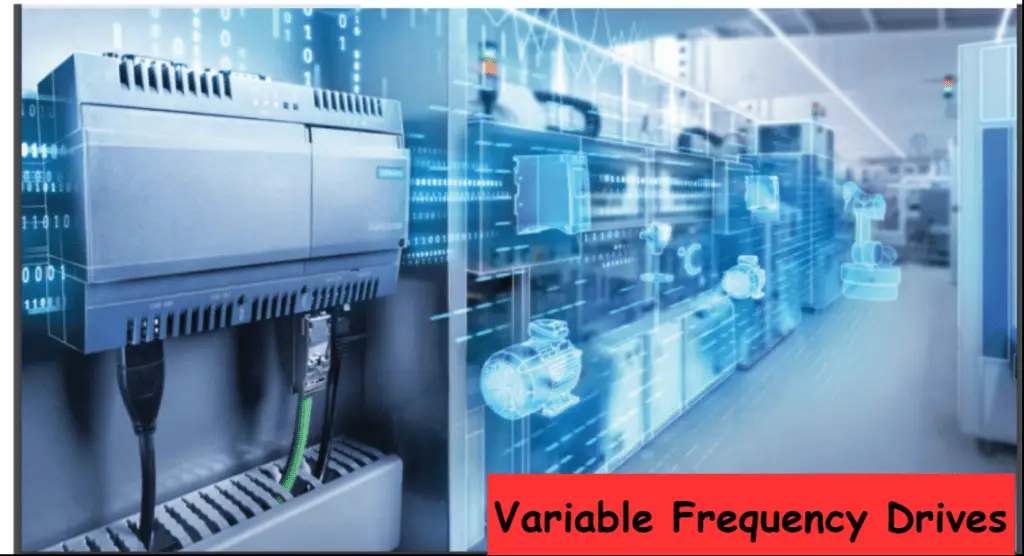
Preventive maintenance
Preventive maintenance is any planned maintenance carried out to deal with potential failures. It is based on estimates of useful life or expected time between failures(MTBF). It is based on the study of the service needs of VFD maintenance. Some of the maintenance activities do not require an expert, and the plant maintenance team can do its own. However, for special maintenance of VFDs, a maintenance crew or a supplier of equipment are the best agencies to do the maintenance.
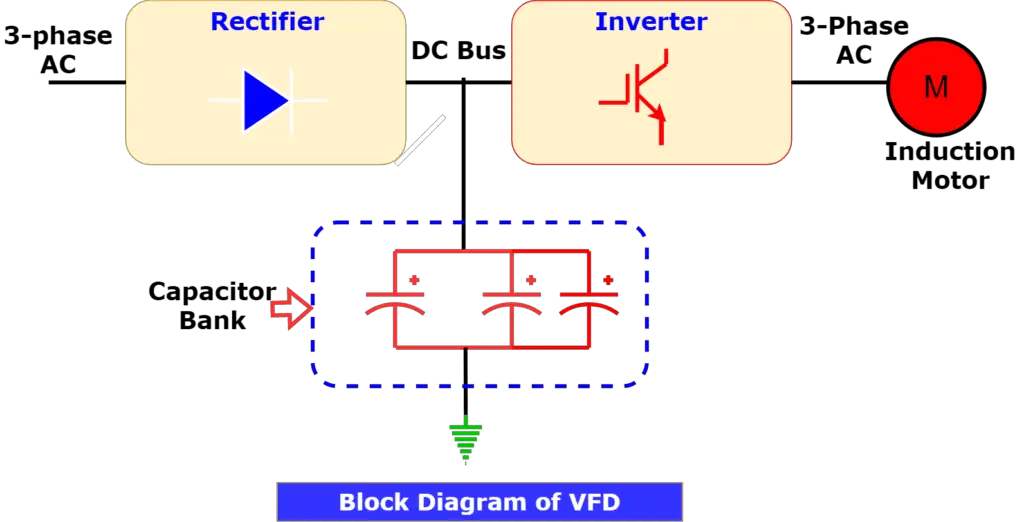
Before deciding on the preventive maintenance frequency and checkpoints it is absolutely necessary to find out the breakdown trends, and reliability trends of the VFD. Also, the supplier’s recommendations for equipment maintenance are vital points for maintenance. The mapping of the preventive maintenance schedule is the backbone for carrying out maintenance activities systematically.
Vital points in preventive maintenance of VFDs
- What should be inspected?
- How often should it be inspected and evaluated?
- To what should the service be given?
- What should preventative maintenance be done with?
- Which components be done with?
- Which components should be assigned useful life?
- What should be the useful and economic life of these components?
- Descriptive sheets of the operations to be carried out.
To determine the above points, one must take the following points into account
- Manufacturer’s recommendations
- Own experience (establish failure documents)
- Engineering analysis – a detailed study of the environment of facilities, and construction characteristics.
- Operation and the conditions in which operates – for which everything must be inspected.
Variable frequency drives (VFDs) have been designed to work in an industrial environment with large electromagnetic interference. Normally, good practices of installation ensure safe and trouble-free operation.
Attention to be paid
- Ensure that all equipment housed in a cabinet is properly grounded.
- Make sure that any control equipment (such as PLC) connected to the drive is linked to the same grounding point or star as the drive through a short, high-voltage link.
- Connect the ground of the motors controlled by the inverter directly to the ground connection of the associated drive.
Visual inspection
When performing a visual inspection, there are a few things to keep in mind. The first thing to do is to look for signs of condensation, corrosion, dust, and other foreign objects (insects). When these simple issues are caught early substantial repair costs can be saved.
Check the obstructions on the heatsink and fans that can hinder VFD’s cooling capacity.
In addition to checking the enclosure air filters for dust buildup, gaskets should also be inspected for deterioration and replaced if necessary.
Checking power connections
Heating and cooling cycles can loosen power connections. When the connections are loose, they can cause overheating, tripped branch circuit protection, and premature failures of VFDs. During the inspection, all power connections should be checked to ensure they meet the electrical requirements and torque specifications.
Preparation of VFD preventive maintenance schedule
The preventive maintenance of variable frequency drive(VFD) can be in three steps but differs from organization to organization based on local environmental conditions.
- Weekly Schedule
- Monthly Schedule
- Annual Schedule
Preventive maintenance usually compromises a series of characteristic activities. Periodic cleaning and inspections. Maintenance of equipment and protection. Good maintenance practices include visual inspection, regular cleaning, checking the tightness of connections and parts replacement are all excellent preventive maintenance practices.
One very important point generally a maintenance crew overlooks during vfd maintenance is retightening of electrical connections. The maintenance crew retightens the connections without having proof of connection looseness. We can find out the connection looseness by measuring the temperature at various connection points with an infrared thermometer when the drive is in running condition. If a temperature rise is observed, note down those connection points and retighten those connections only during preventive maintenance. Use torque wrench/screwdriver for correct connection tightening.
Weekly PM schedule
Over each week electrical maintenance personnel should be alert to unusual noises. At least once a week inspectors should create a report detailing the environment of the VFD. It includes the parameters such as temperature and humidity, VDC bus voltage and output voltage, current, and frequency.
Additionally, the report should document the monitored temperature of the VFD in order to provide long-term data on its health and maintenance requirements.
Monthly PM schedule
It is necessary to clean the filters every month. It includes corrosion filters, de-humidifiers, ventilation panels for VFD panels, and filters in storage cases for VFDs.
Annual PM Schedule
It is recommended that VFDs are cleaned, inspected, and maintained once per year. The use of water-based cleaning tools is not recommended for cleaning variable frequency drives (VFDs).
Inspection parts – it is necessary to tighten all the connections and terminal blocks. Check power supplies and refer to the parts replacement, preparation of schedule for any work to be carried out. It is recommended that well-trained professionals use an oscilloscope to check for ripple in the DC. The increased ripples in the DC show deterioration in the quality of electrolytic capacitors. Inspect DC bus capacitors for any bulging and leakage these replace the capacitors. The DC bus electrolytic capacitors’ life is about 7 years and they need to be replaced after completion of their useful life.
Check all the cooling fans and clean the fans for any jamming. The reliable operation of the fans is a vital criterion for enhancing the reliability of the VFD. Replace the fans after 3-4 years.
The 12-pulse VFD and MV VFD have a transformer connected to the drive. For these types of drives, a transformer is added parts and the regular maintenance of a transformer is a must.
Advantages of VFD preventive maintenance
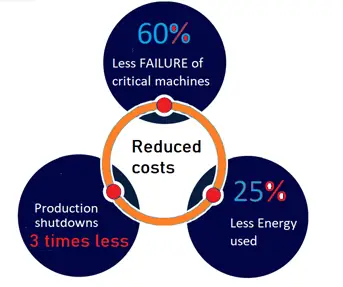
Many companies make the mistake of seeing preventive maintenance as an unnecessary added cost, understanding that it is only necessary to act when there is an incident to resolve. This attitude is wrong and entails great costs since if we do not act in time our ability to react to an incident will be much less. It will have a greater impact on the company’s productivity.