Spring and diaphragm pneumatic actuator has a diaphragm, spring, and stem as its main parts. The air pushes the diaphragm & spring compresses. Further, the spring compression cause displacement of the stem of the valve. The spring diaphragm pneumatic actuators have a widespread application in the industrial process.
Pneumatic actuators basically consist of a diaphragm, a stem, and a spring. On application of pressure on the diaphragm, the spring compresses. The spring compression cause actuator’s mechanism to move. Thus, the air pressure forces the spring to compress & drive the actuator.
Working Principle of Spring and Diaphragm Pneumatic Actuator :
The linear pneumatic diaphragm actuator is based on the principle that when the air supply signal pressure passes through the air chamber composed of the upper diaphragm cover and the diaphragm, make to move the push rod down as thrust is generated on the diaphragm and compress the spring.
When the spring force becomes equal to the thrust generated by the air supply signal pressure on the diaphragm, the pushrod stabilizes in a corresponding position. Thus, the pushrod expelled from the actuator cause displacement called a career.
Parts of Spring and Diaphragm Pneumatic Actuator :
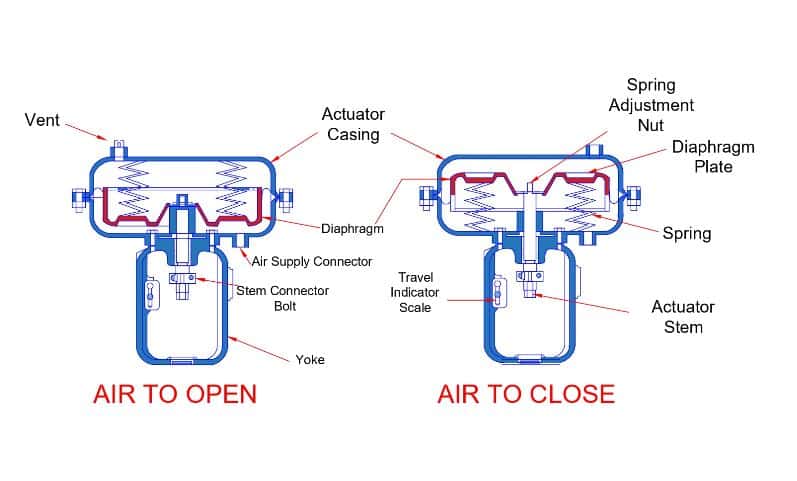
How does a Spring and Diaphragm Pneumatic Actuator work?
The spring and diaphragm actuator is so-called for the flexible diaphragm or membrane that separates two flattened concave chambers.
The spring and diaphragm type actuators are “air to expand” or “air to retract” type. If the valve is push-to-close type, the lowering of the stem by pneumatic signal causes the valve to close. If the valve is push-to-open type, the lowering of stem causes it to open on the application of a pneumatic signal.
At least one of the cavities is connected to a pressure line that operates the actuator. The pressurized air expands the diaphragm and drags the actuator shaft in a linear motion. If it is through the upper part of the diagram, the forces cause diaphragm deformation & which causes a downward displacement of the stem. On the other hand, if the air enters below the diagram, the movement will be upwards.
These actuators act against the spring pressure that is responsible for returning the diaphragm to its initial position when the diaphragm experiences no pressure.
Types of Spring and Diaphragm Pneumatic Actuator
1. Direct Acting( Spring to retract):
Most diaphragm actuators are of direct type. The upper chamber of the diaphragm receives the pressure, and the rod of the reducer moves downwards. In direct acting spring & diaphragm pneumatic actuators, the air pushes the diaphragm case downwards.
By applying a certain pressure on the diaphragm, the spring compresses in such a way that the stem begins to move. The stem keeps moving till the diaphragm pressure becomes equal to the spring pressure.
It will direct-acting when the air pressure acts in the upper chamber. Excessive pressure on the diaphragm can damage the diaphragm.
In air failure (or no air) the valve opens. Spring opens. Air to close. Direct action.
2. Reverse Acting (Spring to extend):
There are reversible diagram actuators, in which the air causes a movement of the rod downwards or upwards depending on the positioning of the actuator.
It is the lower chamber that receives the pressure, so the movement of the stem is upward. It is reverse acting when the air pressure acts in the lower chamber, causing the diaphragm to move upwards & stem to contract.
In air failure (or no air) the valve closes. Spring closes. Air to open. Reverse action.
The instrumentation engineer must also be aware of the following terms of the spring and diaphragm pneumatic actuator.
Maximum Case Pressure:
To achieve a full stroke, the maximum pressure can be applied to the actuator. If this stroke pressure exceeds before the upper diaphragm plate makes contact with the travel stop, it may cause damage to the stem or other parts.
Maximum Excess Pressure-Diaphragm:
If the pressure on the diaphragm exceeds above the rated pressure capacity of the diaphragm case when the actuator completes its full travel, the excess pressure may cause damage to the diaphragm & diaphragm casing.
Handwheel:
Spring and diaphragm valves may have Top-driven or side-driven handwheel for safe operation in case of air supply failure.
Materials:
Actuator Parts | Material |
Diaphragm Plate | Cast Aluminum, Cast Iron, steel. |
Stem | Steel |
Spring | Steel |
Read Next: