VVVF( Variable voltage variable frequency) control is used to control the speed of the induction motor. The VVVF drive controls the voltage and frequency simultaneously to control the speed of the induction motor. Therefore, it is called variable voltage variable frequency drive (VVVF drive). The VVVF full form is variable voltage variable frequency.
In VVVF drive, the V/f ratio is kept constant to maintain the rated flux in the motor. The higher V/f ratio causes the motor’s core to overheat and, eventually, the motor failure.
The VVVF drive is also called VFD. The VFD full form is a variable frequency drive.
Let us first discuss the motor’s speed control method through VFD to understand the effect of the V/f ratio on the induction motor.
Speed of Induction Motor
VFD stands for variable frequency drive. A VFD or VVVF drive is used with an induction motor to control speed, optimize processes, and save energy.
Before understanding why the V/f ratio is kept constant in the VVVF drive, we first understand the working of the induction motor. V/f control is also called V/Hz control or scalar control.
The difference between synchronous speed and the motor’s speed is called slip. The speed of the induction motor can be calculated with the following formula.
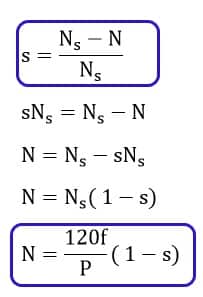
Where,
Ns = 120f/P- The Synchronous speed of the motor
f = Frequency
s = Slip of the motor
P = Number of poles.
Factors Affecting Speed of Induction Motor
- Frequency
- No. of poles
- Slip
Speed regulation of induction motors with a change in voltage alone has certain limitations, and with this method, the speed can be governed in the range of 90% to 100% of the rated speed.
Suppose the voltage is reduced below 90% of the rated voltage. In that case, the torque of the motor gets reduced drastically as the torque of the motor is proportional to the square of the applied voltage. At this reduced voltage, the motor can stall if the load demands more torque than the maximum torque-delivering capacity of the motor.

With the reduction of stator voltage, the flux in the air gap of the motor gets reduced, and, as a result, the torque-delivering capacity of the motor gets reduced.
Speed reduction up to the limited speed range with stator voltage reduction can be done if the driven load demands less torque at a reduced speed.
VVVF Speed Control of Induction Motor
Speed regulation by changing the frequency is the best method to govern the speed of the motor.
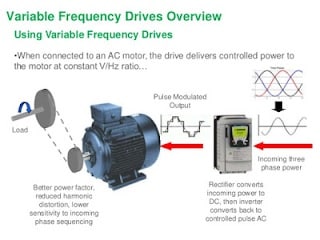
Stator voltage is also increased or decreased proportionately with an increase or decrease of the frequency with the Pulse width modulator(PWM) in the VVVF inverter to maintain the constant flux in the motor. The PWM waveform is given below.
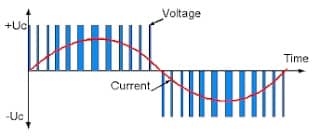
The width of the PWM waveform increases or decreases with an increase or decrease in the frequency. Thus, the smaller widths of PWM produce lower resultant voltage, and the larger pulse width produces higher resultant voltage.
How does the PWM VVVF Inverter maintain a constant V/f Ratio in VFD?
Let us understand the concept of keeping the V/f ratio constant in the VVVF drive by an example. If a 440 volts,1500 RPM, 50 Hz rating motor operates at 50 Hz, the motor’s speed is around 1480 RPM. The V/f ratio is (440/50) 8.8.
If the motor is to operate at 740 RPM, then the frequency is 25 Hz; corresponding to this frequency, the voltage is 220 Volts. In this case, the V/f ratio is (220/25) 8.8. In this way, the PWM VVVF inverter maintains the constant V/F ratio or constant flux; thus, the motor delivers constant torque.
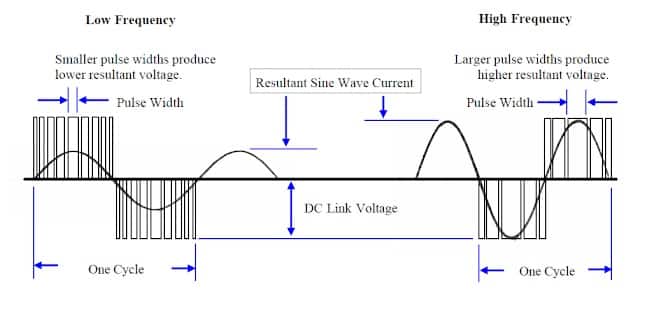
Thus, the inverter’s output voltage increases linearly with an increase in frequency. Thus, the V/f ratio is kept constant.
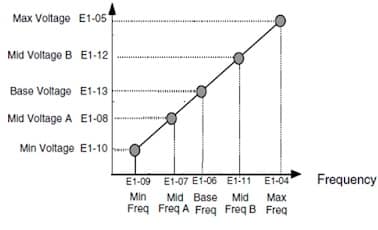
Relationship between Voltage and Frequency
From the above discussions, it is clear that the voltage and frequency increase or decrease in the same proportion in the VVVF drive to maintain the constant air gap flux in the motor. In other words, we can say that the voltage is proportional to frequency.
Mathematically, the voltage and frequency relationship is expressed as;
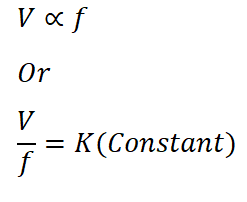
Why is the V/f ratio Constant in VVVF Drive?
The flux produced in the motor core can be calculated with the formula given below.
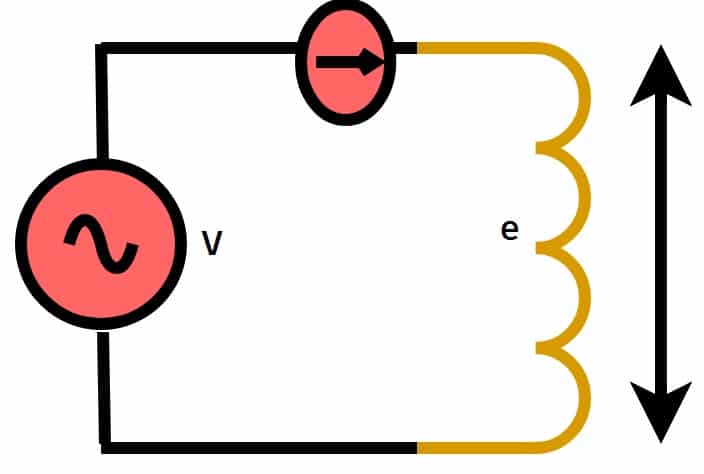
According to Faraday’s law of electromagnetic induction, the self EMF induced generated in the stator is expressed as;

Where erms is the back EMF/phase produced in the stator, f-frequency, and n-number of turns in the stator coil.
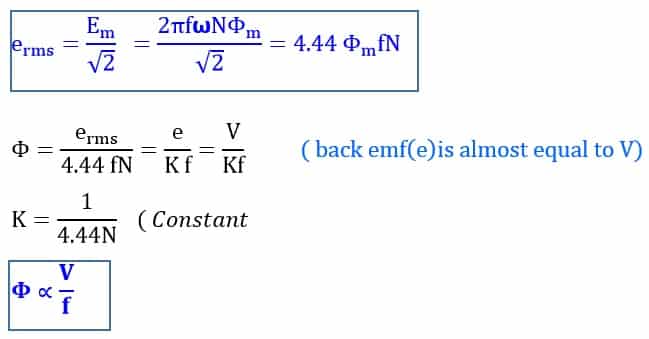
Thus, the flux in the stator core is proportional to the ratio of V/f. That is why we keep the v/f ratio constant in VFD or VVVF drive.
Effect on motor performance if V/f ratio or flux is not maintained constant by VVVF drive
If speed is increased by increasing frequency, the voltage has to be increased in the same proportion as the increase in frequency to maintain the constant flux in the core to avoid core overheating.
What happens if the flux is increased above the rated flux capacity?
If the voltage is not decreased with a decrease in frequency, the flux in the core will go above its rated design capacity, and the core of the motor will get saturated. The saturation of the core will lead to a rise in its temperature, and eventually, the winding insulation will break down.
For example, if we operate the motor with 440 Volts and a 50 Hz rating at full speed, then the ratio of V/f is 440/50=8.8. Now, we reduce the speed of the motor by half of its rated speed by changing the frequency only. In this case, the ratio of V/f is 440/25=17.6.
In the second case, core flux is two times the rated flux capacity. The core can not carry the flux above its capacity and will cause the core’s failure on account of core excessive heating of the core. This is why the v/f ratio is kept constant in the VVVF drive.
If the voltage is not increased with an increase in frequency, the flux in the stator core is reduced from its rated average flux rating, and the motor will not be able to produce the rated torque up to the base speed.
What happens if the flux is decreased below the rated flux capacity through VVVF drive?
In the application where speed is required to be increased above the motor’s base speed, the frequency is increased above 50 Hz. However, it is not practically possible to increase the voltage above 440 volts in the case of 440 Volts drives. Beyond the motor’s base speed, keeping the V/f ratio constant in VFD is impossible.
Speed control above base speed is possible by weakening the main stator flux as the V/ F ratio reduces.
The motor operates in the constant torque region up to the base speed( Rated speed). In this region, the power varies with an increase in speed. Beyond base speed, the flux weakens, and the motor operates in the constant power region. The constant power region is also called the flux weakening region.
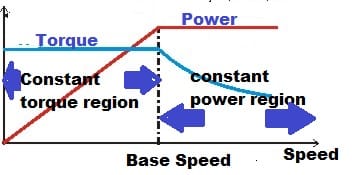
This procedure of speed control above the base speed of the motor can be used to increase the speed of the drives, which requires less running torque above the base speed operation. Increasing the speed above the base speed of the motor will lead to a decrease in the torque.
With flux weakening, the motor speed can be increased above 10 % of the rated base speed of the motor. However, the motor design data must be checked before speed regulation through flux weakening.
Final Words
The core of the induction motor can not carry more flux than the rated capacity, and the flux in the motor depends on the V/f ratio. Therefore, the V/f ratio must be kept constant through the VVVF drive.
Read Next:
Very informative and insightful article
Good lesson and explanation.
Thank you