The copper loss in the transformer is equal to the I2R loss. The copper loss is very important for the calculation of the transformer efficiency. The efficiency of the transformer can be improved by minimizing the copper loss and core loss.
In the transformer, the copper loss in the primary winding is Ip2Rp, and the copper loss in the secondary winding is Is2Rs loss, where Ip and Is are the primary and secondary current of the transformer and Rp and Rs are resistances of primary and secondary winding respectively.
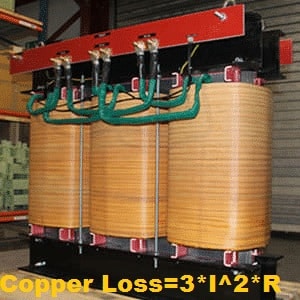
The copper loss is the wastage of power due to I2R loss in the transformer winding, and the energy is wasted as heat. As both primary and secondary currents depend upon the percentage loading of the transformer, the current increases as the load on the transformer is increased. With an increase in the primary and the secondary current, the copper loss in the transformer increases with the load.
The copper loss value is not constant, and it varies as the load on the transformer is increased. That is why the copper loss is also called a variable loss.
The total copper loss (I2R) in the transformer is load-dependent. The copper losses are proportional to the square of the RMS current flowing in the winding and also proportional to the resistance of the winding. The resistance of the conductor varies with the rise in temperature.
The copper loss in the transformer is proportional to the square of the current flowing through the winding. When the load on the transformer is increased, the copper loss varies because of the increased current and increased resistance caused by temperature rise.
The resistance value of the copper or aluminum must be corrected for the maximum permissible rise of the transformer winding at the rated capacity of the transformer. For example, the resistance of the winding measured at 30° C must be corrected for 75° C for an oil-cooled transformer.
For copper winding, the increased value of resistance with temperature can be calculated using the following formula.
RL=R0 [(TL+235)/(To+235)] |
Where,
RL = Resistance at TL temperature
R0 = Resistance at ambient temperature
RL = Operating temperature
T0 = Ambient temperature
For aluminum winding, the increased value of resistance with temperature can be calculated using the following formula.
RL=R0[(TL+225)/(To+225)] |
Read More : No Load Losses in Transformer |
Example of increase of resistance with temperature
Let the resistance of three HV winding of the transformer be 0.967 Ω,0.968 Ω, and 0.967 Ω at 23.8° C. The average HV winding resistance per phase at 23.8°C is;
=(0.967+0.968+0.967)/3 =0.967 Ω
The average HV winding resistance per phase at 75°C is;
RL = R0 * [(TL+235)/(To+235)]
R75 = 0.967 * [(75+235)/(23.8+235)]
= 0.967 * [(75+235)/(23.8+235)
R75 = 1.159 Ω
Percentage increase in resistance
=(1.159-0.967)/0.967 *100
= 19.85%
From the above calculation, it is clear that the resistance increases with an increase in temperature caused by the flow of current in a conductor.
Read More : Effect of Temperature on Resistance |
Copper Loss with Transformer Loading
Example of Copper Loss
The full load copper loss of a transformer is 1000 watts, and the copper loss at half load(50% Load) will be;
Pcu = ( % Load/100)2 x P
= ( 50/100)2 x 1000
= ( 1/2)2 x 1000
= 1/4 x 1000
Pcu = 250 Watts
Thus, the transformer’s copper loss at 50 % load is equal to 1/4 th of the full load copper loss.
The copper loss at 3/4 th load is equal to
Pcu = (3/4)2 x 1000 = 562.5 Watts
The copper loss at 1/4 th load is equal to
Pcu = (1/4)2 x 1000 = 62.5 Watts
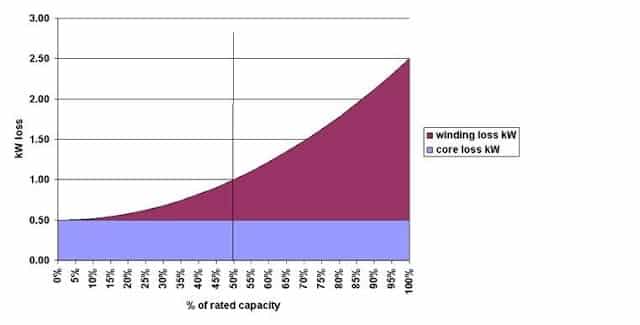
For a given transformer, the manufacturer can supply values for no-load loss, Pno-load, , and load loss, PLOAD.
The total transformer loss, Ptotal, at any load level can then be calculated from;
Ptotal = Pno-load+ (% load/100)2 x PLoad |
Where,
P no- load = No- load loss ( constant loss)
% Load = load on transformer
Pload = Copper loss at rated full load
How to Minimize Copper Loss in a Transformer
Copper loss can be reduced by using copper wire of the proper gauge for transformer winding. The thicker wire has less resistance and lower copper loss. A large cross-sectional area conductor winding should be used to minimize copper loss.
The wire used for transformer winding is chosen for its high conductivity. Copper wire has less resistance, so it has less copper loss compared to aluminum conductors.
Copper loss can be minimized by vacuum pressure impregnation of the transformer. The transformer winding is kept in a vacuum, and high-pressure varnish is passed so that air gaps, if any, are filled.
The transformer, which is used for high-frequency applications, needs to be designed in such a way as to have a lower skin and proximity effect. The conductor area reduces due to the skin and proximity effect, and thus, the resistance of the conductor increases, and it offers higher copper loss.