Distributed Temperature Sensing (DTS) is very useful for finding out the temperature profile of the transmission line. The abnormal temperature at any point of the transmission line points out the fault in the transmission line.
The temperature sensor installed at particular locations only shows the temperature of a particular location. Thus, the temperature sensor installed at the discrete location can not provide the temperature information of an entire transmission line. But, we need a temperature profile of the entire transmission line for determining the fault.
Therefore, the continuous monitoring of the temperature at every point of the transmission line is very important.
Distributed temperature sensing (DTS) is an advanced technology used for temperature measurement. It provides the temperature profile along the whole length of the transmission line. Thus, it facilitates the operator in finding transmission line faults.
What is Distributed Temperature Sensors?
Distributed temperature sensing (DTS) uses fiber optic sensor cables throughout the transmission line, lengths of several kilometers. The DTS is a linear temperature sensor that measures the temperature at every point of the transmission line. Thus, it is possible to get a continuous temperature profile along the entire length of the sensor cable.
DTS functions on the principle of the Raman effect to measure temperature.
RAMAN EFFECT
The change in the wavelength of light occurs when the molecules reflects the light beam. When a light beam traverses a dust-free, transparent sample of a chemical compound, a small fraction of the light reflects in directions other than that of the incident beam.
We call the DTS Technology as Raman OTDR or Raman OFDR (Optical Frequency Domain Reflectometry). Sir Chandrasekhara Venkata Raman (1888-1970), discovered that when light traverses a transparent material, some of the deflected light changes in wavelength. This ground-breaking work in the field of light scattering earned him the Nobel Prize for Physics.
Some other DTS technologies also use the Brillouin backscatter (B-OTDR or B-OTDA), which carries strain and temperature information. Such systems are also called DTSS (Distributed Temperature and Strain Sensing). The challenge with these systems is to isolate the fiber from strain to get accurate temperature information.
Scattering of Light
We can understand the scattering of light with the help of the below diagram.
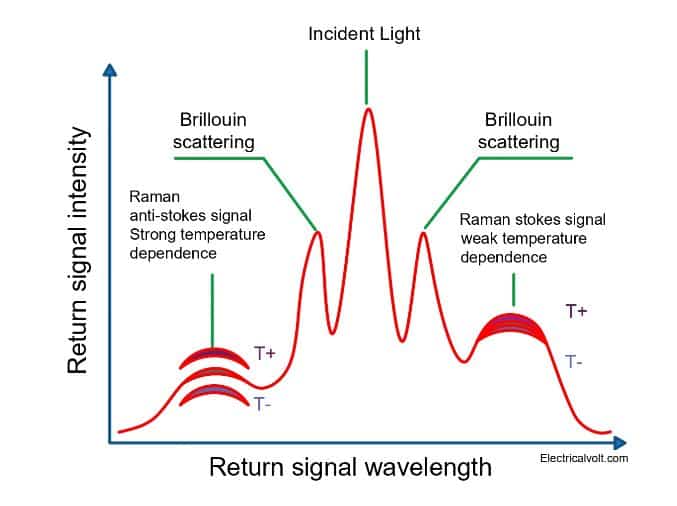
There are two types of signals according to Raman.
- The Raman stroke signal– This signal is almost a stable signal
- The Raman anti- stroke signal– This signal varies its amplitude with changing temperature
The amplitude and frequency increase for higher temperatures. On the other hand, the amplitude and frequency decrease for lower temperatures. The center grey color line shows the typical frequency of a light pulse in the cable. The peaks, Raman and Brillouin, show the temperature peaks of the light signal received.
Typically, at every 1 meter, the light scatters. For example, If the length of the transmission line is 100 km, there would be 100000 reflected pulses received at regular intervals at the receiver of DTS equipment.
Thus, it is possible to monitor the temperature of a larger coverage area of a transmission line or a cable.
The intensity of the Raman scattering shows the measurement of the temperature along with the fiber.
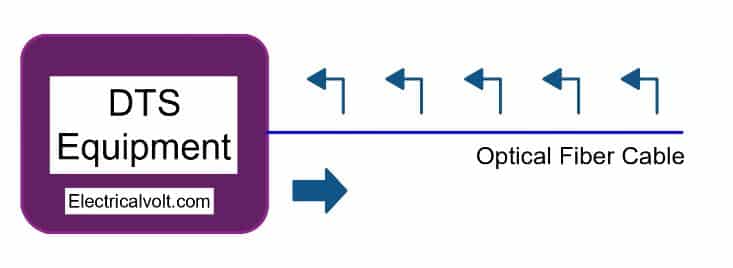
Distributed Temperature Sensing (DTS) System
Basically, the DTS system has;
- DTS transmitter-receiver
- Optical fiber cable laid throughout the transmission line
- PC software analyzer
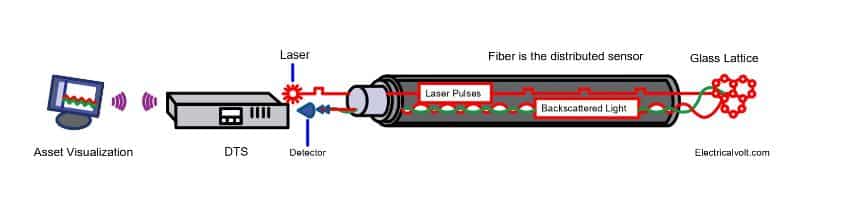
DTS transmitter-receiver sends an optical laser pulse through the fiber. The light scatters by the molecules & reflects back to the transmitting end. By analyzing the reflected light, the DTS calculates the temperature of the event (by analyzing the power of the reflected light) and also the location of the event (by measuring the time it takes the backscattered light to return) to typically within a meter.
Applications of DTS Sensors
DTS sensors are very useful and they have wide applications in industries.
Industrial Segments
- Oil and gas production—permanent downhole monitoring, coil tubing optical enabled deployed intervention systems, slackline optical cable deployed intervention systems.
- Power cable and transmission line monitoring
- Fire detection in tunnels- industrial conveyor belts and special hazard buildings
- Industrial induction furnace surveillance
- Integrity of liquid natural gas (LNG) carriers and terminals
- Leakage detection at dikes and dams
- Temperature monitoring in plant and process engineering, including transmission pipelines
- Storage tanks and vessels
Environmental Monitoring
- Stream temperature
- Groundwater source detection and sediment sourcing and deposition
- Temperature profiles in a mine shaft and over lakes and glaciers
- Deep rainforest ambient temperature at various foliage densities
- Temperature profiles in an underground mine,
- Temperature profiles in-ground loop heat exchangers (used for ground-coupled heating and cooling systems)
Advantages of Distributed Temperature Sensors
The followings are the advantages of the use of DTS.
- High Efficiency
- Reduced Complexity
- Easy installation
- Less costly
However, a special coating film must be coated on fiber cable to eliminate the environmental effects.
Read Next: