Induction Motor Braking Methods
There are many ways of applying the brake to the induction motor. The DC injection braking is a sort of dynamic braking. The DC injection braking can be applied by injecting the direct current in the stator of the motor after switching off the AC supply.
The various braking methods of induction motors are as follows.
- Dynamic braking
- Regenerative braking – (1) Rheostatic braking (2) DC Injection braking
- Plugging
Why is Braking required?
After switching off the AC supply, the motor keeps rotating for a definite period before attaining the standstill position. However, In case of an emergency and for some applications where coasting time is unacceptable, the motor must be stopped immediately to a standstill position. The DC injection, Rheostatic, regenerative, and plugging braking are the methods of braking used to bring the motor to stop immediately.
We will confine our discussion to DC injection braking in this article.
DC Injection Braking Theory
When the AC supply is disconnected from the stationary stator, the DC supply is fed to the stator winding. The DC supply produces a magnetic field that travels through the air gap and links to the rotor conductors. As the rotor is rotating at the moment of switching off the AC supply, the voltage induced in the rotor conductor leads the flow of electric current through the short-circuited conductors of the rotor.
The stator winding connected in a different configuration with a DC supply produces the magnetic field for braking torque. The magnitude of the torque depends on the magnitude of DC and the stator winding configuration.
The speed of the rotor is more than the synchronous speed at the time of stopping the motor. In this condition, the motor works as a generator. During generation mode, the kinetic energy of the motor converts into electrical energy, dissipating heat energy in the rotor conductors. The conversion and dissipation of electrical energy in heat energy produce braking torque in the motor, which stops quickly.
Circuit Diagram of DC injection braking
Circuit Description
The bridge rectifier converts AC voltage into DC. When we switch off the motor or the motor trips with fault, the changeover switch changes its position from AC source to DC source. The stator winding of the motor now receives a DC supply. We can select the number of windings receiving the DC by selecting one, two, or all the windings. We select all the winding to produce more braking torque.
Braking Torque
The induction motor can operate in three operations, i.e., Motoring, generating, and braking. The speed torque curve of the induction motor operating in these zones is given below.
The slip of the induction motor is more than 1 during the braking of the motor. With dynamic braking through DC injection in the motor’s stator, the torque depends on the magnitude of the DC. The higher DC voltage produces stronger braking torque.
The DC should be applied for a few seconds. The DC current produces the heating effect I2R in the rotor winding. The heating of the coil must be below its rated heat rating. Otherwise, the winding is apt to fail. The DC voltage applied for a longer period may cause winding to overheat and finally cause winding burnout.
DC Injection Braking in VFD
The variable frequency drives are very popular, and we use VFDs for industrial and domestic applications. The VFD has the inbuilt function of producing output DC voltage. The DC voltage can create the braking torque, and it is possible to stop the motor immediately. The block diagram of the VFD is given below.
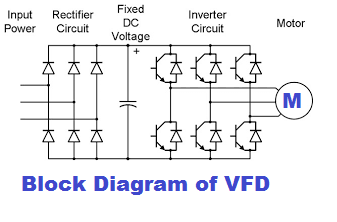
During DC injection, the inverter operation does not function, and switching the IGBTs on and off causes DC injection in the stator winding.
Parameters setting in VFD for DC Injection Braking
It is very easy to activate the DC injection braking in VFD. We set the following parameters in VFD for DC injection braking.
DC Injection start frequency
Set the frequency at which DC injection starts when ramp to stop is selected.
DC Injection braking current
Set the DC injection braking current as a percentage of the drive-rated current.
DC Injection braking Time at start
Set the time of DC injection braking
DC Injection braking Time at stop
Set the time length of DC injection at the stop
The above parameters are shown in the below graph.
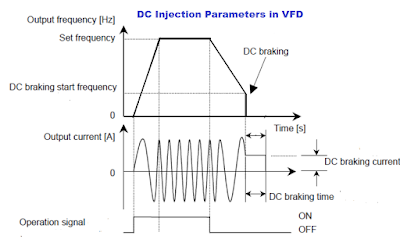