The main difference between VFD and Soft Starter is that a VFD can increase or decrease the speed of the motor, while a soft starter only controls the smooth start and stop of that motor. The soft starter is an electronic device used for starting and stopping the induction motor smoothly. The soft starter is a kind of reduced voltage starter. The soft starter starts and stops an induction motor without any jerk. An induction Motor takes a high current of about 5-7 times current of its full load current when we start the motor through a direct online starter(DOL).
Table of contents
At the start, the motor generates heavy torque. As a result, the motor creates electro-mechanical stress on the power system. In addition to this, it creates mechanical stress on the motor and driven equipment as well. Even if we feed 58.7 % of line voltage through the star delta starter, the motor takes a high current. Though the current on star-delta start is less than the current on DOL start, still the current is high.
Disadvantages of DOL or star delta starter Compared to Soft Starter
- High starting current causes electrical and mechanical stress on the power system.
- High starting current causes mechanical stress on the motor and driven mechanical equipment
Contrary to DOL and Star-Delta starter, the soft starter increases the output voltage gradually at the start. The gradual increase of voltage limits the high starting current and torque. Thus, the driven equipment does not experience mechanical stress.
Similarly, during the stopping of the motor, the soft starter decreases the voltage gradually in a ramp-down manner. This results in, the driven equipment gets soft stopped.
Advantages of soft starter Compared to DOL Starter
- Reduced mechanical stress on the motor and driven equipment
- Reduced electro-mechanical stress on the power system
- Increased life of the equipment
The soft starter is most suitable for jerk-less starting and stopping of the induction motor. However, we can not use the soft starter for speed regulation of the induction motor. On the other hand, VFD is used to control the motor speed from zero to its base speed. This is the major difference between soft starter and VFD.
Disadvantages of soft starter Compared to VFD
The soft starter is suitable for jerk-less starting and stopping of an induction motor, however, we can not use it for speed control of the motor.
Let us understand the working principle of soft starter and VFD for understanding the difference between soft starter and VFD.
Working Principle of Soft Starter
We will first discuss the working of the soft starter to have a better understanding. This will ease the understanding about what is the difference between a soft starter and a VFD. The power diagram of soft starter is as given below. The soft starter has the anti-parallel SCR in each phase.
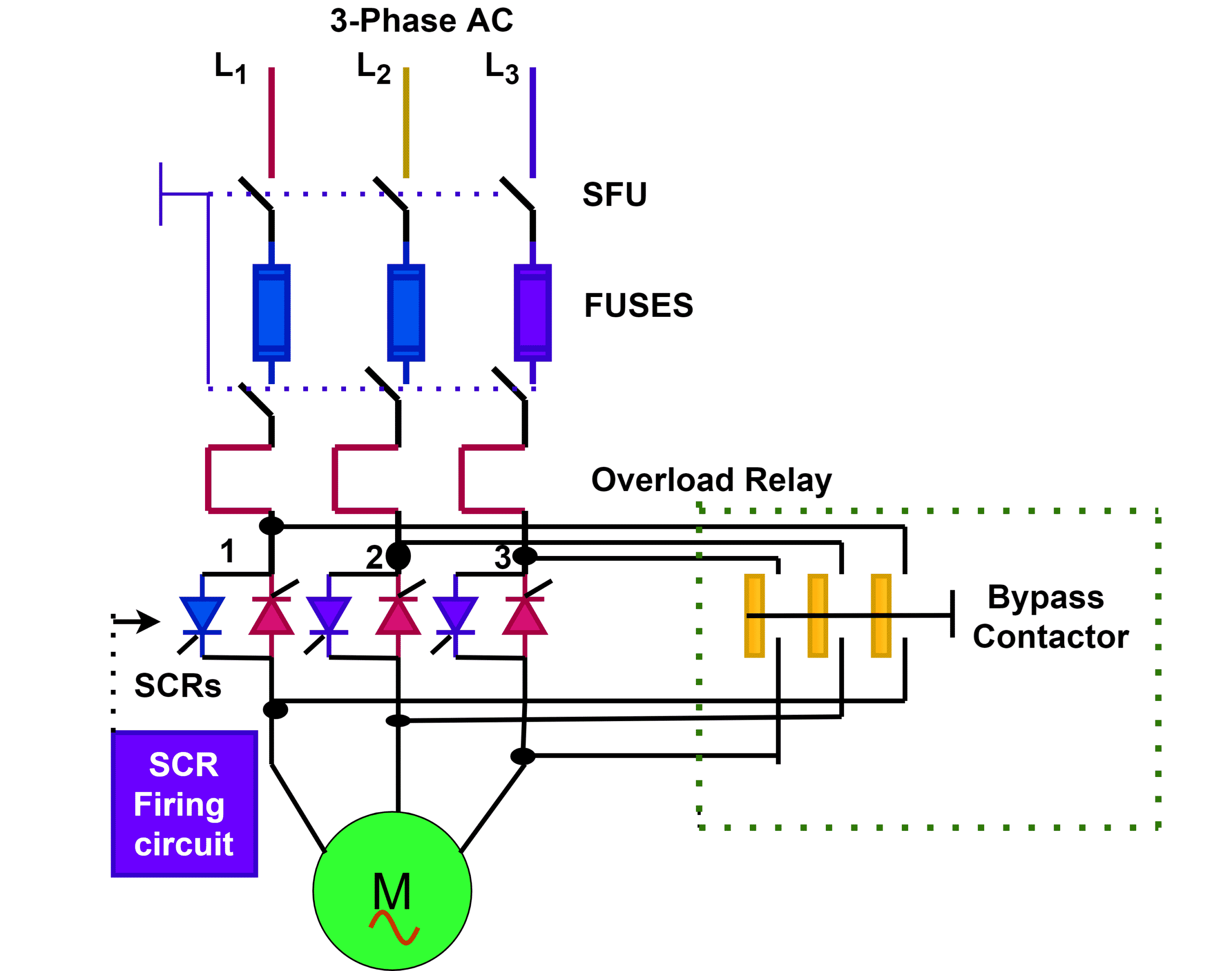
We can control the output voltage of each phase by varying the firing angle of silicon controlled rectifiers (SCRs). The output voltage increase with a decrease in the firing angle.
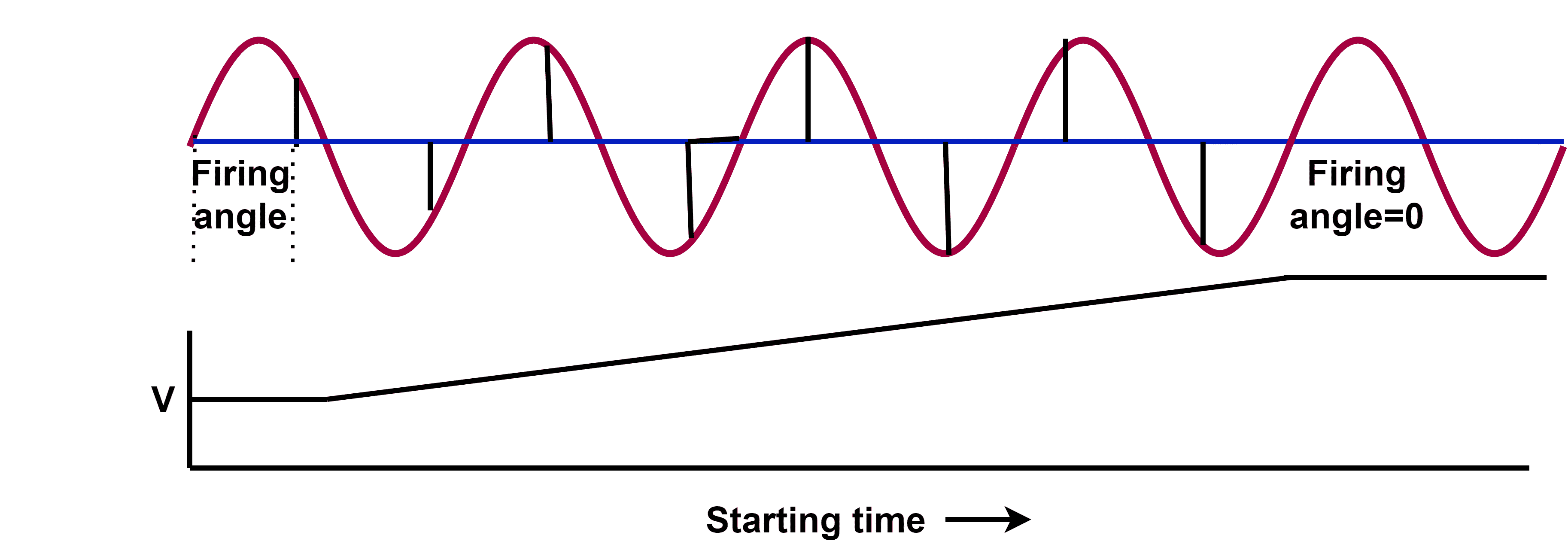
When full line voltage reaches, the soft starter controller switches on the bypass contactor. As a result, the motor gets pure sinusoidal voltage. Again at the time of stopping, the soft starter controller shifts the system from run contactor (bypass contactor) to soft starter mode for smooth stopping of the motor.
Soft starter controls the voltage only, the frequency does not change with change in voltage.
Disadvantages of Soft starter
The soft starter is used where speed control of an induction motor is not required. The soft starter does not maintain the constant v/f ratio, and hence the flux is less than the rated flux capacity of the motor. The torque delivering capacity of the motor depends on the flux. Thus soft starter is not suitable for those applications which demand a higher starting torque.
Soft starters are used for the motors which almost start on no-load- ( coupled equipment demands very low torque at the start) Example – Air Compressor. In other words, it is not possible to drive the loads which demand higher starting torque.
General Misconception about Soft Starter
Someone believes that if we run the motor through a soft starter, the motor draws less starting current and driven equipment runs smoothly and jerk-less. However, the starting current depends on the type of load driven by the soft starter. The starting torque delivery of the motor with a soft starter is very low than its rated capacity. The motor draws a large current for starting of high inertial loads. Also, the motor produces very low starting torque. Under this condition, the motor may stall.
Therefore, before selecting the soft starter for the motor, we must check the speed-torque characteristics of driven equipment.
Variable Frequency Drive (VFD)
We use VFD for:
- Speed control of induction motor
- Jerk-less starting and stopping of induction motor
The speed of an induction motor is proportional to the frequency and number of poles. We can calculate the speed of an induction motor using the following formula.
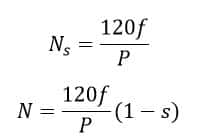
The flux of the motor is proportional to the ratio of voltage and frequency. Therefore, for maintaining the constant flux in the motor along with speed control, the VFD maintains the V/f ratio constant. The PWM inverter maintains the V/f ratio constant by simultaneously increasing or decreasing the frequency and voltage. Whereas the soft starter does not maintain the constant V/f ratio, and flux in the motor is not constant. This is one of the major differences between soft starter and VFD.
Block Diagram of VFD
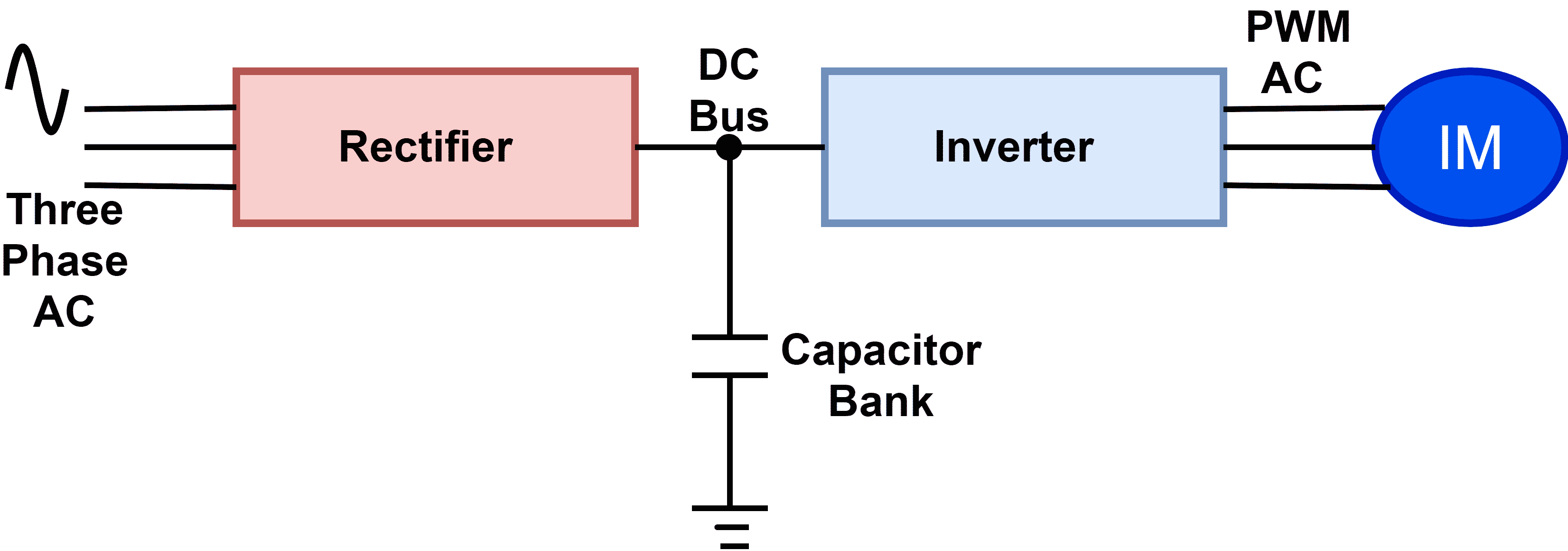
The VFD has three major sections.
- Converter Section
- DC Bus
- Inverter Section
Converter section
The converter or rectifier section has six diodes. The diodes rectify the AC voltage into DC voltage. The magnitude of the DC voltage is;
Vdc = 1.35 X Vrms
DC Bus
The rectified voltage contains ripples in it. Capacitor bank filters the AC components and produces ripple-free DC voltage.
Inverter Section
The inverter converts DC voltage into AC through PWM process. The inverter controls both frequency and voltage simultaneously to maintains the v/f ratio constant.
Summary- Major difference between Soft Starter and VFD
- The soft starter controls the voltage only, the frequency always remains unchanged. VFD changes the voltage and frequency simultaneously to maintain the constant flux in the stator air gap length. This is the major technical difference between soft starter and VFD.
- We use soft starter for soft starting and stopping the motor. The VFD also soft starts and soft stops the motor. The main purpose of the VFD is to control the speed of the motor coupled with energy-saving and smooth process control. We can achieve tremendous power saving in fan and pump applications with the use of VFD because power drawn by pumps and fans is proportional to the cubic of the speed.
- The soft starter is cheaper than VFD.
- A soft starter is suitable for low starting torque demanding equipment. Contrary to this, the motor-driven by VFD can deliver the rated starting torque, and even more than the rated torque for a definite time through enabling the torque boosting feature of VFD.
- Soft starter injects harmonics in the system at the time of acceleration of the motor only. After reaching base speed, soft starter switches on the bypass contractor, and thus, the motor gets a cleaner sinusoidal supply. VFD continuously remains in the circuit, and as a result, injects harmonics into the system. Moreover, the motor gets PWM wave which is not the pure sinusoidal supply. The harmonics impact the motor performance in many ways.
Related Posts:
- Why V/F Ratio Is Kept Constant in VFD?
- Direct Online Starter (DOL Motor Starter) : Circuit Diagram and Working Principle
- Star Delta Starter | Working Principle, Power and Control Circuit Diagram
- Why Induction Motor Takes High Starting Current?
- Harmonics and Harmonic Frequency in AC Circuits
- Working Principle of VFD
- Thyristor Protections
2 thoughts on “What is the Difference between Soft Starter and VFD?”