Double Cage Rotor Induction Motor provides high starting torque and low starting current. In this post, we will discuss the construction, operation, and characteristics of the cage rotor induction motor.
The squirrel cage induction motor is widely used because of its simple construction and long, trouble-free operation. Also, the squirrel cage induction motor requires very little maintenance, and it has high reliability. On the other hand, the squirrel cage induction motor lacks in delivering the high starting torque. The application that demands high starting torque can’t be started with a squirrel cage induction motor. The deep bar double cage induction motor is used for applications that demand higher starting torque.
The slip ring induction motor can be used to drive the high inertia loads that demand high starting torque. However, the slip ring motor requires more maintenance because it has more parts like slip rings, carbon brushes, and external resistances.
One more solution for the production of high starting torque is the use of a double-cage squirrel cage induction motor. The double cage induction motor is a modified version of a squirrel cage induction motor, and it is used for applications that demand high starting torque. In the subsequent sections, we will discuss how the double-cage induction motor produces more starting torque.
The torque equation of the induction motor is given by,

At start, slip is equal to unity; hence, starting torque is given by,
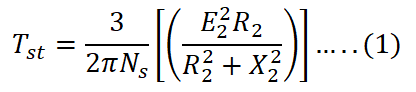
Where,
R2 = Rotor Resistance
X2 = Rotor Reactance
E2 = Rotor Induced Voltage
Ns= Synchronous Speed
From equation(1), it is clear that the starting torque of the induction motor is proportional to the rotor resistance R2 and inversely proportional to the rotor reactance(X2). The rotor resistance of the squirrel cage induction motor is kept low to increase the motor’s efficiency by reducing the copper loss.
At start, the slip of the motor is unity, and the rotor supply frequency is;
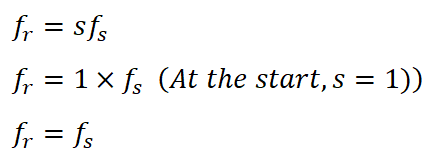
The rotor reactance is slip dependent, and at start, the rotor reactance is;
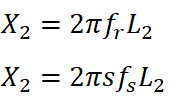
At the start, the rotor reactance is very high because slip=1.
Therefore, the starting torque of the squirrel cage induction motor is low because, at the start, the motor has high rotor reactance. The rotor resistance of the squirrel cage induction motor is low throughout its speed range. For these reasons, the squirrel cage induction motor has a low starting torque.
Incorporating a double-bar double cage in the rotor circuit increases the rotor resistance of a squirrel cage induction motor to increase the starting torque of the motor.
Construction of Double Cage Rotor Induction Motor
The construction of the double cage induction motor is shown below.
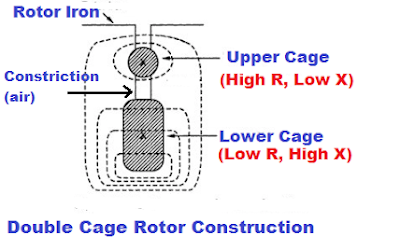
The double-cage induction motor has two cages in the rotor circuit for increasing the starting torque. The rotor of the squirrel cage induction motor has two winding in the rotor. The outer cage has rotor bars of high resistance and low reactance. The inner cage has rotor bars of low resistance and high reactance. The end rings short-circuit each rotor bar.
The outer cage bars are made of high-resistivity materials like aluminum, brass, bronze, etc. Their cross-section area is less than that of the inner cage bars. Therefore, the outer cage bars have more resistance than the inner cage bars. The resistance of the outer cage bars is about 5-6 times the resistance of the inner cage bars. Therefore, the deep bar double cage induction motor produces more starting torque.
The leakage flux linking to the outer and inner cage bars depends on the dimension of the air constriction. Air constriction is vital in the flux linking the outer and inner cage bars. In case of air constriction absence, the flux finds its path through the iron part of the rotor and does not reach the inner cage bars of the motor, and the inner cage bars will not contribute to torque production.
Working Principle
At the start, the frequency of the rotor-induced voltage is equal to the stator frequency(fr=fs as slip=1 at start). The high-frequency rotor current flows through the outer cage bars due to the skin effect and low leakage reactance. The inner cage bars have more reactance than the outer cage bars reactance. The conductor arrangement in the inner and outer cage of the rotor is as shown below.
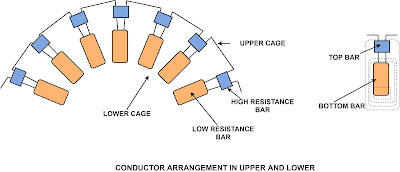
The equivalent circuit of the deep bar double cage induction motor is shown below.
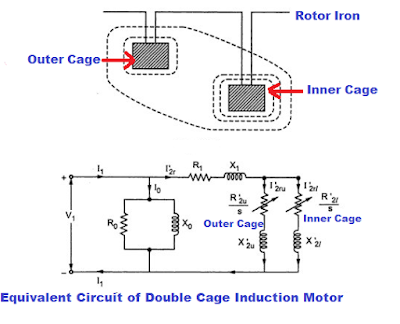
Thus, the inner cage impedes the rotor current when the rotor frequency is higher. So, most of the current will find its path through the low-impedance outer cage bars.
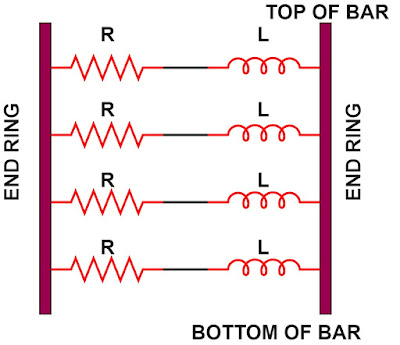
The resistance of the outer cage bars is more than that of the inner cage. Therefore, the Deep Bar Double Cage Induction Motor develops high starting torque.
The rotor frequency decreases with the acceleration of the motor towards its base speed. The frequency of rotor-induced voltage and current depends on the motor’s slip. The slip decreases with an increase in motor speed. The slip at the start is equal to unity, and the slip becomes much less at regular motor running. The rotor frequency becomes very low after the motor attains its full-rated speed.
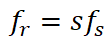
The relationship between the rotor frequency and the slip is shown in the graph below.
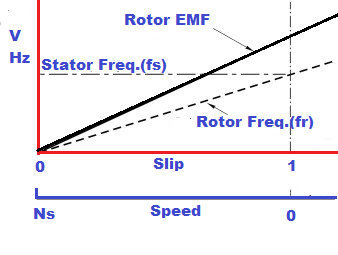
The impedance of the inner cage bars gets reduced when the motor attains its full speed. At the start, most of the rotor current flows through the outer cage bars. When the motor accelerates, the current shifts from the outer cage bars to the inner cage bars. When the motor attains full speed, the maximum current flows through the inner cage bars.
Speed Torque Characteristics of Double Cage Induction Motor
The speed torque characteristics of the double cage induction motor are shown below.
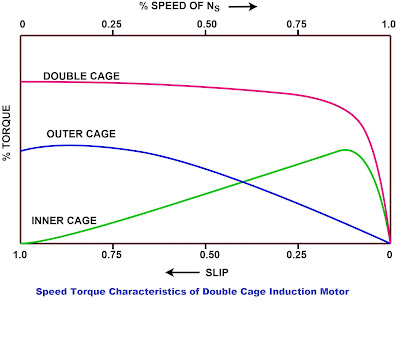
When a double cage induction motor is switched on, most of the current flows through the outer cage bars, and as the outer cage bars offer low impedance, the motor’s torque improves. At the start, the outer cage bars produce more torque than the inner cage bars. If the torque produced by inner and outer cage bars are added, the total torque produced by a double cage motor is much more than that produced by a single cage motor.
With an acceleration of the motor, the impedance of the inner cage bars starts decreasing, and the motor current starts shifting from the outer cage bars to the inner cage bars. The division of the current in the outer cage and inner cage bars is inversely proportional to their leakage impedance. The motor almost behaves as a single cage motor when it attains its full-rated speed.
Difference between Single Cage and Double Cage Induction Motor
The difference between single-cage and double-cage induction motors is tabulated in the below table.
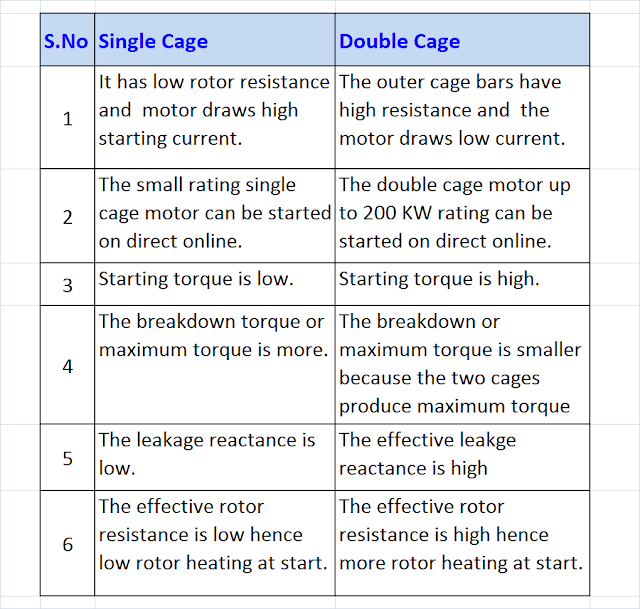