The back EMF momentarily opposes the armature voltage when the speed of the DC motor is changed, and thus, it limits the armature current.
What is Back EMF in a DC Motor?
When the DC voltage is applied to the armature of the DC motor, the motor draws an enormously high current at the start, and it decreases as the motor accelerates. Why the DC motor draws a high armature current at the start and how the current gets decreased as the motor accelerates is because of the counter-potential force developed across the armature winding. The counter voltage induced across the armature winding is called the back EMF.
The diagram of the separately excited DC motor is given below.
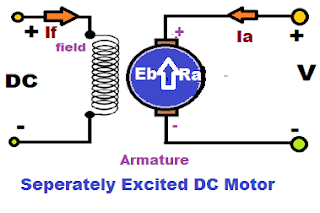
The DC motor has two main parts- the armature and the field winding. The field current flowing in the field coil generates the flux in the motor. The flux gets linked to the armature conductor. When the motor armature(A rotating part) is stationary, the flux of constant magnitude linked to the armature conductor does not produce the voltage in the armature conductor. Therefore, the back EMF is zero when the motor starts. When the motor starts accelerating, the back EMF starts developing across the armature winding. The induced EMF opposes the applied voltage according to Lenz’s law.
The magnitude of the back or counter EMF depends on the following;
- The field flux
- The Speed of the motor
- No. of conductors in the armature winding
The back EMF formula is given below.
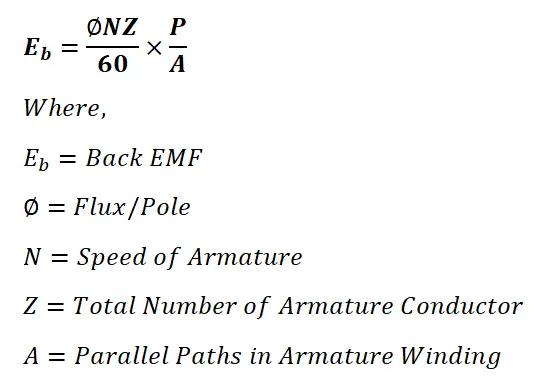
The counter EMF is proportional to the speed of the motor.


At the start, when N=0, Eb=0, the motor draws a very high armature current. Due to an interaction of the field flux and the armature current, the torque is produced.
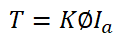
The torque is exerted on the armature, and the motor starts accelerating. The back EMF starts to develop as the motor accelerates because the back EMF is proportional to the speed of the motor. The magnitude of the counter EMF is always less than the applied DC voltage because of the IaRa drop in the armature.
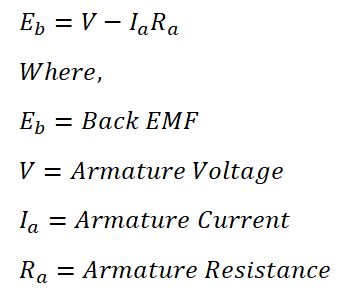
Significance Of Back EMF
Back EMF regulates the armature current and, as a result, the armature current automatically maintains the load requirement. Let us understand how the Back EMF regulates the armature current.
How does Back EMF regulate the flow of armature current?
Case 1: When the applied armature voltage is increased
The back EMF limits the armature current and makes the motor self-regulating. If the applied voltage is increased, the armature current increases momentarily, and the speed of the motor increases. The increased speed of the motor increases the back EMF, and the armature current gets reduced.
Case 2: When the speed of the DC motor gets decreased
If the speed of the motor decreases because of the increased loading, the driving torque becomes less than the load torque, the motor slows down, and the back EMF decreases. A decrease in back EMF allows more armature current to flow through the armature winding.
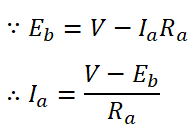
The increased armature current will produce more torque, producing the torque required by the load. When the motor attains the normal speed, the back EMF increases, causing a reduction in the armature current. Thus, the self-regulation of the armature current is achieved.
Case 3: When the speed of the DC motor gets increased
If the load on the motor is decreased, the driving torque becomes more than the load torque. The motor speed increases and the increased speed causes an increase in the back EMF that opposes the applied DC voltage, and as a result, the armature current decreases. The motor stops accelerating, and the speed returns to the point that meets the exact load requirement.
Thus, the back EMF regulates the armature current according to the load requirement.
Read Next: