What is a Dry Type Transformer?
A dry-type transformer does not use any liquid for its cooling and insulation. An oil-filled transformer uses mineral insulating oil for its cooling and insulation. For cooling of dry type transformer, the air is forced into the cabinet of the transformer. Many transformers are cooled with oil or a fire-resistant dielectric. This requires regular maintenance and continuous monitoring of oil. However, dry-type transformers do not use oil and thus require very less maintenance.
Table of contents
Types of Dry Type Transformers
There are two types of dry-type transformers. They are
- Cast Resin Dry Type Transformer (CRT)
- Vacuum pressure Impregnated Transformer (VPI)
Cast Resin Dry Type Transformer (CRT)
The primary and secondary of the transformer are encapsulated with epoxy resin. This encapsulation of the winding prevents the possibility of penetration of the moisture in the winding. Thus, a Cast resin dry type transformer (CRT) can be safely used in the high moisture-prone areas.
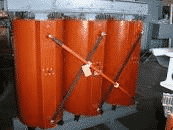
This type of transformer has the following advantages. They are-
- High short-time overload capacity.
- Lower load losses and higher efficiency
- No use of oil – Zero risk of fire hazard make it suitable for indoor installation.
- Can be fitted outdoor in IP 45 enclosure.
- Does not absorb moisture- non-hygroscopic.
- Eco-friendly and safe
Vacuum Pressure Impregnated Transformer (VPI)
In a vacuum impregnated transformer the primary and secondary winding is impregnated with resin within a vacuum chamber. The winding is made in the form of foil or strip. For higher voltage applications the winding is made in the form of a disc.
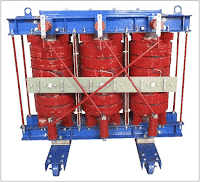
The winding can be physically seen by opening the door of the transformer. But in a CRT dry type transformer, the primary and secondary winding is molded. The winding of the CRT dry type transformer becomes a solid mass after mold casting. Thus opening the door of the transformer one can see three molds for three different limbs of the transformer.
VPI gives a chance for the repair of the winding in case there is some winding fault but CRT is a solid mass and can not be repaired. CRT has higher mechanical rigidity than VPI which gives a higher short circuit withstand capability. The insulation of the winding is of grades F(155˚C) and H(180˚C). This type of transformer is available from 5KVA to 30MVA ratings.
This type of transformer has the following advantages.
- High mechanical strength.
- Void-free insulation.
- No temperature fluctuation.
- Easy maintenance.
- Less prone to fire hazards.
Advantages of Dry Type Transformer
The main advantages of a dry-type transformer are as follows.
- Safety for people and property.
- Maintenance and pollution-free solution.
- Easy maintenance
- Side clearance is less.
- Environmentally friendly.
- Excellent capacity to support overloads.
- Reduced cost on civil installation works and fire protection systems.
- Excellent performance in the case of seismic events.
- No fire hazard.
- Excellent resistance to short circuit currents.
- Long-lasting due to low thermal and dielectric heating.
- Suited for damp and contaminated areas.
Disadvantages of Dry Type Transformer
There are some disadvantages of a dry-type transformer. They are-
- The dry-type transformer is long-lasting and with less chance of winding failure. But once it fails the whole setup is to change, i.e. complete change of high voltage and low voltage winding with the limb.
- For the same power and voltage rating, a dry-type transformer is costlier than an oil-cooled transformer.
Application of Dry Type Transformer
Dry-type transformer is widely used in-
- Chemical, oil, and gas industry
- Environmentally sensitive areas (e.g. water protection areas)
- Fire-risk areas (e.g. forests)
- Inner-city substations
- Indoor and underground substations
- Renewable generation (e.g. off-shore wind turbines )
Important Factors to Design a Dry Type Transformers
The important design parameters for a dry-type transformer are given below.
1. Choice of Insulation Type
The insulation classes F and H have temperature withstand capacities of 155˚C and 180˚C respectively, and generally, F and H classes of insulation are used to insulate the primary and secondary winding. The other factors like mechanical strength, thermal shock, and dielectric strength of insulation must be considered while designing the dry-type transformer.
2. Selection of Winding Material
Copper and aluminum are used used to make the winding or coil. Even though copper is a better conductor, the aluminum conductor wound transformer has lower cost and weight. The transformer winding with a copper conductor has less cross-section area for the same current rating as compared to the aluminum conductor. The copper coils also provide more mechanical strength compared to the aluminum coil.
3. Selection of Core Material of Low Hysteresis Loss
The core of the transformer must have high permeability and less hysteresis loss in order to have better efficiency. The CRGO steel is used for the core material. The CRGO steel offers higher permeability and minimum hysteresis loss.
4. Regulation

The leakage reactance of the transformer must be as minimum as possible to get better voltage regulation of the transformer. The regulation of the transformer shows drops in the secondary voltage with an increase in loading on the transformer. The leakage reactance is generally kept within 2 % during transformer design.
5. Life Expectancy
The life of the transformer depends upon the useful life of the insulation. The life of the insulation is dependent on the temperature. The rise in temperature cause deterioration in the insulation value which may further cause the breakdown of the insulation. Insulation class B, F, and H is preferred for the dry-type transformer to withstand higher temperature. The temperature rise must be calculated during the design stage of the transformer to get a higher life expectancy of the transformer.
6. Losses
The no-load losses of the transformer depend on the eddy current and hysteresis loss. The no-load losses can be minimized by the use of the CRGO core and by keeping the leakage reactance as minimum as possible. The load losses depend on the resistance of the conductor. Thus, by keeping the winding resistance within moderate value losses, voltage regulation and the efficiency of the transformer can be improved.
7. Overloading
If the load on the transformer increases above its rated kVA, the transformer is said to be overloaded. The overloading cause rise in the temperature of the transformer which reduces the useful life of the transformer. The cooling system should be designed to cater to the temporary overloading of the transformer
8. K-factor
If the dry type transformer is to be used for supplying the current to non-linear loads the temperature rise takes place due to harmonics in the current waveform. The transformer for such applications must be assigned K-factor.
9. Insulation Level
In transformer design, insulation level adjustment is an important factor. Generally, insulation level is chosen as per basic impulse level and system overvoltage. A strong insulation level increases the life of a transformer.
Read Next:
1 thought on “Dry Type Transformers: Types and Applications”