In this post, we will discuss what are LVDT and RVDT. LVDT is a short form for Linear Variable Differential Transducer. RVDT is the rotary variable differential transformer. These are electro-mechanical devices that consist of two components.
- A cylindrical hollow body contains two secondary identical winding positioned on both sides of the primary center winding.
- A cylindrical ferrite core freely moves longitudinally within the coil. The secondaries have series connection with phase opposition to one another.
How LVDT works?
In other words, LVDTs are moving core transformers. On application of an alternating excitation voltage signal to the primary winding, it generates a magnetic field. The magnetic field couples to the secondary winding through the ferrite moving core. As a result, voltages are induced in the secondaries.
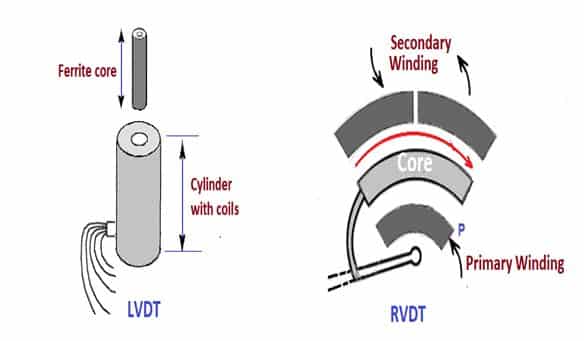
When the core between the two secondaries is in the center position, the voltages induced across both winding are equal. The final voltage is zero because both secondary windings are connected in series & in phase opposition.
If the core moves in the direction of secondary-1, the voltage increases in secondary-1, and the voltage decrease in secondary-2. Similarly, If the core moves in the direction of secondary 2, the voltage increases in secondary-2, and the voltage decrease in secondary-1.
Thus the final net voltage VA-VB is of the same polarity (in-phase) as the reference. If the nucleus moves in the direction opposite, VA-VB will be of opposite polarity (180º out of phase).
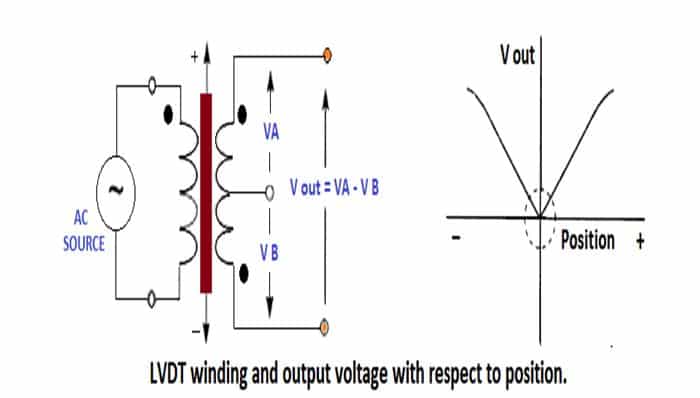
Therefore, as the ferrite core moves along its axes within the LVDT, the voltage the output starts with one polarity, decreases completely to zero. later increases with opposite polarity, all in a continuous and smooth way.
LVDTs give a linear output voltage signal around zero (within the ± 0.25% over a specified linear range of travel).
For a typical LVDT selection, the linear range nominal can be from ± 0.05 inches to ± 10 inches, with the body corresponding to lengths from 1 inch up to 30 inches.
LVDTs are rugged and accurate, and they produce low-voltage outputs. (the Sensors – Conditioners – Processors sensitivity is between 6.3 and 0.08 mV per volt of excitation per millimeter of displacement) and therefore they need a lot of care, attention when doing amplification.
RVDT Construction
RVDT stands for Rotary Variable Differential Transformer, its construction is similar to linear variable differential transducer (LVDT) except that ferrite core movement is circular in the body.
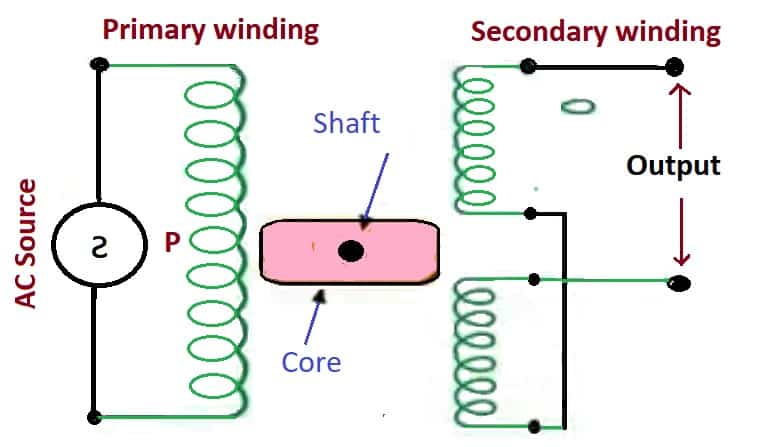
How RVDT work?
While LVDTs measure linear displacement, RVDTs measure angular displacement. The maximum angular position measurement range is approximately ± 60º.
When RVDTs work in the range of ± 40º, the typical device has a linearity error of 0.2% of full scale. If we keep the displacement angularity within ± 5º, the linearity error reduces below 0.1% of full scale. The shaft is supported by ball bearings that minimize friction and mechanical hysteresis.
LVDT Signal Conditioning
Most of the tasks of an LVDT signal conditioner are dedicated to transforming the two a.c. signals. 180º out of phase at a simple d.c. voltage.
It represents the longitudinal position. Therefore, some form of demodulation to condition the a.c. conversion to d.c. The most common mode used for conditioning the LVDT signal is the synchronous demodulation technique.
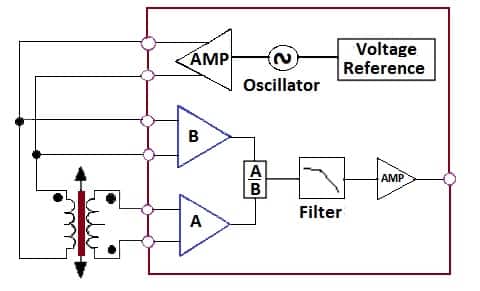
In synchronous demodulation, the excitation of the primary serves as the reference for the demodulator. The demodulator half-wave rectifies the a.c. the signal then is low-pass filtered to produce a d.c output. Whose magnitude shows the movement (position) away from the central position and whose sign indicates the direction.
The LVDT signal conversion method uses a large number of discrete components and built-in, as shown below, where you have four sections: Oscillator / Driver, Drive Amplifier, input, demodulator, and low-pass filter. With the introduction of signal conditioning devices, Analog Devices supports the signal conditioning applications of LVDTs.
Applications
- We use LVDT and RVDT transducers in measurement and control applications for measuring displacement from micro inches to several feet.
- LVDT & RVDT have many applications in metrology systems, in valve positions, in hydraulic actuators. Other applications of these transducers, such as load, pressure sensors using LVDT internally.
- We use LVDT & RVDT in Brake with cable systems,Engines bleed air-systems, Aircraft and Avionics,Process Control industry,Engine fuel control,Ecological control systems;etc.
Good article,